-
- News
- Books
Featured Books
- design007 Magazine
Latest Issues
Current IssueProper Floor Planning
Floor planning decisions can make or break performance, manufacturability, and timelines. This month’s contributors weigh in with their best practices for proper floor planning and specific strategies to get it right.
Showing Some Constraint
A strong design constraint strategy carefully balances a wide range of electrical and manufacturing trade-offs. This month, we explore the key requirements, common challenges, and best practices behind building an effective constraint strategy.
All About That Route
Most designers favor manual routing, but today's interactive autorouters may be changing designers' minds by allowing users more direct control. In this issue, our expert contributors discuss a variety of manual and autorouting strategies.
- Articles
- Columns
- Links
- Media kit
||| MENU - design007 Magazine
Estimated reading time: 1 minute
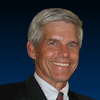
All About Flex: CAD for Flexible Circuits
To define and subsequently fabricate a flexible circuit, a set of electronic documents known as CAD files must be created. These files contain all the data needed for each software-controlled machine to perform its required process step. The type of data a circuit supplier receives from a customer can vary widely. In some cases, the files contain a complete set of data to manufacture a one-up part. In other cases the customer may only provide a print or net list and request the fabrication house to provide a quotation for the design layout by creating the data needed to define the part number. In most of these cases, a CAD file is created and sent to the customer for review and approval.
CAD engineers take a CAD file that defines a single part and panelize the data by creating a nested pattern repeated across the panel. Reverse nesting and off-angle part placement may optimize material utilization, which is a constant cost concern. But this optimization needs to be balanced by ease of stiffener placement and component assembly.
Part of the panelization process considers how to best apply manufacturing tolerance corrections such as artwork scaling as a compensation for material dimensional changes resulting from etching, copper plating and coverlay lamination. Material thickness, percent etched and material types all contribute to determining final dimensions. These interactions combine to make initial estimates more art than science. Refinements occur as empirical data is gathered on individual part numbers.
The CAD data is used to create all the electronic files needed for the programmable equipment that fabricates the part as well as the physical tooling.
To read this entire article, which appeared in the June 2017 issue of The PCB Design Magazine, click here.
More Columns from All About Flex
All About Flex: Terms and ConditionsAll About Flex: ISO 9001 Basics
All About Flex: FAQs on UL Listings for Flexible Circuits
All About Flex: Avoiding Trace Fracturing in a Flexible Circuit
Polyimide vs. Silicone for Flexible Heaters
All About Flex: Copper Thickness Requirements for Flex Circuits
All About Flex: Copper Grain Direction
All About Flex: Options for Purchasing Flexible Heaters