-
- News
- Books
Featured Books
- design007 Magazine
Latest Issues
Current IssueProper Floor Planning
Floor planning decisions can make or break performance, manufacturability, and timelines. This month’s contributors weigh in with their best practices for proper floor planning and specific strategies to get it right.
Showing Some Constraint
A strong design constraint strategy carefully balances a wide range of electrical and manufacturing trade-offs. This month, we explore the key requirements, common challenges, and best practices behind building an effective constraint strategy.
All About That Route
Most designers favor manual routing, but today's interactive autorouters may be changing designers' minds by allowing users more direct control. In this issue, our expert contributors discuss a variety of manual and autorouting strategies.
- Articles
- Columns
- Links
- Media kit
||| MENU - design007 Magazine
Estimated reading time: 4 minutes
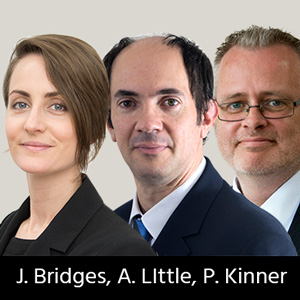
Sensible Design: Can Solvent-free UV-cure Coatings Increase Stability and Throughput?
With environmental awareness at an all-time high, companies are looking for greener options in terms of the chemical products they use for the manufacture and protection of electronics, including conformal coatings that are applied to protect the metal surfaces from corrosion, condensation, dielectric breakdowns, and that mitigate against tin whisker formation and conductive metal particles.
Traditionally, these materials have been solvent-based, resulting in low viscosity, easy-to-use materials. However, the use of solvents has become more restricted and there is increasing demand for solvent-free technology. In this month’s column, I’ll be looking at a particular solvent-free coating group—UV cure coatings. I will examine the benefits that these particular coatings bring to the production line and unveil test data to reveal their performance values.
What Are the Key Benefits of Solvent-free Coatings to Manufacturers?
Aside from solvent-free materials being a smart choice, whereby solvent emissions from your facility will be much lower, there are cost savings due to compliance with legislative requirements, depending upon local, regional, and national legislation. UV-cure materials are also non-flammable and are a lower hazard to human health, resulting in potential cost-savings on insurance. Often, the energy demands required for curing these materials are much lower than for solvent-based materials, resulting in reduced energy bills and reduced CO2 emissions.
But how do they perform? Solvent-free materials are generally applied slightly more thickly, resulting in increased coverage, and therefore greater protective capability. The formulations are also more modern and deliver a better capability to meet the increased protective demands of new applications, e.g., automotive industry thermal shock cycling or aerospace increased condensation resistance. UV-curable materials cure extremely rapidly (in seconds) when exposed to UV radiation of a suitable wavelength and intensity, making them an extremely interesting technology for increasing factory throughput and reducing production footprint. UV-curable materials also provide good protective properties and improved chemical resistance compared with other cure types.
Why Do We Need a Secondary Cure?
Unfortunately, light only travels in straight lines and curing is line of sight only. Due to the 3D nature of a PCB, it is likely that some areas of the board will not attain full exposure to the light, particularly material on the backside of component leads and underneath components. For this reason, UV-curable materials need to contain a secondary cure mechanism, which can be a moisture, chemical, or heat-based mechanism. Moisture-curing has traditionally been favored because it requires no additional processes. However, although the material is generally well cured in light exposed areas, the diffusion of moisture into the coating and the emission of the leaving groups can be difficult. The better the coating barrier, the longer the secondary-curing process; many days, weeks, months, and even years have been reported.
What Are the Issues With Heat Activated Curing?
Heat-activated secondary curing processes require additional processes and time, which eliminates the benefit of the rapid primary cure. Speaking of which, the initial rapid cure can generate significant levels of stress, and seldom leads to more than 70–80% of the theoretical conversion to polymer, meaning that the materials can contain reactive groups that remain dormant. Once exposed to high temperatures (100°C+) additional polymerisation can take place, resulting in the materials continuing to harden, change properties, and be more prone to cracking during thermal shock transitions.
Chemical Secondary Cure Time and Thermal Aging
Materials containing a chemical secondary process will cure completely within six to eight hours at room temperature after exposure to suitable long wavelength UV light. Due to the unique formulation of these materials, residual stress is minimised and the cure proceeds to a very high level of conversion, resulting in minimal changes in properties during thermal aging. After thermal age testing, the results showed that the conventional materials tended to be very stiff and inelastic at sub-ambient temperatures, whereas the secondary chemical cure system remained elastic until -20°C, but still retained a degree of elongation even at -40°C.
UV Chemical and UV Moisture Cure Test Results
While the lack of changes in physical properties during thermal aging are an important parameter in material selection, the key to performance in an end-user application is whether a material can survive the required thermal shock profile without cracking or impacting further stress on solder joints. To investigate this, we selectively coated 12 automotive engine control units at a normal thickness with five different coatings in a full thermal shock experiment test from -40°C to +130°C, 0°C to 130°C, and -40°C to +60°C.
After 250 cycles of each test cycle, the 12 boards were visually inspected for evidence of cracks in the coating, and the most striking observation from the tests was that the materials which had the most stable properties during the thermal aging process were the chemical cure and UV/chemical cure materials. The UV/chemical cure remained virtually crack free after 1,000 thermal shock cycles (-40°C to +130°C) and also completed curing within six hours compared to the extremely long time required to complete the UV/moisture cure. The UV/chemical-cure material had far greater stability of the key physical properties during thermal aging when compared to UV/moisture-cure materials. This increased stability led to a considerably improved thermal shock performance when compared to the traditional UV/moisture-cure materials.
So, there you have it: Environmentally friendly materials are available now, including our unique bio-based UVCLX coating, which guarantees full cure within 24 hours and contains 75% bio-organic content from renewable sources. New developments are in the pipeline and, with time, these UV cure, solvent-free, and bio-based materials will open up new avenues for compliance across many disciplines.
This column originally appeared in the July 2022 issue of Design007 Magazine.
More Columns from Sensible Design
Sensible Design: Automotive Conformal Coating ApplicationsSensible Design: Green Coats Are In
Sensible Design: Encapsulation Resins—PU vs. Epoxy
Sensible Design: Avoiding Conformal Coating Pitfalls
Sensible Design: Comparing Traditional and Bio-based Resins
Sensible Design: All Resins Are Not Created Equal
Sensible Design: Optimize Your Thermal Management
Sensible Design: Why Some Conformal Coatings Fail in Service