-
- News
- Books
Featured Books
- design007 Magazine
Latest Issues
Current IssueProper Floor Planning
Floor planning decisions can make or break performance, manufacturability, and timelines. This month’s contributors weigh in with their best practices for proper floor planning and specific strategies to get it right.
Showing Some Constraint
A strong design constraint strategy carefully balances a wide range of electrical and manufacturing trade-offs. This month, we explore the key requirements, common challenges, and best practices behind building an effective constraint strategy.
All About That Route
Most designers favor manual routing, but today's interactive autorouters may be changing designers' minds by allowing users more direct control. In this issue, our expert contributors discuss a variety of manual and autorouting strategies.
- Articles
- Columns
- Links
- Media kit
||| MENU - design007 Magazine
Estimated reading time: 5 minutes
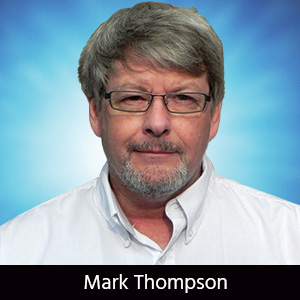
The Bare (Board) Truth: Tips for Getting the Boards You Need
This column is once again about understanding the customers’ needs. Some customers’ requirements are as simple as a specific definition for a fiducial size, rail tooling, or orientation feature, while other customers can require special processes.
Today, I will offer a few fabricator tips that can help designers get the boards they need, and not necessarily what they think they want. The last time I wrote about this topic, I got a good deal of feedback from our customers.
1. If you cannot provide image files such as Gerber or ODB++ with your quote and the part is impedance-controlled, many fabricators will send you an impedance checklist. This should include the very basics: Which traces are being controlled? On what layers do they reside? What is the threshold and tolerance associated with them?
Also, if we cannot see Gerber or ODB++ at the quote stage, we may ask, “What color and type will the mask be?” and “Will there be any coplanar coupling going on?” Believe it or not, at the smaller trace geometries, the color of solder mask can affect the impedance modeling. Any color other than the standard green masks are about half a mil thicker, and with traces and spaces less than .1mm, this can affect the impedance. Additionally, if we calculate all traces in “free space” because we have no image files to review (assuming no coplanar coupling) and the job comes in closely coupled, again the calculations/model will need to be redone.
2. We fabricators are a very literal group. If your drawing specifies the trace sizes that are impedance-controlled, make sure there are no rounding errors if converting from metric to Imperial, or from one output format to another. If you specify .0052” traces on X layers to be 50 ohms +/-10%, but there are no .0052” traces, you can expect a phone call from your fabricator. Remember, we will build it the way you tell us to build it.
3. Be sure you specify electrical connections that are feasible for your fabricator. For example, let’s say you have thermal ties on an inner plane layer, all inside a “fenced” or isolated area, and some are oriented in such a way that the hole with thermal ties is NOT escaping to the adjacent isolated plane because of the orientation of the spoke ties. The hole, however, is connected on another layer at the same spot or by association. Not everyone can build this type of construction.
4. Quotes from a fabricator based solely on preliminary drawings should be considered preliminary quotes, subject to change upon receipt of the final artwork files, drawing and drill files. Many times a customer will not include vias in the prelim data, and since vias can be 1/3 or more of the total hole count on any given job, they could easily affect the quote accuracy. Other items not on prelim drawings may include requirements for via fill or surface finish encapsulation, or even controlled impedances. Your chosen fabricator should be looking at the final data and drawings carefully.
5. Beware material deviations. Most folks state on their drawings to use a specific type of material or equivalent based on the IPC-4101 number. This does NOT mean you can substitute any material the fab shop may have; it means you may use an EQUIVALENT. For instance, let’s says the drawing calls out P-370 or equivalent. In the 4101 family, the applicable options would be N-4000-29, IS-410 or IT-180 – all possess the survivability needed for the higher temps at assembly due to alternative surface finishes. G10 or standard FR-4 would NOT be an equivalent in this case.
6. Know your options when calling for 50 ohm SE surface structures vs. 75 ohm SE structures. Let’s says your desire is to have both 50 ohm and 75 ohm SE structures on surface layers. There are at least two ways to skin this cat. If, based on part geometries, you must keep the 50 ohm traces at .005” or less, you most likely will have to create a ref plane deeper down in the stack-up for the 75 ohm traces. However, if you can live with traces that are .009” to .010” wide for your 50 ohm structures, you can have the 75 ohm traces reference the same plane as the 50s and still stay around .004”.
7. Fabricating via-in-pad at prototype vs. production volumes: Many times, if the part is only being prototyped and the board will not go into the field, the customer may decide to forgo any epoxy or silver-filled vias in favor of a mask plug. In many ways, although it is assumed by the customer to be easier than silver or epoxy fill, the truth is that in the typical scenario with a via in the mount and no clearance present on the opposing side, there are some additional fabrication processes involved. One way of doing this is to create a barrel clearance only on the side currently being tented with mask on the artwork. This allows plating finishes such as immersion gold to flow freely through the vias, ensuring no oxidation. A secondary plugging process is then done from the side with no clearances. The result is good surface plating continuity and the side with no clearances is tented as the artwork shows and the customer desires.
As opposed to a “true” epoxy or silver fill, these vias, if epoxy or silver-filled, are plated over and planarized, making the absence of any clearances on the opposite side of the via-in-pad a non-issue. For this process, the vias to be filled are drilled and plated, and then sent to be epoxy-filled or silver-filled, planarized, and plated prior to the addition of the remainder of the plated through-holes and outer layer image. Since the vias now have continuity via the plating process and are fully plugged with either epoxy or silver/epoxy, the fact there is no clearance on one side of the mask vs. the other is of no consequence.
8. There is no substitute for a real IPC-D-356 netlist. Many fabricators have front-end systems that generate an IPC type netlist based on the Gerbers provided. Personally, I think at that point you are relying solely on the accuracy of the software. The truth is, if you wish to verify the design vs. the exported Gerbers, and your netlist is created from those same Gerber files, we will NEVER find a mismatch. As always, the best way to verify a design vs. exported Gerbers is to provide a true IPC-D-356 netlist for comparison.
Just a few things to think about before you send that dataset to a fabricator for a quote!
I certainly hope this has helped. As always, please feel free to contact me with any questions or feedback.
More Columns from The Bare (Board) Truth
The Bare (Board) Truth: My Top Six Design ChallengesThe Bare (Board) Truth: Via Basics
The Bare (Board) Truth: 5 Questions About Improving Thermal Management
The Bare (Board) Truth: Teaching the Next Generation—An Overview of Today’s University Courses
The Bare (Board) Truth: Fabrication Starts With Solid Design Practices
Board Negotiations: Design Rules and Tolerances
The Bare (Board) Truth: Eliminate Confusion
The Bare (Board) Truth: Getting on the Same Page—A Data Story