-
- News
- Books
Featured Books
- design007 Magazine
Latest Issues
Current IssueProper Floor Planning
Floor planning decisions can make or break performance, manufacturability, and timelines. This month’s contributors weigh in with their best practices for proper floor planning and specific strategies to get it right.
Showing Some Constraint
A strong design constraint strategy carefully balances a wide range of electrical and manufacturing trade-offs. This month, we explore the key requirements, common challenges, and best practices behind building an effective constraint strategy.
All About That Route
Most designers favor manual routing, but today's interactive autorouters may be changing designers' minds by allowing users more direct control. In this issue, our expert contributors discuss a variety of manual and autorouting strategies.
- Articles
- Columns
- Links
- Media kit
||| MENU - design007 Magazine
Estimated reading time: 3 minutes
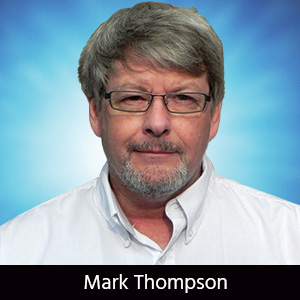
RoHS for Fabricators and Designers: Fact and Fiction
Most of you have heard of the European Union's RoHS directive. Some people mistakenly think it's mainly an assembly problem. But how, exactly, does RoHS pertain to PCB fabricators and designers?
Often called the "lead-free" directive, the Restriction of Hazardous Substances actually restricts the use of six substances. They are:
1. Lead (Pb);2. Mercury (Hg);3. Cadmium (Cd);4. Hexavalent Chromium (Cr6+);5. Polybrominated Biphenyls (PBB); and6. Polybrominated Diphenyl Ether (PBDE).
PBB and PBDE are flame retardants used in plastics. Many of these were used in the woven epoxy glass used traditionally in the fabrication of circuit boards. Many of the older compositions such as FR-4 types contained either PBB or PBDE. So this "lead-free" directive restricts not only the use of lead or tin/lead for the surface finish of a given PCB but also the use of certain flame retardants in the materials themselves.
New material types created without these flame retardants can survive the greater temperature excursions necessitated by the elevated temps associated with alternative surface finishes such as ENIG (electroless nickel immersion gold) or immersion silver. However, as always, you must know your parts application. There are materials suited for these elevated temps, ranging from 170Tg Td>330c to 180Tg >340C to 220Tg, etc.
Well, which material do you use?
If the standard high-temp FR-406 types of the world do not contain PBB or PBDE and most fabricators have this material readily available, will FR-406 suffice for RoHS compliance?
Yes and no. If materials used in PCB fabrication do not contain any of the restricted substances and are using alternative surface finishes instead of tin/lead and do not require multiple assembly passes or excessive rework simulation, then yes, a standard FR-406 type material will certainly meet RoHS requirements and be RoHS-compliant.
But if the application of the device itself requires multiple assembly passes or multiple rework simulations, then certainly a higher temp material such as Iteq IT-180 or Nelco N-4000-29 or Poly P370 is better suited. These are also generally available at most fabricators.
As with most materials, slight variations of effective Dk, loss tangent and dielectric pressed values mean you should consult your fabricator early in the parts evolution to ensure you have designed for 10%. By this I mean you will have factored in an allowable 10% deviation so that the part can be made by multiple fabricators on a variety of similar materials.
Impedance Issues?
Let's also not forget about what these small Dk variations and press values can do to your impedances.
Generally these slight Dk variations in high-temp e-glass style materials only manifest themselves as a +/- .001" trace deviation, but even then, when the design is .004/.004, there is just no room for line/space adjustments. Ultimately, the fabricators' first order of business is to look at dielectric thickness alternatives before resizing any lines.
The online CAD bundled impedance software tools are a good start. But if you really want to get closer, have your fabricator run the numbers on their software using their known (based on empirical data) effective Dk numbers and press values (for establishing dielectrics necessary to meet impedances).
More and more work is going through contract manufacturers these days, so it is critical that the CEMs know what allowable material types can be used at the fab level. Some of you are thinking: Which IPC-4101 numbers denote materials that meet RoHS requirements?
Good question. There are materials that meet RoHS restrictions in the following catagories: 4101/26, /28, /121, /124, and 4101/129 all meet the RoHS directive. But again, not ALL of these can be used for every application.
Again, the 4101/26 and 4101/28 type high-temp FR-406 may not contain any of the restricted substances, but they may still not be well-suited for multiple assembly cycles and extra rework simulation. But they could be perfectly acceptable for parts that do not see excessive heat and merely need to be RoHS-compliant.
The Bottom Line
Remember, RoHS-compliant is different than RoHS-compatible. Many materials and surface finishes are compliant, but based on your parts application they may not be compatible. Communication is key; consult your fabricator and assembler for details about materials best suited for your application. Once again, thank you for your time. Feel free to contact me with any questions. See you next time!Mark Thompson is in engineering support at Prototron Circuits. To contact Mark, click here.
More Columns from The Bare (Board) Truth
The Bare (Board) Truth: My Top Six Design ChallengesThe Bare (Board) Truth: Via Basics
The Bare (Board) Truth: 5 Questions About Improving Thermal Management
The Bare (Board) Truth: Teaching the Next Generation—An Overview of Today’s University Courses
The Bare (Board) Truth: Fabrication Starts With Solid Design Practices
Board Negotiations: Design Rules and Tolerances
The Bare (Board) Truth: Eliminate Confusion
The Bare (Board) Truth: Getting on the Same Page—A Data Story