-
- News
- Books
Featured Books
- design007 Magazine
Latest Issues
Current IssueProper Floor Planning
Floor planning decisions can make or break performance, manufacturability, and timelines. This month’s contributors weigh in with their best practices for proper floor planning and specific strategies to get it right.
Showing Some Constraint
A strong design constraint strategy carefully balances a wide range of electrical and manufacturing trade-offs. This month, we explore the key requirements, common challenges, and best practices behind building an effective constraint strategy.
All About That Route
Most designers favor manual routing, but today's interactive autorouters may be changing designers' minds by allowing users more direct control. In this issue, our expert contributors discuss a variety of manual and autorouting strategies.
- Articles
- Columns
- Links
- Media kit
||| MENU - design007 Magazine
Estimated reading time: 4 minutes
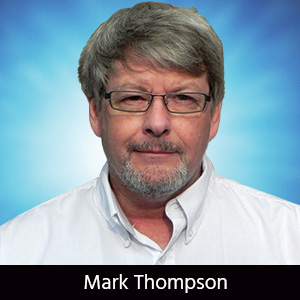
The Bare (Board) Truth: Slow Down and do it Right
Seems like lately we have been seeing a fair amount of new work from new customers, and one thing seems pervasive. Part of the reason we are doing a lot of this new work is time. Engineers, designers and layout folks are being pressed for time; no longer can they wait for two to four weeks of lead time.
As a fast-turn prototype manufacturer, we’re equipped to help with this time crunch. As you might expect, this time crunch results in more design mistakes and conflicts arriving in our shop. (I myself am guilty of feeling harried recently, and I too have made mistakes in an effort to get everything done yesterday.)
Some of the new designs I’ve encountered are fairly complex, with geometries going right down to process minimums, leaving little or no room for compromises. So let’s talk about the risks associated with assuming your board house will find (and be able to) correct errors in your designs.
First off, let’s be clear about what most fabricators can and cannot do for you regarding electrical functionality issues.
For most fabricators, the only way of checking the electrical design without having an electrical engineer on hand is with a netlist comparison. The design iteration (via the provided IPC D-356 netlist) is checked against the customer-provided output Gerber data. If something is inherently wrong with the electrical portion of the design but meets all manufacturing criteria such as minimum space for desired copper weight, etc., it most likely will not be caught by a board house unless a netlist can be provided.
For instance, if you have inadvertently poured copper over an area on a plane at the layout stage where there should be reliefs and shorted the planes together, without an IPC netlist, the board house will not necessarily find the error.
Remembering that most fabricators do not want to change your design; in fact we typically want to change as little as possible on your designs, and we only modify anything due to manufacturing concerns.
Functionality means something different to a board house than it does to the customer.
For most board houses that do not have an EE on staff, functionality merely means the board meets all of our manufacturing criteria such as pad size, minimum space for desired copper weight, etc. This functionality does not necessarily rule out any electrical issues.
Trying to rush things through to fabrication many times results in a new revision. Things like differential pairs that do not have matched length or consistent space between traces in the pairs. Often engineers come along and ask for slight tweaks for issues such as EMI, and these tweaks can impact the impedances. These tweaks include adding copper pour in an effort to deal with EMI and unintentionally creating co-planar coupling, or taking away metal being used as a ref plane for heat considerations.
Some of our customers neglect to update any “boiler” notes on drawings that may conflict or create additional questions. You may, for instance, want to change the soldermask color this rev, and so you have indicated your new color choice to a salesperson at the fab shop upon RFQ. At this point, if a conflict exists, the salesperson needs to clarify and update the drawing to match the current color.
If this is not done, more time can be lost going back and forth inside your own facility!
In conjunction with this, we are seeing a new wave of engineers, designers and layout folks going through trials and tribulations, many of them making the same mistakes that others have made before them. And for the same reasons.
Let me give you another example. Let’s say you are providing an IPC D-356 netlist for the first time and the fab house contacts you with 14 broken or open nets; they all happen to be associated with non-plated holes that have large surface pads designed to make a surface connection via the mounting screw head. This is very common. Here, the design IPC netlist assumed a connection that is simply not present on the Gerber.
Similarly, if you have plated half holes at the part edge for “castellations” you may also get a phone call from your fabricator with a netlist mismatch labeling those locations broken or open nets. Again, this may be due to mounting screws or plates that are assumed to make the connection on the design netlist, even though this is not evident on the Gerber data.
The bottom line is this: It’s always best to slow down and do it right. As the old saying goes, if you don’t have time to do it right the first time, how will you find time to go back to correct your mistakes?
Cutting corners to save time does not save anything if a new revision is necessary to deal with issues – issues not considered at layout or drawing generation – that come up at fabrication. Take the time to recheck the design and output Gerbers to make sure you don’t lose further time by having something go on hold at your fabricator.
As always I really appreciate your time. If you have any comments, questions or concerns, please contact me. Thanks!
Mark Thompson is in engineering support at Prototron Circuits. To contact Mark, click here, or call 425-823-7000.
More Columns from The Bare (Board) Truth
The Bare (Board) Truth: My Top Six Design ChallengesThe Bare (Board) Truth: Via Basics
The Bare (Board) Truth: 5 Questions About Improving Thermal Management
The Bare (Board) Truth: Teaching the Next Generation—An Overview of Today’s University Courses
The Bare (Board) Truth: Fabrication Starts With Solid Design Practices
Board Negotiations: Design Rules and Tolerances
The Bare (Board) Truth: Eliminate Confusion
The Bare (Board) Truth: Getting on the Same Page—A Data Story