-
- News
- Books
Featured Books
- design007 Magazine
Latest Issues
Current IssueProper Floor Planning
Floor planning decisions can make or break performance, manufacturability, and timelines. This month’s contributors weigh in with their best practices for proper floor planning and specific strategies to get it right.
Showing Some Constraint
A strong design constraint strategy carefully balances a wide range of electrical and manufacturing trade-offs. This month, we explore the key requirements, common challenges, and best practices behind building an effective constraint strategy.
All About That Route
Most designers favor manual routing, but today's interactive autorouters may be changing designers' minds by allowing users more direct control. In this issue, our expert contributors discuss a variety of manual and autorouting strategies.
- Articles
- Columns
- Links
- Media kit
||| MENU - design007 Magazine
Estimated reading time: 5 minutes
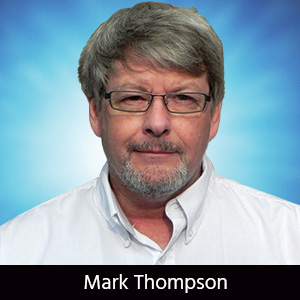
The Bare (Board) Truth: Four Common Fabrication Questions
Greetings all. Earlier this year, I covered the 10 Most Common Fab Misconceptions. In this column, I will take a similar approach and address some of the most common fabrication questions that I hear. These same questions keep popping up, over and over, so these topics are obviously frustrating to many of you.
I believe I can dispel the myths surrounding these challenges, and explain their solutions.
Common Question No. 1: Can you do 4 oz., 5 oz. or even 6 oz. finished boards?
Answer: Yes, most fabricators can build 4 oz., 5 oz. or even 6 oz. finished parts, but there are certain constraints to consider when talking about high copper inners and outers. This is a multipart answer:
A. Air gap or space considerations for high copper. Once again, the trace width is of a lesser concern unless the trace width is at or less than the total copper thickness, at which point it becomes an aspect ratio issue all its own.
Typically, fabricators perform an etch compensation based on the STARTING copper weight. As inner layers are normally processed as what is called “print and etch,” the starting and finished copper are one and the same, so for a 4 oz. inner layer there would be a .004” etch compensation. This is why on high copper jobs, space is more of a consideration than traces, because you must now have enough space to accommodate this etch compensation and still have adequate space left over AFTER the etch compensation.
Our customers ask, “Can you start on a lower copper weight and plate up to avoid the large etch compensations?” The answer is yes, but there is potential peril in doing so. Plating can result in sharp edges that can slice through layers of pre-preg, resulting in high-resistance shorting. This is especially true when dealing with coil boards, where layers feature metal coils on top of each other throughout the stack-up.
B. Inner layer considerations for high copper weights: What are the layer configurations? Mostly planes? Mostly signals? Mixed? Coil boards?
All of these configurations play into determining how much pre-preg will “nest” between layers internally, as well as how much pre-preg will be lost in the anti-metal channels and voids on the layers themselves. If the layer configuration is mostly planes, less pre-preg is generally nested between layers, but with a minimum dielectric distance of the total combined copper weight of the inner layer interface and a minimum of an additional .004” (to meet any Class 3 IPC-6013 minimum dielectric concerns.)
If it’s mixed or signal layers, more pre-preg will flow into the porous areas, resulting in less dielectric material between the copper lands between layers.
C. Panelization considerations for high copper weights: This too must be considered. If the part is small enough to fit multiple images on a given sub-panel or panel, the clearance between parts creates another trough that fills with pre-preg, potentially reducing the dielectric between layers even further.
Common Question No. 2: What size should I make my pads and anti-pads for inner planes?
Answer: This depends on the board complexity, layer count vs. overall dielectric, and other factors. The typical minimum pad size is approximately .010” over your intended finished hole size (FHS). The fabricator will drill approximately .004 - .005” over the FHS to plate back down to that intended finished size. In addition, a fabricator normally likes to see a minimum of a .002 - .0025” per side annular ring AFTER dill compensation, hence the .010” over the FHS.
However, it should be noted this is a minimum annular ring requirement and most fabricators would like to see more than .002” -.005” per side after drill compensation. In addition, if the part is very large and has many holes, there is a high potential for pad breakout with this minimum annular ring, because most drill/fab machine tolerances are +/-.003”.
This is also why the minimum anti-pad size for an anti-pad on a plane layer is larger than that of signal layers. Here you will want to go a minimum of .015 - .020” over the FHS, this will result in .005 MINIMUM per side of clearance (plated hole to copper pour) AFTER drill compensation. Again. this is a bare minimum. Normally fabricators would like to see .007” per side clearance from the edge of the drill-compensated plated hole to the adjacent copper pour.
Common Question No. 3: I have some via-in-pad structures, Do I have to plug these with epoxy or metal/epoxy?
Answer: This also depends on the nature of the design. For instance, if the surface mount pad that the via resides in is small and there are clearances on the solder mask artwork on one or both sides, your fabricator may insist on either an epoxy or metal/epoxy type via fill. This way the clearance on one or both sides is of little consequence after via fill / planarization and over-plate.
If, however, there are not clearances on both sides or there are clearances on one side only, and the land the via resides upon is fairly large, the via can be plugged with solder mask from the side with no clearances and save some cost. And on an .062” thick part, the mask generally does not bleed through onto the opposite side where the surface mount clearance resides.
And finally...
Common Question No. 4: What is the smallest hole size I can use for an .062” thick layer of X material?
Answer: This where the aspect ratio come into play. Typically, most fabricators do not like to exceed a 10:1 DRILL aspect ratio. I say drill aspect ratio because the 10:1 figure applies to the drilled hole size, NOT the FHS.
Remember, fabricators will typically drill anywhere between .004 - .005” over the FHS to plate back down to the intended size. So a .005” finished via specified as +/-.003” would be drilled at .009 - .010” and not exceed a 10:1 drill aspect ratio. However a .005” via specified as +.000 - .005” would have to be drilled at no larger than .006”, which would be right at the 10:1 drill aspect ratio. Got that?
Again, these are just a few of the more common questions we’re asked all the time. I thought it might be helpful to reiterate some of them and their answers…
As always, I appreciate your time. If you have any questions, common or otherwise, feel free to contact me any time.
See you next time!
Mark Thompson is in engineering support at Prototron Circuits. To contact Mark, click here, or call 425-823-7000.
More Columns from The Bare (Board) Truth
The Bare (Board) Truth: My Top Six Design ChallengesThe Bare (Board) Truth: Via Basics
The Bare (Board) Truth: 5 Questions About Improving Thermal Management
The Bare (Board) Truth: Teaching the Next Generation—An Overview of Today’s University Courses
The Bare (Board) Truth: Fabrication Starts With Solid Design Practices
Board Negotiations: Design Rules and Tolerances
The Bare (Board) Truth: Eliminate Confusion
The Bare (Board) Truth: Getting on the Same Page—A Data Story