-
- News
- Books
Featured Books
- design007 Magazine
Latest Issues
Current IssueProper Floor Planning
Floor planning decisions can make or break performance, manufacturability, and timelines. This month’s contributors weigh in with their best practices for proper floor planning and specific strategies to get it right.
Showing Some Constraint
A strong design constraint strategy carefully balances a wide range of electrical and manufacturing trade-offs. This month, we explore the key requirements, common challenges, and best practices behind building an effective constraint strategy.
All About That Route
Most designers favor manual routing, but today's interactive autorouters may be changing designers' minds by allowing users more direct control. In this issue, our expert contributors discuss a variety of manual and autorouting strategies.
- Articles
- Columns
- Links
- Media kit
||| MENU - design007 Magazine
Estimated reading time: 4 minutes
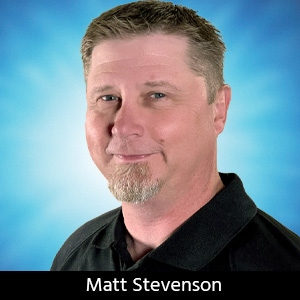
Connect the Dots: Demystifying Multilayer PCBs
As handheld and wearable technology become vital tools for industries ranging from health services to law enforcement, innovation increasingly coincides with PCBs getting smaller. For these devices, multi-layered PCBs offer requisite functionality for boards occupying a small space.
Multilayer PCBs enable more circuitry, components, and functionality to fit in a smaller space, as compared to single-layer or double-sided PCBs. Without them, miniaturization would be much more challenging and many of our coolest projects would rapidly become too clunky and unwieldy.
Though multilayer PCBs are becoming more common, many designers still have limited experience with multilayer board design. This can make the prospect of attempting such a design seem daunting, but multilayer boards do not have to be a hassle. Just think of them as multiple single-layer boards stacked together.
Sound design processes for multilayer boards mirror that of single-layer PCBs: Choose the right CAD tool to optimize design capabilities and best support the transition from design to manufacture. Look for design tools that will confirm design integrity and perform design rule checks.
Following established best practices for design of multilayer PCBs means becoming familiar with multilayer design tips and guidelines provided by the CAD tool, gaining knowledge about tolerances and components unique to multilayer boards, and knowing the manufacturer’s requirements for multilayer designs.
It is also a good idea to understand how multilayer boards are manufactured. The process, though complex, is easy to explain. Let’s break it down into a series of easy steps by looking at the assembly of an eight-layer PCB.
1. Grouping the Layers
The internal layers are grouped into pairs. For an eight-layer build, layers 2 and 3 are paired together, as are layers 4 and 5, and layers 6 and 7. What about layers 1 and 8? As they are on the outside, they’ll be added later.
2. Imaging the Layers
These pairs are imaged together onto both sides of a copper-clad laminate core, creating three distinct double-sided inner layer panels. This image is a representation of the copper image defined by the electronic data for each copper layer.
3. Etching the Images
Once the layers are all imaged, they’ll be etched. Etching removes the unwanted copper cladding, which creates spaces while simultaneously defining traces and pads.
4. Inspecting the Etched Layers
After etching is complete, the layers are inspected to ensure that etched images are defect-free.
5. Preparing for Lamination
The defect-free etched layers are then prepared for the lamination process using a chemical process that roughens up the copper to make sure it bonds to the prepreg.
There are several different names for this chemical process, including oxide, black oxide, and alternative oxide, to name a few.
6. Laying Up and Pressing the Layers
Once the oxide process is finished, the inner layers of the PCB are ready to be laid up and pressed into a single panel. A multilayer layup starts with preparing the lamination book. This book contains top and bottom plates made from steel, steel pins for alignment, thermal lagging material, stainless steel shims, PTFE release sheets, and, of course, the manufacturing panels.
7. Creating the Manufacturing Panels
The manufacturing panel is created by placing copper foil onto the alignment pins followed by prepreg layers. Prepreg is short for “pre-impregnated,” which refers to a partially cured glass-reinforced epoxy resin in sheet form.
The prepreg has two functions. First, it bonds the external foil to the adjacent copper layer and creates the dielectric insulator between these layers. Prepreg comes in several thicknesses to help match the electrical requirements of the design.
Note that the copper foil in this step becomes the eighth layer in an eight-layer PCB design.
8. Applying the Layers
In this step, each etched and oxidized core is placed on top of the previous core’s prepreg until the top layer is reached, where copper foil is applied again.
9. Assembling the Book
Finally, the completed layers are assembled into books. Depending on overall panel thickness, multiple panels can be contained within a single book. Separator sheets are placed between the panels to keep them from sticking together. In addition, shims can be added to evenly distribute pressure and maintain a consistent flatness across panels.
Thermal lagging material is generally placed between the steel plates on either end of the book and the first panel. This helps control the heat flow at a predictable rate into the manufacturing panels during lamination.
10. Pressing the Book
Finally, using heat and mechanical pressure under vacuum, the prepreg is heated up and the epoxy liquefied in order to distribute it evenly. The epoxy then cools and hardens, bonding all the layers into a single panel.
The PCB is now ready to have holes drilled into and through it, creating a finished multilayer PCB.
Designing multilayer boards will become increasingly common, and it makes sense for designers of every experience level to become more familiar with best practices.
This column originally appeared in the January 2023 issue of Design007 Magazine.
More Columns from Connect the Dots
Connect the Dots: Sequential Lamination in HDI PCB ManufacturingConnect the Dots: The Future of PCB Design and Manufacturing
Connect the Dots: Proactive Controlled Impedance
Connect the Dots: Involving Manufacturers Earlier Prevents Downstream Issues
Connect the Dots: Stop Killing Your Yield—The Hidden Cost of Design Oversights
Connect the Dots: Designing for Reality—Routing, Final Fab, and QC
Connect the Dots: Designing for Reality—Surface Finish
Connect the Dots: Designing for Reality—Solder Mask and Legend