-
- News
- Books
Featured Books
- design007 Magazine
Latest Issues
Current IssueProper Floor Planning
Floor planning decisions can make or break performance, manufacturability, and timelines. This month’s contributors weigh in with their best practices for proper floor planning and specific strategies to get it right.
Showing Some Constraint
A strong design constraint strategy carefully balances a wide range of electrical and manufacturing trade-offs. This month, we explore the key requirements, common challenges, and best practices behind building an effective constraint strategy.
All About That Route
Most designers favor manual routing, but today's interactive autorouters may be changing designers' minds by allowing users more direct control. In this issue, our expert contributors discuss a variety of manual and autorouting strategies.
- Articles
- Columns
- Links
- Media kit
||| MENU - design007 Magazine
Estimated reading time: 5 minutes
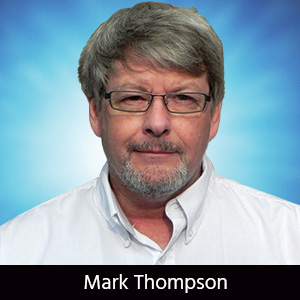
Timing is Everything in Controlled Impedance Fabrication
I want to start out this column a little differently by sharing a true story I heard when I was about 14 years old. In June 1970, the British Aerobatic Champion Neil Williams was practicing for the upcoming World Aerobatic Championships in Hullavington, England.
Neil was flying his single-seat Zlin Akrobat in a shallow pull-up at less than 2,000 feet when he heard a loud bang. The lower left wing bolt had broken and the wing began to fold over towards him. He had on no chute that day, as a chute just added weight and would not have helped at that altitude anyway.
This man had the presence of mind to realize his predicament, and in a split second he rolled the Zlin to the right in a semi-outside snap roll and locked the wing back into position.
BANG! It worked! He was still alive at less than 2,000 feet, but he was upside-down. He had to stay inverted to keep flying; the weight of the failed left wing was being held in place by the "top" wing bolt on that side. He then flew back to Hullavington inverted all the way.
On the approach, he flew a modified downwind, base and final inverted, ending up low and slow upside-down heading towards the runway, daring to un-weight the wing enough to descend more to get somewhere around 85 to 90 knots airspeed. Less than 10 feet off the ground, Neil did a half-outside snap roll and plopped the Zlin on her belly. He casually unlatched the canopy and walked away. Everyone who witnessed this aviation miracle was stunned.
Figure 1: Neil Williams' Zlin Akrobat after his crash in June 1970.
Neil's quick decisions saved his life. After the bolt broke, he timed his actions perfectly. Most importantly, he didn't take anything for granted.
And when you deal with your fabricator, you shouldn't take anything for granted either. (Did you like my segue?) I have been on this soapbox before about the importance of informing your fabricator of your desired end-results if jobs are impedance controlled. I don't mean merely indicating a material type or specifying dielectrics. Now, when many jobs are going through turnkey environments, late communication about impedance issues takes valuable time out of the fabrication process and can delay the delivery of product, leaving the end-user and the turnkey assembler unhappy.
This can be easily avoided by sharing impedance information about the job up front on a drawing or read-me file. A fabricator really needs to know only four things:
- What sizes are the impedance controlled traces?
- On which layers do they reside?
- What is the desired threshold?
- What tolerance is associated with this threshold?
The material callout should express both the Tg and the Td desired. This allows the fabricator some alternatives in selecting materials to meet your needs. Avoid handing off conflicting materials information--conflicts require clarification and cause delays.
Avoid specific one-number Dk callouts. Your Dk callouts should be expressed as an acceptable range, as there are variances in Dk between cores and pregs even within the same material type.
Because many fabricators charge a premium for impedance controlled jobs (we don't agree with that approach), customers often select a specific material and dielectric that has been premodeled and qualified to avoid calling out impedance control. As I have said, this is a huge risk for a few reasons:
- Unique reference plane scenarios may exist, such as 75 ohm external lines where "pass through" layers are common on the next adjacent plane.
- The customer fails to estimate the potential deviation from different Dk values between cores and pregs.
These are both small details, but they can mean the difference between passing and failing impedance.
While you're here, let me share one more aerobatic war story with you. I've had a few "incidents" while flying aerobatic planes--nothing like Neil Williams went through, but always interesting!
Once, when I was still learning to fly in Bellanca Decathalons and Citabrias, I was flying a Citabria and my father was flying our family's Spezio. We formed up for a bit and then broke off. I did a few loops and some crude aileron rolls. Still high at about 4,000 feet, I started into a snap roll and stopped too soon, ending up inverted nose down and semi-slow (around 90 mph). Because I still had plenty of room, I just throttled back and sucked the stick back in my lap, winding up doing a half-snap split-S.
My father remarked how pretty that move looked. It was MANY years later I confessed it was a screw-up! Then a few years ago, I had the opportunity and privilege to fly with aerobatic pilot Wayne Handley. I honestly thought I could fly as if I were 18 again, with the g-force tolerances I used to have. Big mistake.
I flew with Wayne in an Extra 300 L that morning, and I had never flown anything higher-performance than a Decathalon at that point. I was amazed at the effortless rolls, and the Cuban eights were like no roller coaster you could ever ride.
When I opted for doing some snap rolls, I undid myself. On a snap roll, Citabria and Decathalons break at about 45 degrees to the horizon and they're fairly benign. But the Extra 300 reared up its nose to about 90 degrees (straight up) before it broke and rolled around itself.
It felt like spinning into a wall at 120 mph. This was seriously exciting. On one snap, I corrected too soon--as I did years before in front of my dad--and I ended up doing a half-inside and half-outside snap.
As I said, timing is everything!
After only 15 minutes, my cheeseburger and orange pop, age, complacency and my outright lack of respect for an Extra 300 all conspired against me and gave me one heck of a case of the "wobblies." I felt as If I were doing snap rolls for the next 24 hours. I had to drink massive quantities of Gatorade to recover.
I later joked with my co-workers about the "Wayne Handley Diet." I lost about 10 pounds of sweat in 15 minutes.
See you next time!
Mark Thompson is in engineering support at Prototron Circuits. To contact him, click here.
More Columns from The Bare (Board) Truth
The Bare (Board) Truth: My Top Six Design ChallengesThe Bare (Board) Truth: Via Basics
The Bare (Board) Truth: 5 Questions About Improving Thermal Management
The Bare (Board) Truth: Teaching the Next Generation—An Overview of Today’s University Courses
The Bare (Board) Truth: Fabrication Starts With Solid Design Practices
Board Negotiations: Design Rules and Tolerances
The Bare (Board) Truth: Eliminate Confusion
The Bare (Board) Truth: Getting on the Same Page—A Data Story