-
- News
- Books
Featured Books
- design007 Magazine
Latest Issues
Current IssueLearning to Speak ‘Fab’
Our expert contributors clear up many of the miscommunication problems between PCB designers and their fab and assembly stakeholders. As you will see, a little extra planning early in the design cycle can go a long way toward maintaining open lines of communication with the fab and assembly folks.
Training New Designers
Where will we find the next generation of PCB designers and design engineers? Once we locate them, how will we train and educate them? What will PCB designers of the future need to master to deal with tomorrow’s technology?
The Designer of the Future
Our expert contributors peer into their crystal balls and offer their thoughts on the designers and design engineers of tomorrow, and what their jobs will look like.
- Articles
- Columns
Search Console
- Links
- Media kit
||| MENU - design007 Magazine
Mark Thompson: What Designers Need to Know about Fab
June 8, 2018 | Dan Beaulieu, D.B. Management GroupEstimated reading time: 3 minutes
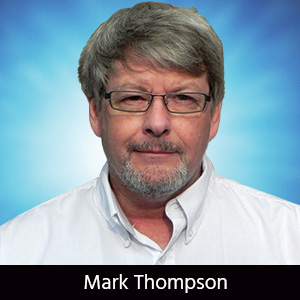
Mark Thompson wants to help PCB designers. He’s seen it all in CAM support at Prototron Circuits: the incomplete or inaccurate data packages, boards that are unnecessarily complex or over-constrained, and so much more. As technical customer liaison, Mark leads tours of Prototron’s facility in Redmond, Washington, often providing PCB designers and design engineers their first glimpse inside a board shop. Mark just returned to writing his popular Design007 Magazine column, The Bare (Board) Truth, which addresses questions such as, “What happens to your design at CAM?”
I’ve known Mark for years, and it’s always a pleasure get a chance to talk with him. In our interview, I asked Mark to explain why it’s so important for designers to communicate with their fabricators, and why they need to get out of the office and visit a board shop every now and then.
Dan Beaulieu: Good morning, Mark. Good to see you again. I have a few questions for you.
Mark Thompson: Fire away!
Beaulieu: So, why should PCB designers talk to board shops?
Thompson: Excellent question, straight to the point. The answer is, because designers need to understand fabrication needs, and we as fabricators need to know their needs. Since we primarily deal with prototypes here at Prototron, most of the parts we see are first-run prototypes, and we have the potential to find unforeseen errors that need to be aired out before production.
Board applications have changed so vastly over the years that it is difficult, if not impossible, for a fabricator to attempt to guess at a customer’s intentions. Nor should he try! That’s where a simple conversation between the board designer and the board fabricator can be invaluable. For example, a customer may ask me questions like these: “Mark, what is the smallest mechanical hole size you can do?” Or “What is the thinnest dielectric you can deal with?” Or, “What is the minimum solder mask clearance you need?”
All are perfect examples of questions that, depending on the customers’ intentions, and they can be answered in multiple ways. The first question, asking about minimum mechanical hole size, is usually followed by “What is the smallest signal pad associated with that hole size and what is the smallest anti-pad on a plane layer for that hole size?” This is where the fabricator should be asking more questions, such as, “Are you referring to vias when you ask about our smallest hole size?”
Because you can buy yourself back a lot of real estate for trace routing, smaller pad sizes and smaller anti-pad sizes by your tolerance callout. If you call them out as +/-.003” we must drill some .004-.005” mils larger than the nominal hole size to plate back down to the nominal. If all you want is electrical continuity and don’t really care how small a given via ends up, call it out as +.003” minus the entire hole size. This tells a fab shop that they can drill the hole smaller, which makes my answers about minimum pad and minimum anti-pad size more appealing. They can now be smaller.
The same holds true with the second question. I need more information on my part to adequately answer this question. Sure, I can tell you we can use .0025” core internally for capacitance and decoupling, but can we have .0025” pre-preg dielectric between 1 oz. clad cores? No! And that is where my conversation changes to copper aspect ratios and pre-preg nesting or loss due to the layer type. Is it full plane, where it may not lose a lot of dielectric distance, or a signal where it may lose some dielectric?
To read this entire interview, which appeared in the May 2018 issue of Design007 Magazine, click here.
Suggested Items
Real Time with... IPC APEX EXPO 2025: New Dispensing and Coating Solutions from Rehm
04/03/2025 | Real Time with...IPC APEX EXPOMichael Hanke, Global Sales Officer at Rehm, discusses new dispensing and coating equipment developed in Germany. He emphasizes the significance of software integration with customer systems to tackle market challenges.
BEST Inc. Presents StencilQuik for Simplifying BGA Rework Challenges
04/02/2025 | BEST Inc.BEST Inc., a leader in electronic component rework services, training, and rework tools is thrilled to announce StencilQuik™ rework stencils. This innovative product is specifically designed for placing Ball Grid Arrays (BGAs) or Chip Scale Packages (CSPs) during the rework process.
Real Time with... IPC APEX EXPO 2025: Nordson's Expansion of Intelligent Technologies
04/02/2025 | Real Time with...IPC APEX EXPOJonathia Ang-Mueller gives an update on Nordson's latest selective soldering system which features a small footprint, offering cost savings and increased production capacity. Advanced software allows for pre-sales simulations, enhancing customer engagement.
Knocking Down the Bone Pile: Basics of Component Lead Tinning
04/02/2025 | Nash Bell -- Column: Knocking Down the Bone PileThe component lead tinning process serves several critical functions, including removing gold plating, mitigation of tin whiskers, reconditioning of component solderability issues, and alloy conversion from lead-free (Pb-free) to tin-lead or from tin-lead to lead-free for RoHS compliance. We will cover each of these topics in more detail in upcoming columns.
Real Time with... IPC APEX EXPO 2025: Innovations at Indium Corporation—A Look into the Future
04/02/2025 | Real Time with...IPC APEX EXPOIndium Corporation, led by CEO Ross Berntson, is making strides in automotive applications with innovative solder paste technologies. The company prioritizes sustainability and energy efficiency in manufacturing while developing its workforce through partnerships with local universities.