Estimated reading time: 3 minutes
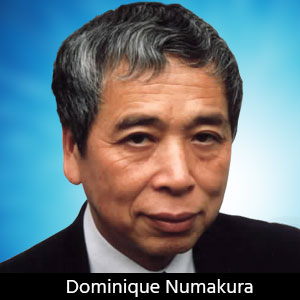
EPTE Newsletter: Next-Generation Flex Circuits—Elastic
My experience in the flex circuit industry spans almost 40 years. Industry production volume grew exponentially during my career as circuit manufacturing shifted from North America and Europe to Eastern Asia. Japan was the manufacturing leader for the consumer market, but that has spread amongst new companies in Taiwan, Korea, and China.
The number of countries that manufacture circuits has expanded, but the basic construction and manufacturing process remains the same. While circuit density is much higher, and automated processes lower manufacturing costs, circuit designers still use single-sided, double-sided, and rigid-flex constructions in their designs. Several new design capabilities are now available using flex circuits. They are revolutionary due to their unique performances and cannot be created using traditional flex circuits. Let’s look at some of these next-generation flexible circuits.
Wearable electronics and health care devices brought a need for elastic, flexible circuits. Traditional flexible circuits are built on thin, flexible, plastic films, such as polyimide films and polyethylene terephthalate (PET) films. The standard construction of these flexible circuits allows them to flex over 10 million times and is the reason they are employed as the major wiring material for mechanical and electronic devices found in hard disc drives and inkjet printers.
New applications from wearable and medical devices demanded elasticity for circuits that attach to the human body. Traditional flexible circuits cannot satisfy the new requirements of these products. Generating fine traces from the circuits’ base films relied on dimensional stability, but new applications are completely different.
Several circuit manufacturers and material suppliers are collaborating to develop new elastic, flexible circuits. Urethane rubber could be an appropriate base material once its relatively low-heat resistance is improved. Silicone rubber is the perfect material to use as the base layer and cover coating, due to its heat resistance and transparency. The increase in cost is the only problem.
Elastic conductor material has to be addressed. One solution is to have laminate suppliers develop copper-clad laminates with elastic sheets. Circuit manufacturers could etch the copper foil to generate the circuits using a typical manufacturing process for flexible circuits. Copper foils do not have the equivalent elasticity as rubber materials, so conductors have to use a meander pattern (Figure 1). This pattern allows the circuits to stretch by 50%.
Creating flexible conductors using a screen-printing process could be another choice for elastic conductors. Printed conductors can have a much higher elasticity compared with copper foils depending on the ink used for the binder material, but the circuit’s conductivity can decrease by one hundredth.
Another challenge with elastic conductors is they are not very stable. The resistance of the conductor is proportional to the elongation of the circuit. For example, when the conductor is stretched by 100%, the resistance doubles. This necessitates the use of meander patterns for printed conductors. Unfortunately, when using meander patterns instead of straight patterns, the amount of space needed for circuits increases. The circuits are larger, and a rise in costs is inevitable due to an increase in the usage of materials. It may need supplemental ideas and experience to build high-density circuits on the elastic substrates.
Creating elastic circuits does not employ conventional thinking. Because the resistance from the elastic conductor is proportional to its elongation, we can estimate how much the conductor is stretched measuring its resistance. This is the basic mechanism of the strain gauge.
The demands for elastic, flexible circuits will grow significantly in the next few decades as the market for wearable, and medical electronics will continue to grow. This segment forces us to think outside of the box for material usage, design ideas, and manufacturing processes. Anything is possible.
This column originally appeared in the June 2020 issue of Design007 Magazine.
More Columns from EPTE Newsletter
EPTE Newsletter: Travel to Japan During COVIDEPTE Newsletter: A New COVID Surge in Taiwan?
EPTE Newsletter: COVID-19 PCR Test in Japan
EPTE Newsletter: Japan Failing in Vaccine Distribution
EPTE Newsletter: A Long Trip to the U.S.
EPTE Newsletter: Ten Years After Fukushima
EPTE Newsletter: Taiwan Releases 2020 PCB Production Numbers
EPTE Newsletter: The Printed Circuit Industry in China