-
- News
- Books
Featured Books
- design007 Magazine
Latest Issues
Current IssueProper Floor Planning
Floor planning decisions can make or break performance, manufacturability, and timelines. This month’s contributors weigh in with their best practices for proper floor planning and specific strategies to get it right.
Showing Some Constraint
A strong design constraint strategy carefully balances a wide range of electrical and manufacturing trade-offs. This month, we explore the key requirements, common challenges, and best practices behind building an effective constraint strategy.
All About That Route
Most designers favor manual routing, but today's interactive autorouters may be changing designers' minds by allowing users more direct control. In this issue, our expert contributors discuss a variety of manual and autorouting strategies.
- Articles
- Columns
- Links
- Media kit
||| MENU - design007 Magazine
Estimated reading time: 1 minute
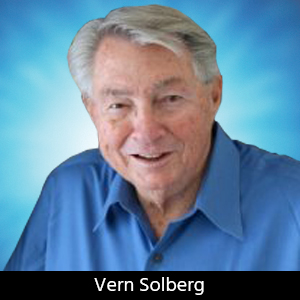
Designers Notebook: Design Challenges for Developing High-density 2.5D Interposers, Part 2
Author’s Note: Read Part 1 here.
2.5D Interposer Design
A typical 2.5D substrate application supports the interfacing of one or more high-density semiconductors. While the upper surface will accommodate a majority of semiconductor redistribution and/or die-to-die interface for multiple die applications, the primary I/O channels and power and ground terminals are transferred to the bottom surface of the interposer through plated or filled microvias for routing to an array pattern of terminals designated to interface with the intermediate package substrate or host PCB structure requiring significantly lower circuit density. Although the overall circuit density of the 2.5D interposer is significantly greater than the mainstream HDI circuit board, the commercial CAD tools already available for PCB circuit routing should accommodate most interposer development activity.
In preparation for developing the interposer, designers are advised to prepare a description of the proposed substrate, detailing the semiconductor element(s) physical parameters, intended use environment, and timeline anticipated for development. The 2.5D substrate fabricator can then recommend a suitable base material (organic, silicon or glass) and define the fabricator’s via forming methodologies, metalization process capabilities, and circuit geometry limitations.
Base Materials
The primary base materials utilized for the 2.5D interposer applications include glass-reinforced organic laminates, silicon (wafers or panels), and ruggedized glass panels.
To read this entire column, which appeared in the November 2019 issue of Design007 Magazine, click here.
More Columns from Designer's Notebook
Designers Notebook: Basic PCB Planning Criteria—Establishing Design ConstraintsDesigners Notebook: Layer Stackup Planning for RF Circuit Boards
Designers Notebook: Addressing Future Challenges for Designers
Designers Notebook: Impact of Advanced Semiconductor Packaging on PCB Stackup
Designers Notebook: Implementing HDI and UHDI Circuit Board Technology
Designer's Notebook: Heterogeneous Integration and High-density SiP Technologies
Designers Notebook: PCB Design and IPC-CFX for Assembly Automation
Designer’s Notebook: What Designers Need to Know About Manufacturing, Part 2