-
- News
- Books
Featured Books
- design007 Magazine
Latest Issues
Current IssueAll About That Route
Most designers favor manual routing, but today's interactive autorouters may be changing designers' minds by allowing users more direct control. In this issue, our expert contributors discuss a variety of manual and autorouting strategies.
Creating the Ideal Data Package
Why is it so difficult to create the ideal data package? Many of these simple errors can be alleviated by paying attention to detail—and knowing what issues to look out for. So, this month, our experts weigh in on the best practices for creating the ideal design data package for your design.
Designing Through the Noise
Our experts discuss the constantly evolving world of RF design, including the many tradeoffs, material considerations, and design tips and techniques that designers and design engineers need to know to succeed in this high-frequency realm.
- Articles
- Columns
- Links
- Media kit
||| MENU - design007 Magazine
RF Antenna Design on the Bleeding Edge
July 13, 2023 | Andy Shaughnessy, Design007 MagazineEstimated reading time: 2 minutes
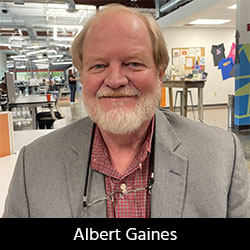
At SMTA Atlanta Tech Expo and Forum, I met with PCB designer Albert Gaines, owner of HiGain Design Services. Albert has been working on some really interesting, fragmented aperture antenna designs, and some of this stuff is really pushing the limits.
Albert and I discussed his work with RF, the differences between COTS and custom antennas, and his efforts to educate engineers about what they can and can’t do.
Andy Shaughnessy: Hi, Albert. Good to see you. I understand you’re doing some pretty interesting antenna design work. Tell us about it.
Albert Gaines: We're doing some really fancy designs, compared to what we used to do; we’re doing the sequential lay-up up of board layers with Rogers and other types of high-frequency laminates. They are actually back drilling, filling, and planarizing blind vias on internal layers, and then stacking materials as we need them for the dielectrics we need. Instead of depending on this particular core, we're actually using a single layer of double layer cores, stacking up sometimes two or three layers of special prepreg.
Then it gets pretty interesting. This is all about trying to get away from having a large parabolic antenna. You have a flat circuit board with all these receivers or transmit elements all over it, and we basically create a grid. It’s like the dot matrix of your LED TV—they get signals from each one of those combined and through software and then get an antenna. The largest one so far has a 242-transmitter array on one side and a 242-receiver array on the other side.
Shaughnessy: Who are the typical customers for this sort of thing?
Gaines: As you can expect, there are some big players in this market. There is still a great push to get satellite access more transportable and smaller. Some customers are looking at it from a commercial standpoint, like the trucking or the airline industry. It’s just a portable antenna for wherever you might need it; you can open up a case, lay it on the ground or just take it out, mount it on a truck or whatever. The whole antenna structure is about 40" x 30". They are also developing smaller arrays for specific applications.
It’s interesting when you start working with 4-mil spaces and other small features. I always tell everybody that my favorite button is Zoom, but it's relative to whatever space you have to work with, and when you see a board that’s 40" x 30"—wow, that's a pretty big element.
But it's been very interesting, and the technology has really changed. We have some good board shops that we're working with, and they’re willing to push the envelope in a niche market. It has opened my eyes over the last couple of years about what can be done in a circuit board environment, as opposed to limitations you are put on by an average board shop.
To read this entire conversation, which appeared in the July 2023 issue of Design007 Magazine, click here.
Suggested Items
Excellon Installs COBRA Hybrid Laser at Innovative Circuits
06/23/2025 | ExcellonExcellon is pleased to announce the successful installation of a second COBRA Hybrid Laser System at Innovative Circuits, located in Alpharetta, Georgia. The Excellon COBRA Hybrid Laser System uniquely combines both UV and CO₂ (IR) laser sources on a single platform—making it ideal for high-density prototype and production printed circuit boards (PCBs).
Gorilla Circuits Elevates PCB Precision with Schmoll’s Optiflex II Alignment System
06/23/2025 | Schmoll MaschinenGorilla Circuits, a leading PCB manufacturer based in Silicon Valley, has enhanced its production capabilities with the addition of Schmoll Maschinen’s Optiflex II Post-Etch Punch system—bringing a new level of precision to multilayer board fabrication.
The Evolution of Picosecond Laser Drilling
06/19/2025 | Marcy LaRont, PCB007 MagazineIs it hard to imagine a single laser pulse reduced not only from nanoseconds to picoseconds in its pulse duration, but even to femtoseconds? Well, buckle up because it seems we are there. In this interview, Dr. Stefan Rung, technical director of laser machines at Schmoll Maschinen GmbH, traces the technology trajectory of the laser drill from the CO2 laser to cutting-edge picosecond and hybrid laser drilling systems, highlighting the benefits and limitations of each method, and demonstrating how laser innovations are shaping the future of PCB fabrication.
Sierra Circuits Boosts High Precision PCB Manufacturing with Schmoll Technology
06/16/2025 | Schmoll MaschinenSierra Circuits has seen increased success in production of multilayer HDI boards and high-speed signal architectures through the integration of a range of Schmoll Maschinen systems. The company’s current setup includes four MXY-6 drilling machines, two LM2 routing models, and a semi-automatic Optiflex II innerlayer punch.
Driving Innovation: Traceability in PCB Production
05/29/2025 | Kurt Palmer -- Column: Driving InnovationTraceability across the entire printed circuit board production process is an increasingly important topic among established manufacturers and companies considering new PCB facilities. The reasons are apparent: Automatic loading of part programs, connection with MES systems and collection of production data, and compliance with Industry 4.0 requirements