-
- News
- Books
Featured Books
- design007 Magazine
Latest Issues
Current IssueProper Floor Planning
Floor planning decisions can make or break performance, manufacturability, and timelines. This month’s contributors weigh in with their best practices for proper floor planning and specific strategies to get it right.
Showing Some Constraint
A strong design constraint strategy carefully balances a wide range of electrical and manufacturing trade-offs. This month, we explore the key requirements, common challenges, and best practices behind building an effective constraint strategy.
All About That Route
Most designers favor manual routing, but today's interactive autorouters may be changing designers' minds by allowing users more direct control. In this issue, our expert contributors discuss a variety of manual and autorouting strategies.
- Articles
- Columns
- Links
- Media kit
||| MENU - design007 Magazine
Estimated reading time: 5 minutes
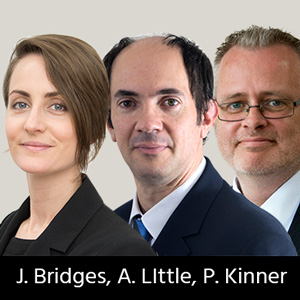
Sensible Design: Comparing Traditional and Bio-based Resins
In this month’s column, two of Electrolube’s leading resin specialists have collaborated to give you the clearest focus of how introducing bio-based resin systems will impact your production process and the benefits they bring in terms of performance. Beth Turner is Electrolube’s senior technical specialist and Beth Massey is Electrolube’s global product manager for resins. Having two Beths working on resins may be a little confusing, but this column should help demonstrate the unique input each has and alleviate any confusion. Here we dive into how bio-based resins differ from their traditional counterparts, examining what they can bring to the table, aside from their obvious sustainable and environmentally friendly benefits.
What percentage of the overall content can reasonably be bio-based without causing a detrimental effect to the performance of the product, and is the bio content added to part A or B?
The honest answer to this question is quite simple: It depends. Realistically, up to 70% of content can be bio-based, and both A and B can contain bio-based materials. The 70% limit has more to do with availability of bio-based alternatives than high levels having a detrimental effect. It’s likely that some components of the formulation will never have a bio-based alternative, but the benefits we are seeing from changing to bio-based raw materials, where possible, does suggest we should push to include content as high as possible. It goes without saying that bio-coatings have significantly less impact on the environment and meet the ethical needs of manufacturers and end users. However, the most surprising benefit we have observed is the improvement in performance. Even additives such as powders can be bio-based.
Does a particular chemistry, i.e., epoxy or polyurethane, lend itself to removing some of the chemicals present and substituting them for bio-based content. If yes, why is this?
Both are suited. If we refer to Beth Turner’s award-winning white paper on next generation bio-resins, she states, “Nature offers an abundance of macromolecules and smaller molecular weight compounds that provide renewable sources for polymers, as opposed to crude oil. These renewable resources make ideal structural backbones for the synthesis of biopolymers, renewable-based monomers, fillers and additives, the key ingredients for polyurethane and epoxy thermoset materials. Research and development to promote innovative solutions that lead to a sustainable economy shows that bio-based materials can deliver a viable alternative to materials derived from crude oil, even in electronic encapsulation applications.”
Do bio-based resins behave in a different way when being poured or when curing compared to their chemical versions, and are the tech datasheets almost identical in terms of the qualities exhibited?
Interestingly, bio-based resins show the same dispensing behaviour and cure profiles as conventional resins, so there is no need to invest in adaptive equipment. There is no negative effect on processability or curing when using bio-based materials and performance is equivalent. However, we do see significant benefits in cured properties when select bio-based raw materials are used. Combining a bio-based polymer matrix and hardener with a biogenic filler offers a significant improvement in thermal conductivity compared to a fully synthetic polyurethane using a synthetic polymer matrix derived from crude oil and mineral rock filler. The bio-based resin also offers better electrical insulation and thermal stability while also having a higher resistance to hydrolysis vs. a synthetic polyurethane resin.
Are bio-based products gaining popularity purely due to their association with sustainability or do they exhibit qualities that are superior to their chemical alternatives?
Initial interest is often sparked because of the increasing focus on sustainability but this is extended by research showing significant performance benefits for bio-based resins. The best way to succeed with bio-based products is to ensure consumers do not have to compromise on quality in order to make the more sustainable choice. As was documented in Beth Turner’s white paper, use of certain bio-based raw materials offers substantial benefits in terms of the cured resin’s electrical and thermal performance vs. synthetic-based raw materials. The fact that these high-performance, bio-based materials are a more sustainable solution is really an added bonus. It’s especially exciting that some of the raw materials tested were from biogenic waste, adding another layer of sustainability by repurposing waste material from other industries.
In your experience, is sustainability something that genuinely affects manufacturers and their reputation in the market as doing their absolute best to reduce their carbon footprint, or is this more of a box-ticking exercise?
I think we are seeing a sea change in attitude at the moment, from sustainability seen as a niche focus to now being a big concern for society as a whole. In the past, the focus has been on sustainability almost as a marketing tool, leading to “greenwashing,” but more manufacturers are realising that sustainability needs to be at the core of what they do, both to meet increasing consumer demands for sustainable products and to future-proof their business. We’ve seen supply shortages and price volatility making synthetic materials, such as those derived from crude oil, a much less attractive choice, which is an additional commercial incentive toward using more sustainable bio-based materials. The fact that our research shows using certain bio-based materials in the formulation improves resin properties also means a bio-based resin doesn’t need to be sold on sustainability credentials alone. Its performance speaks for itself, as can be seen with one of our products that is a high temperature, chemically-resistant polyurethane resin.
Electrolube’s extensive research and findings conclude that the future looks extremely promising for bio-based resins, which bring distinct performance advantages in harsh environments, including underwater applications as well as hot and humid operating environments. Bio-based chemicals are highly suited to a wide variety of applications within the electronics industry and even lend themselves to RF applications. One Electrolube product has a bio-sourced content of over 60% and has been used in many sensor applications. It is likely that the bio-based chemicals share within the electrochemical production segment will increase, and electrochemical manufacturers and associated OEMs will become an important part of the bio-economy of the future.
This column originally appears in the September 2022 issue of Design007 Magazine.
More Columns from Sensible Design
Sensible Design: Automotive Conformal Coating ApplicationsSensible Design: Green Coats Are In
Sensible Design: Encapsulation Resins—PU vs. Epoxy
Sensible Design: Avoiding Conformal Coating Pitfalls
Sensible Design: All Resins Are Not Created Equal
Sensible Design: Can Solvent-free UV-cure Coatings Increase Stability and Throughput?
Sensible Design: Optimize Your Thermal Management
Sensible Design: Why Some Conformal Coatings Fail in Service