-
- News
- Books
Featured Books
- design007 Magazine
Latest Issues
Current IssueAll About That Route
Most designers favor manual routing, but today's interactive autorouters may be changing designers' minds by allowing users more direct control. In this issue, our expert contributors discuss a variety of manual and autorouting strategies.
Creating the Ideal Data Package
Why is it so difficult to create the ideal data package? Many of these simple errors can be alleviated by paying attention to detail—and knowing what issues to look out for. So, this month, our experts weigh in on the best practices for creating the ideal design data package for your design.
Designing Through the Noise
Our experts discuss the constantly evolving world of RF design, including the many tradeoffs, material considerations, and design tips and techniques that designers and design engineers need to know to succeed in this high-frequency realm.
- Articles
- Columns
- Links
- Media kit
||| MENU - design007 Magazine
Estimated reading time: 5 minutes
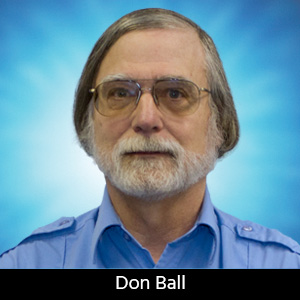
The Chemical Connection: Can Changing Spray Nozzles Improve My Etch Quality?
Whenever the need to improve etch quality due to tightening customer specifications arises, the inevitable question asked early on is, “Will going to a different type of nozzle or nozzle flow rate make my etch quality better?” Unfortunately, the answer is most likely, “Probably not.” (Sorry, folks.) So, why not?
The fluid dynamics of flow on a horizontal plate with turbulence is extremely complicated and spraying hot acid at high velocity onto a moving horizontal plate is about as turbulent as it gets. The main problem with a horizontal etcher is that the etchant is sprayed onto the top surface of the panel faster than it can flow off, so the spray doesn’t actually hit the surface of the panel—it hits the top of the puddle of etchant formed by the spray. The uniformity of the etch rate is affected by the thickness and velocity of the puddle. The puddle is thickest and moves the slowest in the center of the panel and gets gradually thinner and faster as the edges of the panel are approached. As a result, the etch rate is lower in the middle of the panel and faster around the edges, and etched line widths can vary significantly between the edges and center of a panel. This is nowhere near as big a problem on the bottom side of the panel as gravity removes the etchant on the surface of the panel almost as fast as it is applied.
So, what are the fluid dynamics on the top side of the panel that are causing the unequal etch rates between the center of the panel and the edges? When any fluid (gaseous or liquid) flows across a solid object, a boundary layer of static fluid forms where the fluid meets the surface of the solid. The thickness of the boundary layer (also known as the diffusion layer) helps determine the speed of any chemical reaction by controlling the time needed for fresh chemistry to diffuse through the boundary layer to the surface and the time for spent chemistry to move away from it. The thicker the boundary layer the slower the reaction. The thickness of the boundary layer is determined by such things as fluid viscosity, fluid density, and fluid velocity.
For spray etching, the viscosity and density will be constant, so the major factor is velocity. The equations for boundary layer thickness show that the higher the fluid velocity, the thinner the boundary layer is and the faster the etch rate. That is why the etch rate increases as the spray pressure increases. Increased spray pressure means higher fluid velocity across the panel. Thus, the boundary layer is thinner and the etch rate increases.
This also explains why the etched line widths decrease as the edge of the panel is approached. The fluid velocity increases toward the edges of the panel, the boundary layer gets thinner, and the etch rates increase slightly toward the edges of the panel. It should be noted that this same effect can be seen on the bottom side of the panel but is hardly noticeable because there is very little puddling effect on the bottom side.
Assuming the etcher has been properly designed for even spray coverage, what effect can it have to go to nozzles with a higher or lower flow rate or from cone nozzles to fan nozzles or vice versa? If you’re looking for a quick and easy improvement in your etch quality, you’ll probably be disappointed. Changing to a nozzle with the same spray angle but a different flow rate changes the average droplet size. Generally, a higher flow rate nozzle has a larger opening and produces a larger droplet. At first glance this might seem to be an advantage since a larger droplet has more mass and produces a higher impact force at the panel surface. You will probably see an increase in etch rate at the same spray pressure compared to the lower flow rate nozzle, but not much change in etch quality. This is because, while the droplet sizes get bigger for a higher impact force, the flow rate has also increased, leading to a deeper etchant puddle. The higher impact force verses the deeper puddle tend to cancel each other out.
Some have thought that changing to a lower flow rate nozzle with a smaller droplet size might be an advantage as the spaces between the lines get tighter and tighter. A smaller droplet size might be better at getting into smaller spaces. A 0.75 gpm (2.8 lpm), 70° cone spraying 40 psi (2.7 bar) has an average droplet size of around 950 µm compared to an average droplet size of about 1200 µm for a 1.5 gpm (5.7 lpm), 70° cone nozzle at the same pressure. Yes, the droplet size is smaller but still gigantic compared to a 50 µm space between circuit lines, so there probably won’t be much effect on etch quality. Also, the relationship between flow rate and droplet size still applies. Lower flow rates mean less puddle but with smaller droplet sizes and less impact force that tend to cancel each other out.
Cone nozzles vs. fan nozzles for etching has always been a favorite subject for debate ever since I started in the business in 1974. The argument in favor of fan nozzles has always been that they have a higher impact because the spray is directed at a much smaller area. Because of this, they should be more efficient at getting fresh etch solution to the panel surface through the puddle and therefore give a better etch quality.
A fan nozzle does have a higher impact/unit area at the surface, but the area of impact is long and narrow, so each part of the panel spends a relatively short time under the direct impact. The impact/unit area for the cone nozzle is much less but applied for a longer period of time over a much larger area. If you multiply the impact/unit area by the total area of the spray coverage for each nozzle with the same flow rate and spray angle, you will find that the total spray force is about the same.
Other variables must be considered in spray design, so the best spray design for cone nozzles is different from that for fan nozzles. Given the proper spray system design, I have never seen any difference in etch quality between cone and fan nozzles. The whole source of debate arose because fan nozzles don’t work as well in a system designed for cone nozzles and vice versa.
In conclusion, you probably won’t see much improvement in etch quality by just changing nozzles. However, it’s a relatively easy change to make so there is no harm in trying different nozzle combinations if you wish to satisfy your curiosity.
This column originally appeared in the December 2024 issue of PCB007 Magazine.
More Columns from The Chemical Connection
The Chemical Connection: Through-glass Vias in Glass SubstratesThe Chemical Connection: Reducing Defects in Circuit Board Production
The Chemical Connection: Common Misconceptions in Wet Processing
The Chemical Connection: Surface Finishes for PCBs
The Chemical Connection: Earthquakes, Astronauts, and Aquatics—A Lighter Look at the Past
The Chemical Connection: Better Fabs Attract a Better Workforce
The Chemical Connection: Getting the Best from Your Cupric Chloride Etchant
The Chemical Connection: Troubleshooting PCB Process Problems