-
- News
- Books
Featured Books
- design007 Magazine
Latest Issues
Current IssueProper Floor Planning
Floor planning decisions can make or break performance, manufacturability, and timelines. This month’s contributors weigh in with their best practices for proper floor planning and specific strategies to get it right.
Showing Some Constraint
A strong design constraint strategy carefully balances a wide range of electrical and manufacturing trade-offs. This month, we explore the key requirements, common challenges, and best practices behind building an effective constraint strategy.
All About That Route
Most designers favor manual routing, but today's interactive autorouters may be changing designers' minds by allowing users more direct control. In this issue, our expert contributors discuss a variety of manual and autorouting strategies.
- Articles
- Columns
- Links
- Media kit
||| MENU - design007 Magazine
Estimated reading time: 5 minutes
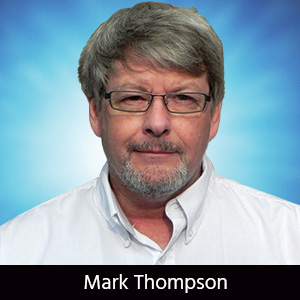
The Bare (Board) Truth: Tales From the Fab Shop
Greetings all! It has been a while since I have been able to write with any consistency. Fortunately, I’ve had plenty of time to gather fodder for new columns, thanks to the many good and bad habits of designers and engineers. Now I can relate some of these examples back to you in an effort to help you avoid making similar mistakes.
We all want to be able to make assumptions about certain aspects of processes in a typical fab shop, but the truth is that there really are no more “typical” fab shops in the US. The large production fab houses have expanded their capabilities, while the smaller yet still-alive fabricators carefully weigh the consequences of newer technologies or processes.
Gone are the days of doing ROIs on eight pieces of equipment, plugging them all in simultaneously and crossing your fingers that everything will work as planned. A good fabricator carefully researches the new equipment or process and makes sound, educated purchases based on customer needs.
The salesperson comes in at the beginning of this process. Customers frequently ask outside sales folks about remedies to common industrywide issues. These folks should be prepared to offer those solutions. They don’t always have to involve a new process or a large technology shift. Most of the time, once the need is fully understood there are many options to be able to fulfill that need.
I am a huge believer in common sense in electronics. If a product does not have to contend with temperature excursions, available board space driving parts smaller, and the geometries of smaller features as well, it will be a more robust product in general.
One thing often not considered when designing at smaller geometries: With the small features dictated by available board space, if you have impedances, the traditional 50 ohm and 60 ohm structures are very small. This is where tolerance plays a key role in whether or not your board will be a no bid. At .1mm (.0039”) there is little room for any process errors; just a half-mil deviation from trace width can result in a 5 ohm difference.
Sure, small lines and spaces can be dealt with better by starting on a lighter copper weight, but remember the analogy about digging a trench. If I dig a shallower trench, it will have to be wider to contain the same volume. The same is true for traces on a PCB; if you go lighter on the copper weight so you can impose less etch compensation, the traces get wider to accommodate the same impedance. In addition, the shallower trench now has different flow characteristics than the deeper, thinner version. Again, the same is true for the flow of current on a PCB trace. I cannot remember where I heard that analogy years ago, and it is a bit tongue-in-cheek, but you get the idea.
And another thing: Keep it real. When reviewing your drawing notes, make sure they actually pertain to the job! Sometimes when editing these drawing notes, new notes are added but old ones are not deleted. These notes, if in conflict, will mean a phone call from your fabricator.
The same goes for various specifications for impedances. Make sure the traces and spaces that you say are controlled actually exist and that no “rounding” has occurred. For example, the drawing may call out .0055” traces for 50 ohms +/-10% on layer X but when we look at layer X, no such trace widths exist. Again, this will mean a phone call from your fabricator.
These all seem like obvious points, but we still get parts missing basic information: no outline, no drawing, and no dimensioned hole or feature, leaving us without a way to place the NC drill file within the part.
We still see designers creating same-net spacing violations by relying too heavily on autorouters. For example, surface features that are connected elsewhere on an internal plane may have copper pour too close to other metal features. Electrically it does not matter whether these features bridge as, again, they are connected elsewhere, but gap violations still occur nonetheless. For most fabricators, any sliver thinner than .003” has the potential to flake off and redeposit somewhere else on the board, causing potential opens (in the case of an outer layer).
Same-net spacing violations are also common on terminations for differential pairs as well. Many times, in an effort to match lengths, one of the traces will “wrap” around the terminating via. And because it is ready to be connected to said via, many times an autorouter creates same-net spacing violations. Fabricators going through “filling” slivers could easily (if they’re not careful) change the length of one half of the diff pairs!
Lastly, a word about when to involve fabricators in your quest for the desired impedances. I have said in the past that you should involve your fabricator at the earliest possible point in the parts evolution. But I have also said that a good sample plan from two, three or even four different fab shops can give you a good idea of the differences in material Dks and pressed values from the same 4101 family of materials.
I want to reiterate, however, that it is NOT a good idea to have your fabricator dictate the trace/space values unless the relationship is such that the end-user will always be using that same fabricator. The differences in Dk, press parameters and environmental conditions alone can be greater than +/-10% at geometries below .1mm.
This is a case when the engineer and the draftsman need to provide the fabricator information within 10% of the intended impedance. How do they go about doing this?
Again, start with a good idea of what the various Dks are for your chosen material based on frequency. Use an impedance calculator to establish the traces and spaces, and if co-planar coupled, the g-sep (copper pour distance to adjacent features).
A simple calculator tied to various CAD systems should be adequate to get within 10%. This way, once the design is handed off to your fabricator, you can be assured he will not come back with large “tweaks” to get to your desired impedance.
As always, please feel free to e-mail or call with your comments or suggestions.
Mark Thompson is in engineering support at Prototron Circuits. To contact Mark, click here, or call 425-823-7000.
More Columns from The Bare (Board) Truth
The Bare (Board) Truth: My Top Six Design ChallengesThe Bare (Board) Truth: Via Basics
The Bare (Board) Truth: 5 Questions About Improving Thermal Management
The Bare (Board) Truth: Teaching the Next Generation—An Overview of Today’s University Courses
The Bare (Board) Truth: Fabrication Starts With Solid Design Practices
Board Negotiations: Design Rules and Tolerances
The Bare (Board) Truth: Eliminate Confusion
The Bare (Board) Truth: Getting on the Same Page—A Data Story