-
- News
- Books
Featured Books
- design007 Magazine
Latest Issues
Current IssueProper Floor Planning
Floor planning decisions can make or break performance, manufacturability, and timelines. This month’s contributors weigh in with their best practices for proper floor planning and specific strategies to get it right.
Showing Some Constraint
A strong design constraint strategy carefully balances a wide range of electrical and manufacturing trade-offs. This month, we explore the key requirements, common challenges, and best practices behind building an effective constraint strategy.
All About That Route
Most designers favor manual routing, but today's interactive autorouters may be changing designers' minds by allowing users more direct control. In this issue, our expert contributors discuss a variety of manual and autorouting strategies.
- Articles
- Columns
- Links
- Media kit
||| MENU - design007 Magazine
Estimated reading time: 1 minute
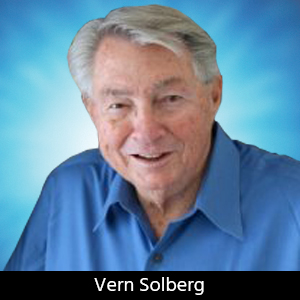
Embedding Components, Part 4: Passive Component Selection and Land Pattern Development
This column will focus on land pattern development criteria, and methodology for accommodating low and moderately high-profile passive components within a multilayer circuit board.
As noted in Part 3 of this series, a broad range of discrete passive component elements are candidates for embedding, but the decision to embed these component elements within the multilayer circuit structure must be made early in the design process. While many of these components are easy candidates for integrating into the substrate, others may not be suitable, or they are difficult to rationalize because they involve more complex process methodology.
Substrate Development
Basic material sets selected for this embedded component application defines a 200-μm FR-4 epoxy-glass core base with 18-μm copper foil bonded to both sides. In this example, the buildup material includes pre-impregnated layers of glass cloth with an uncured epoxy resin furnished pre-dried, but not hardened, and layers of 18-μm copper foil. There are more than a dozen thickness options available for prepreg materials, but for this process description, a 200-μm material will be referenced. The prepreg layer and copper foils are sequentially bonded together using a combination of pressure and heat. The process begins with imaging and chemically etching the circuit pattern on the copper foil. The lamination, imaging, and etching processes continue until the layer structure is complete.
When embedding components in the multilayer structure, several factors must be considered:
- Circuit layer selected for attachment
- Component size (length, width, and height)
- Terminal area and metalization
- Location and orientation
- Method for termination
While thin passive components may not require any preparation before lamination, taller components will likely need developing a cavity-like pocket in the dielectric layer to ensure that the overall flatness of the finished multilayer PCB can be maintained. Regarding the attachment method for components, tin-alloy plated terminals will be most compatible with a tin-based solder alloy or a conductive polymer material that is either deposited or stencil printed onto the mounting site.
To read this entire column, which appeared in the October 2018 issue of Design007 Magazine, click here.
More Columns from Designer's Notebook
Designers Notebook: Basic PCB Planning Criteria—Establishing Design ConstraintsDesigners Notebook: Layer Stackup Planning for RF Circuit Boards
Designers Notebook: Addressing Future Challenges for Designers
Designers Notebook: Impact of Advanced Semiconductor Packaging on PCB Stackup
Designers Notebook: Implementing HDI and UHDI Circuit Board Technology
Designer's Notebook: Heterogeneous Integration and High-density SiP Technologies
Designers Notebook: PCB Design and IPC-CFX for Assembly Automation
Designer’s Notebook: What Designers Need to Know About Manufacturing, Part 2