-
- News
- Books
Featured Books
- design007 Magazine
Latest Issues
Current IssueShowing Some Constraint
A strong design constraint strategy carefully balances a wide range of electrical and manufacturing trade-offs. This month, we explore the key requirements, common challenges, and best practices behind building an effective constraint strategy.
All About That Route
Most designers favor manual routing, but today's interactive autorouters may be changing designers' minds by allowing users more direct control. In this issue, our expert contributors discuss a variety of manual and autorouting strategies.
Creating the Ideal Data Package
Why is it so difficult to create the ideal data package? Many of these simple errors can be alleviated by paying attention to detail—and knowing what issues to look out for. So, this month, our experts weigh in on the best practices for creating the ideal design data package for your design.
- Articles
- Columns
- Links
- Media kit
||| MENU - design007 Magazine
Estimated reading time: 3 minutes
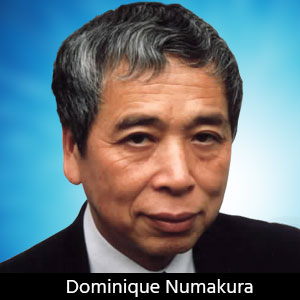
EPTE Newsletter: Polymer Thick-film Circuits: Practical or Not?
The subtractive process (an etching process of copper foil) is the primary technology used to build various printed circuits. On the other hand, printable electronics are making significant progress in this area, and several researchers predict the traditional etching processes will be replaced by printing technologies in the near future. The advantages are both technical and economical for manufacturers, but is this practical?
I currently use both technologies, depending on the task at hand. Figure 1 compares technical capabilities between etching processes and printing processes. The etching process (red line) assumes typical photolithography and etching with flexible copper laminates. Thick-film printing means screen-printing of silver pastes on plastic films (blue line).
Because the red line and blue line show different patterns, they have different advantages and disadvantages. It’s not practical to compare all of the bullet points for both technologies; instead, we should consider whether the process is capable of building key parts at an acceptable cost. Once we pass the cost test, we can determine if there are any critical issues with the technologies.
It is easy to determine which technology to employ since both have measurable performance at each milestone. Usually, the conductivity for thick-film circuits is two or three orders lower than copper-etched circuits, so there is no argument against using copper foil circuits. Since silver ink conductors have migration issues, thick-film circuits require special constructions to guarantee reliable insulation. Progress and innovation over the last 20 years alone have changed the process of generating fine lines with thick-film circuits. Volume manufacturers can produce 50-micron line and space on plastic films. Thick-film circuits have the equivalent fine line capabilities as thin copper foil circuits. However, there is still a gap between reliably technology and process yields.
A thick-film printing process can generate low-cost via holes for double-sided circuits and multilayer circuits. This could be an alternative process for additional layers. Traditional etching processes require an appropriate flexible copper-clad laminate as the starting material. On the other hand, a thick-film process is available for all kinds of plastic films, and elastic materials are available for wearable devices.
Generally, copper foil circuits are designed to have enough heat resistance for soldering, but most thick-film circuits do not have a high heat resistance due to the organic matrix of the conductive inks. One advantage of the thick-film process is the ability to create operative layers for functional devices, such as flexible sensors, photovoltaic cells, batteries, displays, and more.
This is achieved from a simple printing process assuming the appropriate inks are available. A traditional etching process has little to no capabilities for functional materials.
The actual designs for flexible devices coupled with the manufacturing processes are not simple. If you have the ability to use a traditional etching process, this is a safe bet. However, if the construction is not possible using the etching process, you should consider the thick-film printing process with appropriate ink materials.
Headlines
1. Mitsubishi Electric (electric and electronic company in Japan)
Developed a multi-cell GaN-HEMT with diamond substrate for industrial uses that makes power efficiency 10% higher, reducing the temperature increase to one-sixth.
2. NEDO (R&D organization)
Will start field test of a biomass power generator in October. Bamboo is available as the main fuel material.
3. Taiwan Pucka (flexible circuit manufacturer in Taiwan)
Established the hybrid process of polymer thick-film and copper plating. The new process significantly reduces the conductor resistance in the circuits.
4. Toshiba Memory (semiconductor manufacturer in Japan)
Expects a big loss in 2019. Plans to buy SSD business of Lite-On in Taiwan.
5. Murata (device supplier in Japan)
Had an open house at the newly built battery manufacturing Koriyama plant, which will be the core facility of the battery business.
6. Renesas Electronics (semiconductor manufacturer in Japan)
Added small, 64-pin package for a 32-bit microprocessor “RX651 Series” as the ultra-miniature IoT module.
7. TDK (device supplier in Japan)
Rolled out a film capacitor series “B3277M” for the convertor of solar power generators that has stable performances under severe circumstances.
8. AGC (glass product manufacturer in Japan)
Decided to build a new manufacturing line of cover glasses in their China plant for automobile displays.
9. Nikon (optical device manufacturer in Japan)
Commercialized a 3D printer that can build metallic subjects “Lasermeister 100A.”
10. Nippon Chemicon (device supplier in Japan)
Unveiled a compact camera module with two million pixels developed for drive recorders and has high reliability against high temperature and vibration.
11. Kyocera (device manufacturer in Japan)
Released a low-height (4 mm) BTB connector series with 0.5-mm pitch for automobile applications, such as LiDAR, microwave radar, and monitor cameras.
Dominique K. Numakura is the managing director of DKN Research LLC.
More Columns from EPTE Newsletter
EPTE Newsletter: Travel to Japan During COVIDEPTE Newsletter: A New COVID Surge in Taiwan?
EPTE Newsletter: COVID-19 PCR Test in Japan
EPTE Newsletter: Japan Failing in Vaccine Distribution
EPTE Newsletter: A Long Trip to the U.S.
EPTE Newsletter: Ten Years After Fukushima
EPTE Newsletter: Taiwan Releases 2020 PCB Production Numbers
EPTE Newsletter: The Printed Circuit Industry in China