-
- News
- Books
Featured Books
- design007 Magazine
Latest Issues
Current IssueProper Floor Planning
Floor planning decisions can make or break performance, manufacturability, and timelines. This month’s contributors weigh in with their best practices for proper floor planning and specific strategies to get it right.
Showing Some Constraint
A strong design constraint strategy carefully balances a wide range of electrical and manufacturing trade-offs. This month, we explore the key requirements, common challenges, and best practices behind building an effective constraint strategy.
All About That Route
Most designers favor manual routing, but today's interactive autorouters may be changing designers' minds by allowing users more direct control. In this issue, our expert contributors discuss a variety of manual and autorouting strategies.
- Articles
- Columns
- Links
- Media kit
||| MENU - design007 Magazine
Estimated reading time: 5 minutes
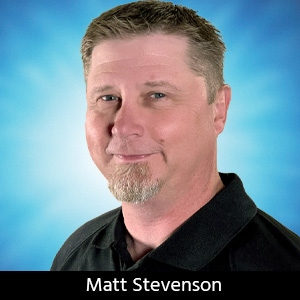
Connect the Dots: Controlled Impedance and Calculations for Microstrip Structures
Modern high-speed and RF PCB design is an exciting field but it comes with its own set of challenges. Signal integrity, performance, and crosstalk become major concerns. Designers for these types of projects need to learn how to control electromagnetic interference (EMI) and compatibility (EMC), which means utilizing some interesting math and calculations.
These designs rely on controlling impedance to improve signal integrity and reduce EMI. PCB traces are there to conduct signals from one component or device to another, and when the impedance of those traces matches the characteristic impedance of a transmitting device, the maximum signal can be sent. This method limits both signal reflection and interference. However, beyond impedance there are other critical values and calculations that the designer must understand.
An impedance structure refers to physical configuration of components on a PCB, including microstrips, striplines, and coplanar waveguides. The microstrip line is the most common type of impedance structure: an external trace separated from a plane layer by a dielectric material. Microstrips are compact, allowing for greater design flexibility. They are also easy to probe and measure, making them suitable for easy fabrication and a wide range of applications.
Figure 1 shows a microstrip trace with width (w) and thickness (t). The dielectric material separating the trace from the plane has an overall thickness of h and a dielectric constant of εr.
Key Calculations Involved in Microstrip Design
Incorporating a microstrip line into a PCB requires calculations involving the analysis and design of transmission lines which are widely used in microwave and RF circuits. Characteristic impedance, the effective dielectric constant, and propagation are all critical pieces of information for the designer to understand.
Characteristic Impedance
Characteristic impedance (Z0) is the ratio of voltage to current in a transmission line and is an important parameter for determining the performance of microstrip circuits (Figure 2).
The characteristic impedance of a microstrip line can be approximated as:
h is the height of the substrate
w is the width of the trace
t is the thickness of the trace
Effective Dielectric Constant
Effective dielectric constant (εr) is the relative permittivity of the substrate material as seen by the signal on the microstrip line (Figure 3). For a microstrip line, the dielectric of the material and the dielectric of the surrounding air are the two values that are used to understand the effective constant.
εr1 is the permittivity of the substrate
εr2 is the permittivity of the air above the substrate
h is the is the height of the substrate
w is the width of the trace
Velocity of Propagation
The velocity of propagation (vp) is the speed of a signal as it travels down the microstrip line—or through any transmission line. It is typically expressed as a fraction of the speed of light, due to the effective dielectric constant of the substrate material (Figure 4).
c is the speed of light in a vacuum: 300 million meters/second
Propagation Delay
Propagation delay (τ) is the time taken for a signal to travel down the microstrip line. This is a relatively straightforward equation using the velocity of propagation and the distance the signal must travel (Figure 5).
L is the length of the microstrip line
Putting It Into Action
To illustrate how all these equations come together, let us examine how to calculate the numbers around a fairly common design structure: a 50Ω microstrip. For this microstrip configuration, we will use the following values:
Z0 = 50Ω
h = 0.0146" 1
t = 0.0024"
εr1 = 4.1
εr2 = 1.00 2
The first step is to calculate the effective dielectric constant (εr) for the external trace using the equation we discussed previously. Make sure you keep track of the output. In our example, we get:
εr = 2.808
Next, we must determine the required trace width to meet our 50Ω target. The width of the required trace will depend on the thickness of the copper layer on the PCB (t), the effective dielectric constant (εr), and the desired characteristic impedance (Z0).
We next use the characteristic impedance equation discussed earlier and solve for trace width (w). You might need to use a calculator or equation solver to calculate w 3.
By inputting the values we have calculated already, we find:
w = 0.030" (30 mils)
This requires another look. The resulting 30-mil trace is a little on the wide side for most designs. However, if controlling impedance is critical, then this is the measurement the design must account for. If a 30-mil trace will absolutely not work, other variables can be modified to still achieve the required impedance. For example, both material type and thickness could be altered to meet our target numbers.
For Fun
Since length is such an important part of the equation, it is interesting to calculate the propagation delay for a 3"- and 6"-trace. Here’s how the numbers work out:
For 3" trace, τ = 4.2 x 10-10 seconds
For 6" trace, τ = 8.5 x 10-10 seconds
Design Tips
- Trace Thickness (t): The thickness of the trace should be at least 1-ounce copper (0.0014") to ensure good current handling capability. In this example, we used 1-ounce copper (0.0014") plated to 0.0024".
- Trace Spacing Calculation: To minimize crosstalk between traces, make sure the spacing between those traces is at least three times the height of the dielectric substrate.
Tying It All Together
These calculations will help you create 50Ω traces for high-speed and RF PCBs that provide good signal integrity and minimize loss. In addition, with these equations in your toolkit, you are ready for any variation in impedance control. However, remember that PCB substrate quality and manufacturing process accuracy will have a big impact on the performance of the transmission lines in RF circuits.
We look forward to seeing what you will design next.
References
- This is the standard dielectric thickness of some manufacturers’ 6-layer stackup.
- Don’t forget to account for air.
- It’s time to dust off those rules for manipulating natural logs.
This column originally appeared in the December 2023 issue of Design007 Magazine.
More Columns from Connect the Dots
Connect the Dots: How to Avoid Five Common Causes of Board FailureConnect the Dots: Sequential Lamination in HDI PCB Manufacturing
Connect the Dots: The Future of PCB Design and Manufacturing
Connect the Dots: Proactive Controlled Impedance
Connect the Dots: Involving Manufacturers Earlier Prevents Downstream Issues
Connect the Dots: Stop Killing Your Yield—The Hidden Cost of Design Oversights
Connect the Dots: Designing for Reality—Routing, Final Fab, and QC
Connect the Dots: Designing for Reality—Surface Finish