-
- News
- Books
Featured Books
- design007 Magazine
Latest Issues
Current IssueProper Floor Planning
Floor planning decisions can make or break performance, manufacturability, and timelines. This month’s contributors weigh in with their best practices for proper floor planning and specific strategies to get it right.
Showing Some Constraint
A strong design constraint strategy carefully balances a wide range of electrical and manufacturing trade-offs. This month, we explore the key requirements, common challenges, and best practices behind building an effective constraint strategy.
All About That Route
Most designers favor manual routing, but today's interactive autorouters may be changing designers' minds by allowing users more direct control. In this issue, our expert contributors discuss a variety of manual and autorouting strategies.
- Articles
- Columns
- Links
- Media kit
||| MENU - design007 Magazine
Estimated reading time: 3 minutes
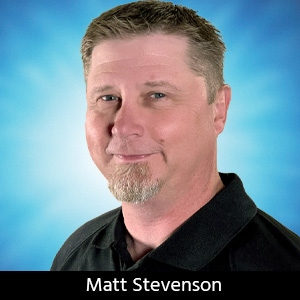
Connect the Dots: Controlled Impedance—The Devil is in the (Math) Details
Controlling impedance is critical to signal integrity and board performance in devices powering everything from high-speed digital applications to telecom and RF communication. It is common practice for designers to include impedance-related notes with their PCB designs and rely on the manufacturer to determine the proper trace parameters. This inherently passive methodology often leads to delay, cost overrun, and even batches of useless boards.
Designers can save time, money, and effort if they are aware of the impedance math as they design their board. Impedance math is heavily influenced by the distance an electrical signal must travel between components.
Comprised of a signal trace and a return path, a PCB transmission line transmits an electrical signal from one component to another. To function as a transmission line, the line length must be at least one quarter of the signal wavelength. For most transmission lines, the return path is a ground plane located on a layer above or below the signal trace.
Impedance comes into play when transmission lines are part of the PCB design. It is equivalent to the measure of resistance in a DC circuit and is also measured in ohms. The higher the impedance, the higher the input voltage must be to achieve a desired current in the circuit.
For high speeds greater than 100 MHz, frequencies and noise sensitive signals are used to control the characteristic impedance and are important to maintaining signal integrity. Mismatches in the impedance of these high-speed signals can cause signal reflections—meaning a portion of the signal is traveling in the opposite of the intended direction. The greater the difference in impedance, the greater the amount of signal reflected in one portion of the circuit, which will cause the signal to be noisy and could even cause a disruption of the signal.
Several factors that will influence the impedance of a circuit are:
- Cross-sectional area of the transmission line (height x width)
- The height of the dielectric material between the transmission line and the reference plane
- The dielectric constant of the dielectric material
- Spacing between the transmission lines (differential pairs)
The devil is in the mathematical details when it comes to controlling impedance. Documenting impedance requirements properly is more onerous than most people realize. Simply stating target impedance, trace requirements, and material tolerances often leaves knowledge gaps for the manufacturer and increases the likelihood of producing boards that do not make the cut during testing.
The math is the math when it comes to controlled impedance and it must be done at some point. Why not during the design phase? Using an impedance calculator will help designers build the right tolerances into their designs and avoid issues like signal mismatch. Impedance testing then becomes a double-check instead of the tool relied upon to determine if impedance documentation is correct.
When it comes to the math of controlling impedance, even simple equations really aren’t that simple. The following equation, taken from IPC-2141, is used for a single ended microstrip structures. It is a good demonstration of the influences on impedance. This is the simplest mathematical representation of impedance, and it can present up to a 7% error in calculations at high speeds.
W = Width of trace
T = Copper thickness
H = Dielectric Thickness
= Dielectric Constant (Dk)
Lack of specificity in the design notes can create risk during the transition from design to manufacture. The components of this equation all come with a +/- tolerance during manufacturing and raw material creation. For a PCB to have the desired result of matching or controlled impedance for critical structures, it is imperative that the PCB manufacturer understand these factors.
Manufacturing doesn’t happen in a vacuum and lessons learned from past experience will help reduce risk associated with controlling impedance. PCB manufacturers should be collecting data on every board produced, and they can leverage that in predictive models that will provide a good starting point to fill in documentation gaps and achieve the desired outcome.
A good partner for producing boards that reliably handle high-speed signals uses sound methods for process control and data collection. They fundamentally understand the influence of impedance and scrutinize signal transmission. But it is a two-way street. The designer should consider impedance factors in advance of manufacture. Matching the material characteristics (Dk), targeted layer spacing, and impedance needs during the design phase will make the process go more smoothly and help avoid costly rework.
This column originally appeared in the August 2022 issue of Design007 Magazine.
More Columns from Connect the Dots
Connect the Dots: How to Avoid Five Common Causes of Board FailureConnect the Dots: Sequential Lamination in HDI PCB Manufacturing
Connect the Dots: The Future of PCB Design and Manufacturing
Connect the Dots: Proactive Controlled Impedance
Connect the Dots: Involving Manufacturers Earlier Prevents Downstream Issues
Connect the Dots: Stop Killing Your Yield—The Hidden Cost of Design Oversights
Connect the Dots: Designing for Reality—Routing, Final Fab, and QC
Connect the Dots: Designing for Reality—Surface Finish