-
- News
- Books
Featured Books
- smt007 Magazine
Latest Issues
Current IssueSupply Chain Strategies
A successful brand is built on strong customer relationships—anchored by a well-orchestrated supply chain at its core. This month, we look at how managing your supply chain directly influences customer perception.
What's Your Sweet Spot?
Are you in a niche that’s growing or shrinking? Is it time to reassess and refocus? We spotlight companies thriving by redefining or reinforcing their niche. What are their insights?
Moving Forward With Confidence
In this issue, we focus on sales and quoting, workforce training, new IPC leadership in the U.S. and Canada, the effects of tariffs, CFX standards, and much more—all designed to provide perspective as you move through the cloud bank of today's shifting economic market.
- Articles
- Columns
- Links
- Media kit
||| MENU - smt007 Magazine
Estimated reading time: 4 minutes
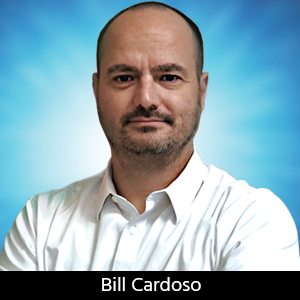
X-Rayted Files: My Favorite BGA Assembly Ever
In the early 1980s, Motorola and IBM introduced a novel package that allowed a high number of input and outputs with a large pitch in a small area, thus providing large savings in board real-estate. The ball grid array (BGA) was born. Initially in ceramic, by the late 1980s Motorola—and this time Citizen—brought to market the plastic BGA. This was the pivotal step needed to drop the cost of this packaging technology and to enable the electronic miniaturization wave that soon followed.
BGAs are touted as the ideal interconnect technology because it uses solder balls as leads that provide a reasonable level of self-alignment. That means that you have some tolerance in the placement accuracy, which is a direct function of the size and density of the BGA you’re working with. The BGA package also has considerable electrical and thermal advantages over other packaging technologies. The solder ball can be placed as near as possible to the pad of the die, thus minimizing the total pad to pad impedance. Also, the presence of many solder balls (which are great thermal conductors) under the entire package greatly reduces the thermal impedance of the BGA.
Figure 1: This BGA assembly is both the best and worse assembly ever. Worst because it has so many defects; best because it allows us to exemplify, in one image, most defects encountered in BGA assembly.
I’m an X-ray guy, so I don’t claim to be an expert in BGA assembly and rework. However, given the sheer number of clients we work with in the field, I’ve picked up quite a bit of knowledge. Here we’ll revisit some of the things we’ve learned over the years about BGA assembly and rework. In truth, it’s too much for one column, but we’ll put a dent in it, and follow up with more in a following column or two.
The use of BGAs usually leads to high manufacturing yields, so if you need to rework your board it’s very likely that you have an issue related to either materials or processes. The first thing we advise our customers to do is to check the bare board quality. Ensure that your PCB has solderable pads, and that those pads have a solder mask that is not encroaching excessively on the pad. The next step is to make sure the solder paste printing is done correctly. Avoid solder skips at all costs, and if needed, include a 3D or 2D solder paste inspection step until this process is under control.
If you have a high-quality bare board paired with a smooth solder paste application process and you’re still having problems with your BGA assembly, it’s time to look at the solder reflow process. The fact that BGAs are great at conducting heat through solder balls is both good and bad: good for the thermal management of the electronic components inside the BGA package, bad for assembling it. That's why you need to carefully profile the fully assembled board to minimize the temperature gradients between the middle and outer regions of the BGA. How do you do that? There are several methods that the rework station companies suggest. Simply put, these methods include using thermocouples around the BGA to map the temperature profile of the package. In other words, so that the rework machine knows that if it measures 240°C at the top nozzle (for SnPb), the BGA solder ball is at 220°C. This 20°C delta is not atypical. We will cover the other assembly issues—stencils, solder paste chemistry, cleaning—in the following section where we discuss BGA assembly X-ray inspection.
So, you went through the whole assembly process and the BGA looks amazing sitting on the board. Unfortunately, looks can be deceiving in this business. BGAs hide their problems very well, so you do need an X-ray machine to look through the package to assess the quality of the assembly. The X-ray image in Figure 1 is the perfect example of the best – and at the same time worst – BGA assembly we’ve ever seen. It’s the worst because it has every single assembly problem you can find in a BGA assembly. It’s also the best because it is a great educational tool, since it allows us to show you all these problems in a single image.
I hope you’ll find this review useful, as we can sometimes forget how much we’ve learned over the years. Before we start listing all the issues with the BGA in Figure 1, let us check what a good assembly looks like, as seen in Figure 2. You’ll notice all the balls in this image are properly collapsed, there are no opens or shorts and voiding is minimal. There is some shape deformation, but not enough to cause any trouble. In short, that’s the image you want to see of your BGA assembly. In my next column, we’ll dig into Figure 1, and address each of its problems and how to address them.
Dr. Bill Cardoso is CEO of Creative Electron.
More Columns from X-Rayted Files
X-Rayted Files: Best Practices in Buying MachinesX-Rayted Files: ’23 and Me?
X-Rayted Files: Battery-Powered Advancements Keep on Ticking
X-Rayted Files: What’s Cooler Than X-ray?
X-Rayted Files: My Favorite BGA Assembly Ever, Part 3
X-Rayted Files: My Favorite BGA Assembly Ever, Part 2
X-Rayted Files: Smart vs. Intelligent SMT Factory
X-Rayted Files: X-ray Everything!