-
- News
- Books
Featured Books
- design007 Magazine
Latest Issues
Current IssueAll About That Route
Most designers favor manual routing, but today's interactive autorouters may be changing designers' minds by allowing users more direct control. In this issue, our expert contributors discuss a variety of manual and autorouting strategies.
Creating the Ideal Data Package
Why is it so difficult to create the ideal data package? Many of these simple errors can be alleviated by paying attention to detail—and knowing what issues to look out for. So, this month, our experts weigh in on the best practices for creating the ideal design data package for your design.
Designing Through the Noise
Our experts discuss the constantly evolving world of RF design, including the many tradeoffs, material considerations, and design tips and techniques that designers and design engineers need to know to succeed in this high-frequency realm.
- Articles
- Columns
- Links
- Media kit
||| MENU - design007 Magazine
Estimated reading time: 8 minutes
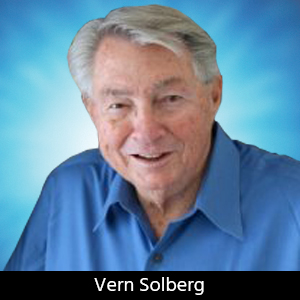
Designers Notebook: What Designers Need to Know About Manufacturing, Part 1
The designer needs to have a working understanding of two key manufacturing operations: basic circuit board fabrication procedures and assembly process practices. For printed circuit board manufacturing, the number of steps required to produce the printed circuit board correlates to the circuit board's complexity. Greater process complexity in fabricating the circuit board equates to increased costs. To develop any portion of the electronic product, the designer must apply the design for manufacturing (DFM) principles established in the industry. In fact, DFM should always be the goal of the design engineer. It encompasses a wide range of disciplines that must be considered during the planning phase of any product.
The critical elements of DFM principles include:
- Design for fabrication efficiency (DFF)
- Design to enable electrical test (DFT)
- Design for assembly processing (DFA)
- Design for end product reliability (DFR)
Planning for PCB Fabrication
Printed circuit boards may be as simple as having a single- or double-copper layer or require a more complex multilayer construction. The fabrication processes implemented will commonly use the same basic materials, but fabrication processing can differ a great deal from one manufacturer to another. Although many circuit board fabricators will use similar chemistries and process systems to build the board, there can be significant differences in how they manage and control their processes.
There are four primary material elements for PCB fabrication:
- Substrate. The first and most important is the base substrate, usually made of woven glass-fiber reinforcement and epoxy. This material is used for the majority of circuit board applications because it provides a physically stable dielectric platform for both circuit interconnect and component mounting.
- Copper layer. Depending on the substrate base material, this electrically conductive layer will be a copper foil laminated to one or both surfaces of the dielectric core.
- Solder mask. Applied on the outer surfaces after circuit imaging and chemical etching, a polymer coating applied over the bare copper circuit features on the circuit board surface.
- Surface marking. Silkscreen and ink-jet printing (also known as legend or nomenclature printing) is applied on the component side of the board to furnish the assembly part numbers, source identification, material content, and component reference.
- Circuit design engineers must also consider several governing criteria. Minimizing unnecessary complexity, specifying the most suitable base materials, and applying proven circuit design principles that will enable efficient assembly processing. The goal is to provide an end product that meets its intended performance criteria and furnishes reliable operation throughout its life cycle.
Circuit Complexity Assessment
When assessing printed circuit board design complexity, first consider the component area and board area ratio. While the less complex circuit may only be the single- or double-copper-layer circuit, the component area to circuit board surface area ratio may not be workable. Conductor routing follows component placement. Clearance protocols must be established in advance: the space separating via-hole lands, microvia lands and/or component attachment lands. Spacing provided between surface mount land pattern and hole lands is referred to as “channel width.” The channel widths for routing active and array-configured semiconductors will be mathematically calculated using the terminal pitch (center-to-center distance) and the size of the land pattern. This provides the maximum number of conductors that can be routed between each channel (conductors per channel). The spacing separating the circuit conductors must consider the established minimum electrical clearance required for fabrication process variables, solder-mask surface adhesion, land pattern features, via-hole lands, and other fixed elements on the board.
Narrow conductors routed in parallel may have a space equal to the conductors’ width; however, wider current-carrying and ground conductors will probably require a significantly wider spacing between adjacent conductors. Three circuit routing complexity levels for the multilayer printed circuit board are compared in Table 1.
The width of conductors that function as power and ground paths will increase to accommodate the level of current flowing through them. The best guide for establishing conductor width and copper thickness is detailed in IPC-2152, Standard for Determining Current-Carrying Capacity in Printed Board Design.
When the surface area for component interface is restricted, it may justify adopting multilayer or a multilayer sequential build-up (SBU) PCB fabrication to improve power and ground distribution and allow more efficient sub-surface circuit interconnect capability.
Base Material Selection
Circuit board fabricators and circuit board material suppliers have worked together in establishing a series of standards documents to eliminate misunderstandings between manufacturers and purchasers, facilitating interchangeability and end product improvement. Standards allow the fabricator to set up their processes that will meet the quality and reliability criteria defined by the customer company. A standard that focuses on materials for printed circuit board fabrication, for example, is IPC-4101, Specification for Base Materials for Rigid and Multilayer Printed Boards. This document is prepared and maintained by IPC member companies. The working members developing and maintaining these standards are experienced in all segments of the product development: engineers, designers, material suppliers, printed circuit board fabricators, and assembly service providers.
IPC-4101 includes the requirements for both laminates and prepreg base materials used primarily for rigid or multilayer printed circuit boards.
Key properties include:
- Dimensional stability and flexural strength
- Coefficient of thermal expansion (CTE)
- Limits of thermally induced Z-axis expansion
- Glass transition temperature (Tg)
- Thermal conductivity and flammability rating
At the end of IPC-4101 is a series of detailed specification sheets that furnish key requirements for both laminate and prepreg materials. The specification sheets are classified by a specific reinforcement type, resin system, and/or construction. Each variation is assigned a unique specification sheet number and includes copper foil peel strength, resistivity, moisture resistance, moisture absorption potential, and the maximum kV level resulting in dielectric breakdown.
Prepreg sheet materials are furnished when adding additional (buildup) circuit layers onto the partially processed base or core substrate. The prepreg is a thin woven glass fiber cloth impregnated with a resin bonding agent furnished to the circuit board fabricator as a partially cured dielectric sheet (referred to as B-stage or bonding ply) material. In preparation for joining the circuit board layers, the B-stage prepreg material is placed between the rigid laminate materials or as shown in Figure 1, between the copper-clad laminate base and the succeeding copper foil layers. The process for joining the multi-layer circuit uses specialized lamination systems employing both heat and pressure.
FR-4 Glass/Epoxy Laminate ($)
This family of glass-reinforced material developed for printed circuit fabrication has been (and will continue to be) the workhorse of interconnection technology. The materials are widely available, very versatile, and tailored to accommodate different product functions or applications: hand-held, portable electronic products to large multilayer system-level boards. The dielectric is defined as a high-pressure thermoset plastic laminate that exhibits, in a panel form, a robust strength-to-weight ratio and performs well in most environmental conditions.
- Glass transition temp (Tg): 150–200°C
- Surface resistivity: 104 MΩ minimum
- Dielectric breakdown: 40kV minimum
These attributes, along with good fabrication characteristics, make it a secure choice for a variety of electrical and mechanical applications, retaining its high mechanical values and electrical insulating qualities in both dry and humid conditions. Although all epoxy/glass laminates have similar physical attributes, the products that adopt these materials often have very different manufacturing focus and performance requirements.
Note: The acronym “FR” stands for flame retardant, denoting that the material comprises woven fiberglass cloth with an epoxy resin binder. The material complies with the Underwriters Laboratory Standard, UL94V-0, defined as glass fiber/epoxy composite with copper foil laminated on one or both sides.
Bismaleimide/Triazine (BT)/Epoxy Laminate ($$)
BT laminate is one of the preferred materials for products developed to operate in the more physically challenging environments and has proven ideal for semiconductor package substrate applications. The company that developed the material reports that, when compared to standard epoxy resin systems, the blending of bismaleimide/triazine with epoxy provides:
- Enhanced thermal and mechanical stability
- Improved electrical performance
- Furnishes a higher Tg (180°C)
- Lower coefficient of thermal expansion
- Improved electrical insulation in high humidity and temperature
Polyimide (PI)/Glass Laminate ($$$)
Polyimide-based laminates are comprised of a high-strength and high-temperature polymer material system engineered with an all-polyimide resin chemistry suitable for any electronic package application requiring uncompromised performance. Thermal stability of the polyimide composition and glass fiber reinforcement makes this material particularly attractive for products with stringent high-temperature operating requirements.
- Glass transition temp (Tg): 200°C minimum
- Surface resistivity: 6 x 104 MΩ
- Dielectric breakdown: 40kV
Note: The moisture absorption rate for PI materials is relatively high when compared to the FR-4 and B-T composites.
Special Application Laminates
Alternative dielectric formulations have evolved that can address the technical needs of a wide range of special applications. High-frequency laminate products, for example, are better known for cores with better high-frequency properties, such as PTFE (Teflon®) that has a wider range of Dk values than FR-4 material. The PTFE composite is more expensive than fiberglass, but is better suited for high operational frequencies, making the laminate a good choice for RF circuit boards.
- Low electrical signal and dielectric loss
- Excellent thermal management characteristics
- Broad range of Dk (dielectric constant)
- Low out-gassing (ideal for space applications)
- Enables improved impedance control
Comparing the commercial FR-4 to the PTFE (Polytetrafluoroethylene), the material is less likely to experience a dielectric breakdown when operating in extreme environmental conditions.
When selecting base materials for the circuit board, the designer must consider end-product safety. Government agencies, both domestic and international, have banned a number of elements considered a health hazard, for example, plating and soldering alloys that contain lead.
Part two of this series will focus on PCB fabricator-recommended design guidelines for efficient circuit board fabrication processing.
This column originally appeared in the January 2024 issue of Design007 Magazine.
More Columns from Designer's Notebook
Designers Notebook: Layer Stackup Planning for RF Circuit BoardsDesigners Notebook: Addressing Future Challenges for Designers
Designers Notebook: Impact of Advanced Semiconductor Packaging on PCB Stackup
Designers Notebook: Implementing HDI and UHDI Circuit Board Technology
Designer's Notebook: Heterogeneous Integration and High-density SiP Technologies
Designers Notebook: PCB Design and IPC-CFX for Assembly Automation
Designer’s Notebook: What Designers Need to Know About Manufacturing, Part 2
Designer’s Notebook: DFM Principles for Flexible Circuits