-
- News
- Books
Featured Books
- smt007 Magazine
Latest Issues
Current IssueDo You Have X-ray Vision?
Has X-ray’s time finally come in electronics manufacturing? Join us in this issue of SMT007 Magazine, where we answer this question and others to bring more efficiency to your bottom line.
IPC APEX EXPO 2025: A Preview
It’s that time again. If you’re going to Anaheim for IPC APEX EXPO 2025, we’ll see you there. In the meantime, consider this issue of SMT007 Magazine to be your golden ticket to planning the show.
Technical Resources
Key industry organizations–all with knowledge sharing as a part of their mission–share their technical repositories in this issue of SMT007 Magazine. Where can you find information critical to your work? Odds are, right here.
- Articles
- Columns
Search Console
- Links
- Media kit
||| MENU - smt007 Magazine
Estimated reading time: 6 minutes
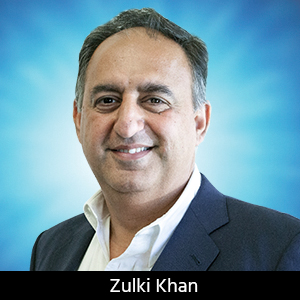
Zulki's PCB Nuggets: Onshoring for PCB Microelectronics Production?
In many instances, OEMs fail to realize that some of their PCB assembly and manufacturing production going offshore can easily be brought back to the United States, saving them time, money, and best of all, keeping their IP intact and protected. Certainly, the lion’s share of PCB SMT production continues to be found at offshore centers that offer lower cost of labor.
However, as we’ve said in earlier columns, a variety of OEMs, including medical device OEMs, are creating next generations of smaller products that demand PCB microelectronics assembly and manufacturing. Much of that type of PCB assembly and manufacturing is currently performed offshore.
But many OEMs may not be aware that here in the U.S., microelectronics assembly and manufacturing is leading in technology advances and provides OEMs a relatively easy way to bring that production back to the U.S., compared to onshoring PCB SMT production.
Facts associated with both types of PCB production clearly tell you this. Let me present those facts by comparing and contrasting those two types of PCB production.
Traditional manufacturing takes into account large machinery, including paste dispensing, pick-and-place, reflow, and wash cycle. But then you have through-hole components to mount on a board. Those components are installed, they undergo wave soldering, and then comes the second batch of cleaning after the first SMT cleaning has already been performed. Cleaning cycles involve machines for de-ionized, batch, and ultrasonic cleaning. In some cases, there are two cleaning cycle processes; sometimes, there can be three cycles.
Basically, everything is big in traditional SMT manufacturing. We’re dealing with big physical sizes, bigger footprints of equipment, considerably large rooms, and resources to assemble and manufacture those PCBs. If you’re doing box build, you need even more physical area since those products are big and bulky. In some cases, they are heavy, for example with traditionally large medical electronic machines.
Compare with Microelectronics
Let’s now compare and contrast SMT production with PCB microelectronics, since microelectronics deal with products, device packages, substrates, and boards that are smaller in size. Those boards could be rigid, a combination of rigid and flex or they could be completely flex boards.
There are different boards which are smaller in size and footprint. Now, we have to consider that most of the microelectronics work is performed in a cleanroom, which is an enclosed environment using smaller footprint equipment.
There are fewer wet processes like washing or using alcohol for cleaning stencils, for example. Therefore, it’s a smaller, compact, enclosed environment, and footprints are much smaller for microelectronics assembly machines. The reason for it to be like that is simply because the product—which could be medical devices like indigestible, implantable, or insertable or even wearable devices—are by their very nature, compact, lighter, and smaller in size.
Also, there are fewer steps taken in a cleanroom to make the product, compared to traditional SMT manufacturing. When dealing with microelectronics assemblies, either conductive or non-conductive epoxy is dispensed using dispensing machines and then the die is attached, followed by wire bonding. This is a general approximation for the microelectronics assembly process.
Also, even if cleaning is performed inside the cleanroom, plasma is used, which takes a relatively small process-based application compared to de-ionized water cleaning or batch cleaning using a huge machine for traditional SMT manufacturing, including water connections and di-ionizing beds.
Everything is efficiently performed within a small, compact, and safe area, as long as all cleanroom parameters are met. Some cleanrooms are categorized as Class 10,000; some are 100,000; some are 1,000, depending on the product you are making. HEPA filtration systems, the number of particles that are flowing through the cleanroom, all have to be within the allowable range for optimally making these microelectronics products.
Since PCB microelectronics assembly is an enclosed environment or cleanroom with smaller footprint machines and fewer number of steps, it is considerably easier for it to be brought back to the U.S., compared to SMT manufacturing.
Criteria
But there’s certain criteria that must be considered to select the proper U.S. PCB microelectronics assembly and manufacturing line (Figure 1). Microelectronics, by its very nature, possesses the following aspects.
Figure 1: Certain criteria must be considered in selecting the proper U.S. PCT microelectronics assembly and manufacturing line.
First, it has to be very precise. Machine tolerances for wire bonding, die attach or flip chip must be very tight. In some cases, accuracy required for die attachment or wire bonding is within 5–10 µm which is a fraction of a mil. A mil is 100 thousandths of an inch; 25 µm makes 1 mil.
For instance, if you’re putting up a die on a 10 µm tolerance, you are using very accurate, reliable, and highly sophisticated machines. This high level of precision allows you to not only view at those depths and details the video images, but you are able to place the die and later do the testing by either shear pull testing or bond pull testing to assure that the microelectronics assembly is done properly and there are no remaining issues.
Second, there is no room for making errors when dealing with microelectronics. You have to perform all the assembly steps one time and you have to do it perfectly. Why? Because once the microelectronics die is attached or wire bonded, you cannot rework that step to fix your mistake.
Let’s say, out of 200 wires, if four wires are pulled or broken during the assembly or testing, it’s virtually impossible to put those wires back on the wire bond. You have to basically replace the whole die and re-do the assembly. You have to do it right. You have to do it 100% accurately when it comes to microelectronics.
On the other hand, SMT manufacturing consumes a fair amount of physical area on the assembly floor to perform rework. For example, if you have a BGA that has an open or a short seen under x-ray, you can pull it off and re-ball it. You can then clean the surface and put the BGA back again. The same is true for other components like resistors, capacitors, and even QFN devices.
Most, if not all components, can be reworked in traditional SMT manufacturing when problems are identified after being tested or when they undergo AOI, or x-ray and misplaced or mis-oriented components are found. Those components can be pulled and put back the right way and then AOI is performed again to ensure the correct orientation.
But if you do place a die at wrong orientation when it comes to die attach, then that die is gone. Wire bonding needs to come off and you need to do the whole assembly again. This means you cannot use the same die again because it’s almost impossible to work a die and try to fix it or rework it.
These are the differences. And these are the reasons it is considerably easier to bring portable, indigestible, implantable, and insertable devices back to the U.S. in terms of microelectronics assembly production compared to traditional SMT.
In summary, it’s a fact that in the U.S. there are skilled manpower, process engineers, excellent state-of-the-art technologies, and machines with extremely high tolerance, as well as cleanrooms that meet all the requirements for successfully assembling and manufacturing small, yet highly advanced products for a variety of OEMs.
Zulki Khan is the president and founder of NexLogic Technologies Inc.
More Columns from Zulki's PCB Nuggets
Zulki's PCB Nuggets: Cleanliness is Next to ReliabilityZulki’s PCB Nuggets: Thermal Compression Bonding for Extra Fine Pitch Flip Chips
Zulki’s PCB Nuggets: WBAN Steps Into PCB Microelectronics Assembly
Zulki’s PCB Nuggets: Photonics Comes to PCB Microelectronics Assembly
Zulki’s PCB Nuggets: Sub-Micron Die Bonding—Don’t Be Misled by Five Micron Placement Standard
Zulki’s PCB Nuggets: Meet the New Player in PCB Microelectronics Assembly—Interposers
Zulki’s PCB Nuggets: How Effective Is Your PCB Microelectronics Assembly?
Zulki’s PCB Nuggets: Five Key Benefits for Onshoring PCB Microelectronics Assembly