-
- News
- Books
Featured Books
- design007 Magazine
Latest Issues
Current IssueProper Floor Planning
Floor planning decisions can make or break performance, manufacturability, and timelines. This month’s contributors weigh in with their best practices for proper floor planning and specific strategies to get it right.
Showing Some Constraint
A strong design constraint strategy carefully balances a wide range of electrical and manufacturing trade-offs. This month, we explore the key requirements, common challenges, and best practices behind building an effective constraint strategy.
All About That Route
Most designers favor manual routing, but today's interactive autorouters may be changing designers' minds by allowing users more direct control. In this issue, our expert contributors discuss a variety of manual and autorouting strategies.
- Articles
- Columns
- Links
- Media kit
||| MENU - design007 Magazine
Estimated reading time: 3 minutes
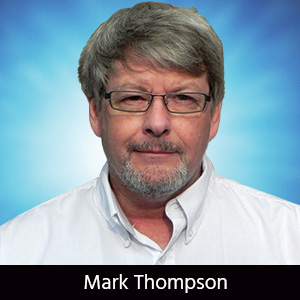
The Bare (Board) Truth: Scene and Heard at IPC APEX EXPO
I was in Las Vegas for the annual IPC APEX EXPO 2011 show. Yeah, I know. It must be rough having to work in Vegas, but somebody’s got to do it.
I’m always amazed at the diversity of people I see while people-watching in Vegas. And this year, we saw a great diversity of new products and processes at APEX. Some of these processes, as Semblant CEO Steven Lowder pointed out, were new combinations of older technologies, while others addressed problems in a completely new, different way.
So let’s start with Semblant. Semblant has teamed up with Nordson March to create a real game-changing polymerized plasma surface finish. This is quite an impressive technology. This particular plasma surface is deposited using a plasma polymerization process in a vacuum chamber. It can lay down a continuous coating down to 15 nanometers, and it is highly solderable. I know what you’re thinking, A polymer that you can solder to? Yes, not only can you solder to it but it generates NO hazardous wastes and uses NO greenhouse gasses.
I also found some older technologies being used in a completely new way, such as Orbotech’s AOR (automated optical repair) station. With the AOR, any shorts are first located by the AOI, and the lasers on the AOR then ablate the copper shorts quickly and reliably, and far more accurately than any human being with an X-acto knife.
This fascinated me quite a bit, and I began to wonder: How fast they can make these things? Can we at some point in our future get down to very small trace and space geometries in a fraction of the time without the use of any chemistry per se?
Speaking of imaging, Maskless Lithography also showed off a fantastic new product for direct digital imaging. I say direct DIGITAL imaging as it utilizes gray level imaging (GLI) technology to provide high-speed and extremely accurate features. (It is the gray level control of exposed image pixels that allows for fine edge control.)
In addition, one of the biggest advantages of digital lithography is that the image pattern can be scaled or dimensionally altered minutes before the pattern is projected onto the substrate, allowing for on-the-fly scaling due to inner layer misregistration through lamination. Imaging systems have certainly come a long way. I’ve been familiar with direct imaging systems at Prototron for a number of years. I know that I will be looking into both Semblant’s new surface finish and Maskless Lithography’s gray level imaging technology.
Another amazing device I saw at APEX this year was made by Orbotech: The Sprint inkjet system. Although there are a number of manufacturers of good inkjet legend printers, I was surprised at the speed and legibility of these very small designators. In years past, characters had strokes on the order of 6-7 mils, a width of 40 mils and height of 60 mils. Today, with board geometries at a premium, the character sizes are down to 3-4 mil stroke sizes, 20 mil widths and 40 mil character heights. And the Sprint uses very little ink and wastes virtually none. The panel I saw was printed and UV-cured to the touch in about 30 seconds.
But all this new technology was only a small part of this year’s APEX success story. Many of the technical sessions at APEX and the Designers Forum were full, with attendees showing a renewed interest in understanding our technology and our industry overall. Great presenters covered everything from design and manufacturing tricks and techniques to practical concerns such as the benefits of technology vs. cost.
Next year, IPC APEX EXPO will be held in San Diego. This year, the show recorded an 8% increase in attendance over the previous year, so I expect to see an even larger show next year, thanks to its proximity to El Segundo and all the military and commercial interests.
I hope to see you all at IPC APEX EXPO next year!
Mark Thompson is in engineering support at Prototron Circuits. To contact Mark, click here.
More Columns from The Bare (Board) Truth
The Bare (Board) Truth: My Top Six Design ChallengesThe Bare (Board) Truth: Via Basics
The Bare (Board) Truth: 5 Questions About Improving Thermal Management
The Bare (Board) Truth: Teaching the Next Generation—An Overview of Today’s University Courses
The Bare (Board) Truth: Fabrication Starts With Solid Design Practices
Board Negotiations: Design Rules and Tolerances
The Bare (Board) Truth: Eliminate Confusion
The Bare (Board) Truth: Getting on the Same Page—A Data Story