-
- News
- Books
Featured Books
- design007 Magazine
Latest Issues
Current IssueProper Floor Planning
Floor planning decisions can make or break performance, manufacturability, and timelines. This month’s contributors weigh in with their best practices for proper floor planning and specific strategies to get it right.
Showing Some Constraint
A strong design constraint strategy carefully balances a wide range of electrical and manufacturing trade-offs. This month, we explore the key requirements, common challenges, and best practices behind building an effective constraint strategy.
All About That Route
Most designers favor manual routing, but today's interactive autorouters may be changing designers' minds by allowing users more direct control. In this issue, our expert contributors discuss a variety of manual and autorouting strategies.
- Articles
- Columns
- Links
- Media kit
||| MENU - design007 Magazine
Estimated reading time: 5 minutes
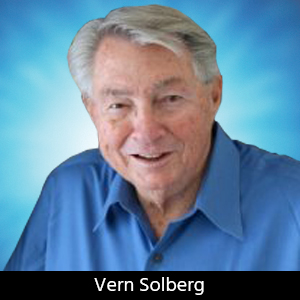
Embedding Components, Part 3: Implementing Discrete Passive Devices
Note: Part 1 of this column appeared in the June 2017 issue of The PCB Magazine and Part 2 appeared in the June 2017 issue of The PCB Design Magazine.
For many, the driving force to integrate passive components within the layers of the PCB structure was the need for providing the consumer with smaller and lighter products. Once the commercial sector began developing and refining embedded component processes and overcoming quality and reliability issues, the automotive, telecom, aeronautic, and aerospace industries recognized the advantages of embedded passives technology for the following benefits:
- Improved density and functionality
- Reduced PCB area and weight
- Increased assembly process efficiency
- Improved functional performance and reliability
Most of the passive components used in electronics are discrete surface mount components configured to mount onto land patterns furnished on the surface of a PC board. Designers have several choices for providing passive functions in a system design, such as discrete surface-mounted passives, array passives or passive networks, integrated (Rs and Cs) passive devices, and embedded discrete passive components. A growing number of PCB suppliers with experience in build-up of circuits can embed both passive and active components.
Although a majority of companies furnishing high-volume embedded component circuit boards are in Europe and Asia, there are number of proficient North American suppliers as well.
Providing formed resistors and capacitors within the circuit structure remains the most economical process with the least level of risk; however, value range and tolerance control is somewhat limited. Placing discrete component elements furnishes a greater value range and superior tolerances.
Embedded Component Process Planning
The process for embedding discrete passive component elements within the multilayer PCB structure is a sequential process requiring specialized SMT process skills and assembly systems typically outside the realm of the average circuit board supply chain—a process capability more common to OEMs and boardlevel assembly service providers. To prepare for efficient high-volume production, the PCB fabricator will need to establish in-house component placements and attachment capabilities and reliable component sources or develop partners for the procurement of components that are suitable for embedding. The PCB supplier must also determine which systems and methodologies will be required for applying termination materials (conductive polymer or solder) that can ensure precise component placements, curing polymers or reflowing solders, and specialized systems required for electrical testing during the progressive stages of the fabrication process.
When choosing discrete resistor, capacitor, and inductor components for embedding, both device outline and thickness must be considered.
While some passive components are very thin and require no special preparation, others may have profile dimensions requiring encroachment into contiguous circuit layers.
Discrete Resistors
Several companies are now able to furnish thin, small outline resistors and capacitors that prove to be ideal for embedded component applications. The outline of currently available components can be as small as 0.4 mm x 0.2 mm (01005) and 0.6 mm x 0.3 mm (0201).
Discrete thick-film resistors are offered in a 0.015-mm profile. Specifically developed for embedding, these devices are described as a flat thick-film resistor furnishing a value range of 1.0 ohm to ~10 M ohms with a power rating of 0.063 watts and working voltage maxing out at 50 volts.
Although these devices have a relatively low power rating, the operating temperature range, resistor value, and tolerance (1% and 5%) specified for the smaller devices are the same as the larger resistor variations and available with copper terminals. While tin-based alloy terminals are acceptable for solder or conductive polymer termination, copper terminals will be necessary when using plated microvia interface technology. For applications requiring resistor value tolerances less than 1%, an alternative nickel-chromium thin-film family is available, but the package dimensions are significantly greater than the thick-film resistor previously described.
Discrete Capacitors
Low-profile ceramic capacitors have been developed for height-restricted applications where device thickness is a key design constraint— perfect for embedded or other applications with thickness limitations. Ideal for decoupling and filtering applications, the components are available with the same small outline dimensions as the resistor family, but device thickness will vary somewhat due to the dielectric type and required volume.
For example, the body thickness for the 01005 capacitor is specified as 0.20 mm while the 0201 outline component thickness can increase to 0.30 mm. Additionally, the dielectric type and working voltage will impose limits on the capacitor value range for these smaller device outline families. The 01005 and 0201 type capacitors with a C0G dielectric are available in a value range of 5–100 pF. The X7R dielectric capacitors can furnish a value range of 68–470 pF for the 01005 capacitor and 68–10,000 pF for the 0201 variation. The standard terminal plating is tin-alloy over a nickel base metalization for solder and conductive polymer attachment. Because the base layer is a nickel-alloy, termination of the component to the circuit conductor pattern with copper-plated microvias may be possible.
Discrete Inductors
A limited value range of miniature inductors is available from several leading suppliers. The multilayer ceramic inductor family is available in both 0402 and 0603 (1.0 mm x 0.50 mm and 1.60 mm x 0.80 mm) outlines with a thickness equal to the device width (0.50 mm for the 0402 device and 0.80 mm for the 0603 variation). The terminal plating is a nickel alloy with a tin-alloy based coating for solder or conductive polymer interface.
The available inductance value ranges between 6.8 nH for the low and 220 nH for the high with a tolerance value of +/-5%. An alternative thin-film small outline and lowprofile inductor family is available too. For this variation, the inductor element is printed onto the surface of a ceramic base material, passivated and fired to protect the printed pattern, and furnished with a tin-alloy terminal for joining to the circuit structure. Small outline thin-film inductor elements will range in size from 0402 to 0603. The actual dimensions for the 0402 device are 1.0 mm x 0.50 mm x 0.35 mm, and 1.6 mm x 0.8 mm x 0.50 mm for the 0603 device.
The value range for these two thin-film inductor components is between 1.0 nH and 82 nH with a tolerance of +/-2%. Manufacturers claim that the miniature inductors furnish up to twice the rated current and half the DC resistance of comparable ferrite inductors. Designers should be aware that inductors size and value range varies somewhat between suppliers.
Next Column
Part 4 of this embedded component technology series will focus on land pattern development criteria, ways to accommodate higher profile passive components, and alternative termination methodologies.
Vern Solberg is an independent technical consultant specializing in surface mount technology, microelectronics design, and manufacturing technology.
This column originally appeared in the September 2018 issue the Design007 Magazine.
More Columns from Designer's Notebook
Designers Notebook: Basic PCB Planning Criteria—Establishing Design ConstraintsDesigners Notebook: Layer Stackup Planning for RF Circuit Boards
Designers Notebook: Addressing Future Challenges for Designers
Designers Notebook: Impact of Advanced Semiconductor Packaging on PCB Stackup
Designers Notebook: Implementing HDI and UHDI Circuit Board Technology
Designer's Notebook: Heterogeneous Integration and High-density SiP Technologies
Designers Notebook: PCB Design and IPC-CFX for Assembly Automation
Designer’s Notebook: What Designers Need to Know About Manufacturing, Part 2