-
- News
- Books
Featured Books
- smt007 Magazine
Latest Issues
Current IssueSupply Chain Strategies
A successful brand is built on strong customer relationships—anchored by a well-orchestrated supply chain at its core. This month, we look at how managing your supply chain directly influences customer perception.
What's Your Sweet Spot?
Are you in a niche that’s growing or shrinking? Is it time to reassess and refocus? We spotlight companies thriving by redefining or reinforcing their niche. What are their insights?
Moving Forward With Confidence
In this issue, we focus on sales and quoting, workforce training, new IPC leadership in the U.S. and Canada, the effects of tariffs, CFX standards, and much more—all designed to provide perspective as you move through the cloud bank of today's shifting economic market.
- Articles
- Columns
- Links
- Media kit
||| MENU - smt007 Magazine
Estimated reading time: 9 minutes
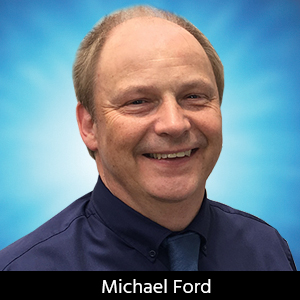
Contact Columnist Form
Smart for Smart’s Sake, Part 3: Unification & Traceability
All of the recent innovations in electronics manufacturing, including Industry 4.0, the Internet of Manufacturing, smart factories, digital manufacturing, etc., bring digitization to many aspects of the factory operation. The names don’t really matter, as most people’s understanding of what these initiatives are continues to differ. However, concerns with implementing these innovations include the compatibility of information transfer, as we discussed in Part 1 of this series, as well as actual Smart application examples as we saw in Part 2, and the need for an open platform of information, which is being enabled by such technologies as the open manufacturing language (OML).
Digital data capture presents another opportunity for innovation—the complete traceability of the operation. Now, at last, traceability for electronics is defined by a dedicated standard in IPC-1782, which is designed to bring the appropriate levels of traceability without any net cost to the operation, that is, in a smart way.
Traceability is like having a CCTV camera that watches the manufacturing operation and records everything that happens. If a defect is detected in any aspect of production, the recording can be played back as if in slow motion to identify exactly what happened. The camera can see many different things happening because it has a point of view that includes the whole factory operation. Total traceability is not driven from a single point of view, such as the data from an SMT machine. The advantage of complete traceability is the ability to gather big data, that is, data from all of the different aspects of manufacturing, in such a way that information can be analyzed to understand the interaction of the different processes, events, and actions that are happening in the factory.
For example, we can watch the SMT placement machine. Our camera can see the placement of components onto the PCB. While this happens, the SMT machine provides a data record of these placements as the machine follows the engineering information that it was given. However, the data output is founded on the association of feeder position that the material was taken from for each individual placed component on the PCB. The engineering data identifies each feeder position with a part number, so the data looks as though it is reporting part number against reference position on each PCB.
The assumption, however, is that the correct part number was set up at that feeder position. The material verification records need to be checked to make sure this is true. The setup verification may have been done by the machine software or by a third-party software. For complete traceability, we need to rewind our recording to see the actual events related to the verification.
First, we can see that a reel of material was loaded onto a feeder. Usually, verification is done using a barcode on both the feeder and the material being read to associate the two together. The material barcode should provide the part number, which is checked against the engineering information for the machine for the intended position used. Assuming this process is done correctly, then the machine can have the feeder loaded, which can be then a simple automated confirmation that the material has been loaded in the right place.
However, there can still be sources of doubt. The part number used for verification is either a generic “internal” part number, or it could be the material vendor’s part number. The latter case is difficult to manage because of the lack of standardization currently with labeling of materials from suppliers. The label format and content have to be “learned” by the verification software, which, if done “on the fly” at the time of material preparation, can lead to a significant risk of error. The barcode labels are notoriously unreliable, and conflicts between material vendors can happen.
The better approach is to label the material as it comes into the factory, or at least the SMT warehouse area, on a unique material basis. Where this is done, we can gain better traceability by rewinding our recording to see these events taking place. As material comes in, the vendor barcode is read, and a conversion is made to the generic internal part number. As is most often the case, materials of the same generic part number can come from two or more suppliers. The shape, size, orientation, and even the way in which the materials are packaged for use on the machine can be different.
Simply labeling the material with the internal part number would mean that these differences would not be noticed until the material was at the machine, if you were lucky. The verification process would not record any issue, but a different behavior of the machines, including an epidemic series of defects, can occur if the differences are not noticed. Instead, unique identification of materials can be used to maintain a record about not only the part number but also all other information about the material that may be significant to the operation, including the physical differences, vendor specific metrics, and things such as moisture sensitivity device (MSD) parameters. With a unique profile maintained for each material in this way, the verification process can be much more secure and reduce variation in the material replenishment process, with automated consistent selection of materials by supplier as replenishment materials are needed.
Simple verification software at the machine may not provide the higher level of checking required unless it can understand the full profile of each individual material. Therefore, the machine software needs to be closely linked to the material management software of the factory. The smart and lean material management functions in use at the factory level can then also make use of the machine data, providing mutual operational value.
The series of these processes is recorded by our traceability camera. A base level of traceability may be satisfied with just a check that the part number was correct. On the other hand, most reputable electronics manufacturers will need to have clear control of quality and responsibility, requiring a higher level of traceability that goes into the detail of the handoff between these different systems within the factory.
This simple example of the traceability of SMT materials illustrates that the whole solution cannot come solely from one point. Automatic collaboration needs to be done. Many other processes consume materials, including manual assembly and repair, as well as configuration using virtual materials such as MAC addresses. There are also consumable materials such as solder paste, which in itself has a complex working procedure to follow, with similar different levels of traceability data capture.
Traceability does not stop with simple materials, however. Quite often, subassemblies are used as part of the product assembly, which need to have their traceability data inherited from their production history. Our recording of assembly operations has to be linked with other recordings made at different times and in different places, but they need to be are completely compatible to create a complete record of the build of the finished product.
Traceability covers more than just materials though. The process history is also a key part of any build record. Smart factory systems continuously plan the factory operation, making decisions about the best product flow and the best machine configuration setups. The information associated with each work order of products, including process setup configurations also needs to be seen by our traceability camera. This link of planning information is critical because we need to ensure that all processes have been set up and executed in the right sequence in the correct conditions, and that the result of the process has been good.
Test processes especially provide a large amount of data about each product, as well as the simple pass or fail result. Products that do not pass a test must be routed to a repair station. These processes also need to interact directly with the traceability data to determine any possible cause that may have arisen from deviations that were recorded throughout the production cycle, as recorded by the traceability data. The defect, once found, triggers an assessment to be made as to whether corrective action needs to be taken in the process or whether previously completed production units need to be double-checked.
In this simple example of just a cross-section of the factory operation, we can see the need for the exchange of data from all aspects of production: direct, indirect, and transactional. Data collected directly from processes is only valid where qualified against the prior processes and transactions through which the materials, the PCB, and operations that the machine went through to get to that point in time. The importance of the machine data is that it allows our traceability camera to see the progress of the operation, establishing the timeline against which every other aspect can then be related, looking backward or even forward in the recording.
About IPC-1782
The IPC-1782[1] traceability standard for electronics is a comprehensive specification for the capture of both material and process data, with four defined levels of detail/specification for each. Understanding traceability requirements is essential for expectations to be fulfilled, especially if and when traceability data is needed to identify the causes of complex issues or to identify the exact scope of an issue. Having the specification clearly defined also means that only the necessary data is captured, reducing costs.
About OML
The OML[2] specification is designed to enable the interconnection of all machines and processes using a single language definition, including transactional activities on the shop floor. OML supports all forms of smart factory activity for use in any digital factory/Industry 4.0 solutions, as well as being a conduit for all levels of traceability data. Virtually every machine and process has just one point of data collection. OML allows the use of that data by many different Smart applications simultaneously.
Smart Traceability
The use of data flowing in an automated way from processes provides almost all of the required data for traceability, at any level. It is analogous to the video feed from our camera, with every aspect of the picture included. It means that the cost of traceability can actually become negative. Instead of having additional operations to gather, qualify, and catalog traceability data, the whole process can be automated in a way that is synergistic with the Smart factory operation. Having this “video” record of all the events, the full potential of traceability data can be realized, which brings opportunity of the highest level of active quality management, as well as full control over any issues that may occur. Bringing these elements of Smart technology together, whatever the priority or approach, the effective common Smart or Digital Factory platform brings all of the elements together for full traceability as defined by IPC-1782.
References
- IPC 1782 can be purchased by clicking here.
- The OML Community website is at www.omlcommunity.com.
More Columns from The Essential Pioneer's Survival Guide
If It's My Data, I Can Do What I Want, Right?The Essential Pioneer's Survival Guide: One Size Fits All?
Smart for Smart's Sake, Part 2: Material Management
The 'New Face' of Automotive Traceability
Industry 4.0: Who Benefits?
To Be Lean is to Be Human
Stop the SMT Conspiracy, Part 2: Abduction
The Future of SMT: Welcome to the 4th Dimension