-
- News
- Books
Featured Books
- smt007 Magazine
Latest Issues
Current IssueSupply Chain Strategies
A successful brand is built on strong customer relationships—anchored by a well-orchestrated supply chain at its core. This month, we look at how managing your supply chain directly influences customer perception.
What's Your Sweet Spot?
Are you in a niche that’s growing or shrinking? Is it time to reassess and refocus? We spotlight companies thriving by redefining or reinforcing their niche. What are their insights?
Moving Forward With Confidence
In this issue, we focus on sales and quoting, workforce training, new IPC leadership in the U.S. and Canada, the effects of tariffs, CFX standards, and much more—all designed to provide perspective as you move through the cloud bank of today's shifting economic market.
- Articles
- Columns
- Links
- Media kit
||| MENU - smt007 Magazine
Estimated reading time: 4 minutes
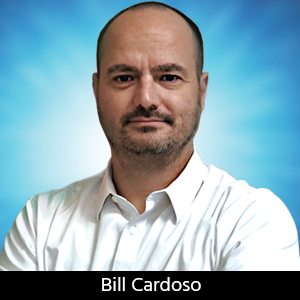
X-Rayted Files: My Favorite BGA Assembly Ever, Part 2
One of the most notorious component failures in manufacturing is a faulty ball grid array (BGA). Any line manager or engineer will tell you that there are too many things that can cause a BGA to fail. When a BGA is installed on a circuit board in a factory, it is visually checked for proper alignment. If it passes this simple test some might assume all is well. However, even a board that passes a cursory exam can still be terribly flawed. Because the BGA is a bottom terminating component, examination for quality of the connection cannot be seen with optical tools. To make sure there is a good connection between the BGA and the board, an X-ray inspection is essential. We’ll revisit my favorite X-ray image of a BGA that I shared in my last column and dig into the details of how to address its many problems.
Figure 1: This BGA assembly is both the best and worse assembly ever: Worst because it has so many defects; best because it allows us to exemplify, in one image, most defects encountered in BGA assembly.
Quite honestly, I never get tired of this image (Figure 1), and at the same time, I hope I never come across another like it again. With experience, and advancements in inspection tools, the industry has gotten increasingly better at avoiding these types of defects. Conversely, with packages getting increasingly smaller, these challenges do still exist. So, let’s review some of the problems we see in Figure 1 and how best to address them.
We’ll start with coplanarity. Imagine two planes, like two sheets of paper, perfectly flat. Now imagine you place these two sheets of paper on top of each other. The four corners of the top sheet will touch the four corners of the bottom sheet. That means they are coplanar; they’re perfectly parallel to each other. Now gently lift one of the corners of the top sheet. You have just created a coplanarity problem, a common issue in BGA assembly caused by either assembly misalignments or by popcorning due to trapped moisture in the plastic BGA package.
Figure 2: X-ray image in Figure 1: Emphasis on the four corners and middle of the part.
Coplanarity is one of the trickiest problems to diagnose because it requires the inspection of the whole BGA. A single area of the component will not tell you the whole story. However, as we analyze the X-ray images of all four corners and the center of the BGA, the story starts to clarify, as we can see in Figure 2. The solder balls in the top right corner are elongated, also called hourglass-shaped. As we move to the bottom of the BGA, the solder balls are barely touching the board—and some are not. These X-ray images in Figure 2 show that the BGA is not parallel to the board, requiring it to be reworked.
Short circuits, or “shorts,” are identified by a solder bridge between two or more solder balls. This defect is easily identified in the X-ray image, as seen in Figure 3. The root cause of this problem is diverse. One common cause is incorrect solder deposition, either too much solder deposited or located in the wrong place in between the pads. Another can be misalignment between BGA and board which can cause solder balls to short. Defective solder mask can also cause shorts if the mask is not properly deposited on the board. I know, I’m a broken record, but all these issues can be caught and addressed early with inspection, avoiding rework and scrap.
Perhaps the most challenging BGA assembly problem to identify—head in pillow (HIP)—has haunted engineers since the early days of the BGA history. Under special circumstances, as seen in Figure 4, the solder ball collapses, but not entirely. This partial collapse allows the solder ball to rest on top of the pad (like a head on a pillow) and to make electrical contact. However, since the contact between solder ball and board pad is mechanical and not metallurgical, the integrity of this electrical contact will depend on how the board is flexed. That’s the case you’ve experienced where the finished board passes all electrical tests in your facility, but it fails at the customer’s site. Temperature differences, for example, can cause the BGA to move, even slightly, and cause the solder ball to open.
One of the most common questions we get asked is how to find HIP. Although we keep improving our algorithms to allow you to find this defect automatically and unequivocally, it is still a manual process in the industry. To attain an image like the one in Figure 4, you need an X-ray inspection machine with high magnification, resolution, and geometric maneuverability. A wide range of geometric maneuverability will allow you to capture profile acquisitions (side view) as well as a tilted view of the BGA assembly. Some call it 2.5D inspection, which is the perspective view you see in Figure 1.
I hope you find this review useful. I’ll cover the remaining issues with this particular BGA in my next column. Stay tuned and stay well.
Dr. Bill Cardoso is CEO of Creative Electron.
More Columns from X-Rayted Files
X-Rayted Files: Best Practices in Buying MachinesX-Rayted Files: ’23 and Me?
X-Rayted Files: Battery-Powered Advancements Keep on Ticking
X-Rayted Files: What’s Cooler Than X-ray?
X-Rayted Files: My Favorite BGA Assembly Ever, Part 3
X-Rayted Files: My Favorite BGA Assembly Ever
X-Rayted Files: Smart vs. Intelligent SMT Factory
X-Rayted Files: X-ray Everything!