-
- News
- Books
Featured Books
- design007 Magazine
Latest Issues
Current IssueShowing Some Constraint
A strong design constraint strategy carefully balances a wide range of electrical and manufacturing trade-offs. This month, we explore the key requirements, common challenges, and best practices behind building an effective constraint strategy.
All About That Route
Most designers favor manual routing, but today's interactive autorouters may be changing designers' minds by allowing users more direct control. In this issue, our expert contributors discuss a variety of manual and autorouting strategies.
Creating the Ideal Data Package
Why is it so difficult to create the ideal data package? Many of these simple errors can be alleviated by paying attention to detail—and knowing what issues to look out for. So, this month, our experts weigh in on the best practices for creating the ideal design data package for your design.
- Articles
- Columns
- Links
- Media kit
||| MENU - design007 Magazine
Book Excerpt: Thermal Management With Insulated Metal Substrates, Part 3
July 1, 2020 | Didier Mauve and Ian Mayoh, VentecEstimated reading time: 2 minutes
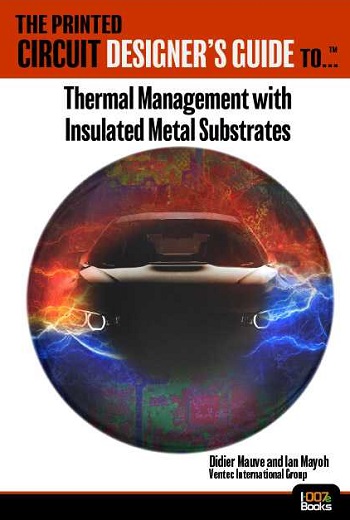
The following is an excerpt from Chapter 3 of "The Printed Circuit Designer's Guide to... Thermal Management With Insulated Metal Substrates," written by Ventec International Group’s Didier Mauve and Ian Mayoh. In this free eBook, the authors provide PCB designers with the essential information required to understand the thermal, electrical, and mechanical characteristics of insulated metal substrate laminates.
Chapter 3: Developments in Insulated Metal Substrate Laminates
The insulated metal substrate concept is not new. Materials were available as long ago as the mid-1960s for specific niche-market applications. However, the exponential growth in LED lighting has been the main driver for the development of improved versions in volume manufacture. Insulated metal substrate laminates are now firmly established as the preferred base material for the fabrication of printed circuits for high-brightness LED lighting and DC power conversion applications because they offer cost-effective performance with straightforward fabrication, good mechanical stability, and a range of thermal conductivities to suit particular configurations.
Although thermal PCB design technology has been predominantly single-sided, multilayered constructions are now possible through resin-coated foil and resin-coated film options. The use of thermally conductive prepregs and copper clad thin laminates manufactured with them, which can be bonded to the insulated metal substrate or co-laminated with high Tg or low Dk and Df cores and prepregs, have also made multilayered constructions possible.
The recent progress made by these thermal prepregs and thin cores allow engineers to design multilayered PCBs with integrated thin thermal layers. This opens up many possibilities, particularly when convection is not an option due to space, or real estate, and the cost of additional radiators is a concern.
Dielectric Layer
The key element of an insulated metal substrate material is the thermally conductive dielectric layer between the copper foil and the aluminum plate. This may be a woven-glass reinforced-resin composite (prepreg), as in a conventional laminate construction, or a layer of unreinforced resin. The resin itself is typically a halogen-free epoxy-laminating resin. Whereas a conventional FR-4 laminate would have very poor thermal conductivity, the thermal conductivity of the resin component is significantly improved by loading it with up to 70% of a thermally-conductive ceramic filler. The resin must also continue to serve the fundamental purpose of reliably bonding the insulated metal substrate construction together under potentially severe thermal-cycling conditions.
The thermal conductivity of glass-reinforced materials is still limited by the nature of the glass, so it is the non-reinforced dielectrics that have the lowest thermal resistance. However, they demand critical control in manufacture to maintain consistency of dielectric thickness, whereas glass fabric provides a natural mechanical spacer.
To download this free eBook, published by I-Connect007, click here.
To view the entire I-Connect007 eBook library, click here.
Testimonial
"We’re proud to call I-Connect007 a trusted partner. Their innovative approach and industry insight made our podcast collaboration a success by connecting us with the right audience and delivering real results."
Julia McCaffrey - NCAB GroupSuggested Items
Statement from the Global Electronics Association on the July 2025 Tariff on Copper Foil and Electronics-Grade Copper Inputs
07/31/2025 | Global Electronics AssociationWe are disappointed by today’s decision to impose a 50% tariff on imported copper foil and other essential materials critical to electronics manufacturing in the United States.
Considering the Future of Impending Copper Tariffs
07/30/2025 | I-Connect007 Editorial TeamThe Global Electronics Association is alerting industry members that a potential 50% tariff on copper could hit U.S. electronics manufacturers where it hurts.
Connect the Dots: Sequential Lamination in HDI PCB Manufacturing
07/31/2025 | Matt Stevenson -- Column: Connect the DotsAs HDI technology becomes mainstream in high-speed and miniaturized electronics, understanding the PCB manufacturing process can help PCB design engineers create successful, cost-effective designs using advanced technologies. Designs that incorporate blind and buried vias, boards with space constraints, sensitive signal integrity requirements, or internal heat dissipation concerns are often candidates for HDI technology and usually require sequential lamination to satisfy the requirements.
OKI Launches Rigid-Flex PCBs with Embedded Copper Coins Featuring Improved Heat Dissipation for Space Equipment Applications
07/29/2025 | BUSINESS WIREOKI Circuit Technology, the OKI Group’s printed circuit board (PCB) business company, has developed rigid-flex PCBs with embedded copper coins that offer improved heat dissipation for use in rockets and satellite-mounted equipment operating in vacuum environments.
Designers Notebook: Basic PCB Planning Criteria—Establishing Design Constraints
07/22/2025 | Vern Solberg -- Column: Designer's NotebookPrinted circuit board development flows more smoothly when all critical issues are predefined and understood from the start. As a basic planning strategy, the designer must first consider the product performance criteria, then determine the specific industry standards or specifications that the product must meet. Planning also includes a review of all significant issues that may affect the product’s manufacture, performance, reliability, overall quality, and safety.