-
- News
- Books
Featured Books
- design007 Magazine
Latest Issues
Current IssueProper Floor Planning
Floor planning decisions can make or break performance, manufacturability, and timelines. This month’s contributors weigh in with their best practices for proper floor planning and specific strategies to get it right.
Showing Some Constraint
A strong design constraint strategy carefully balances a wide range of electrical and manufacturing trade-offs. This month, we explore the key requirements, common challenges, and best practices behind building an effective constraint strategy.
All About That Route
Most designers favor manual routing, but today's interactive autorouters may be changing designers' minds by allowing users more direct control. In this issue, our expert contributors discuss a variety of manual and autorouting strategies.
- Articles
- Columns
- Links
- Media kit
||| MENU - design007 Magazine
Estimated reading time: 4 minutes
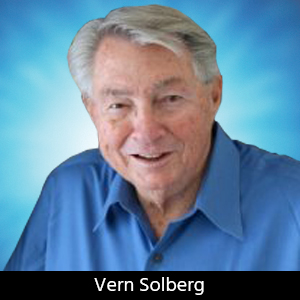
Designer's Notebook: PCB Design for Bare Board Testing
There are several testing methods used for certifying that the circuit board meets its defined quality level and intended functional criteria. Multilayer circuit boards have become increasingly complex: finer conductor line definition, blind and buried microvia interface, and smaller, finer-pitch SMT land pattern geometries. Visual assessment using automated optical inspection (AOI) is adopted to check all circuit layers prior to lamination and as a final examination of the end product.
Flying probe testing, in particular, is a method that uses multiple contactors designed to make rapid electrical contact on exposed conductive terminal sites of the PCB surface. Users have found that the flying probe electrical test is very accurate; it is capable of quickly measuring the electrical characteristics of each board with a high accuracy, ensuring that the board meets the specifications of the design. Probe contactors rapidly move across the circuit board’s surface, allowing the test to be completed in a short amount of time. This is beneficial when time is of the essence, such as when a product needs to be released to market quickly. The probes travel across the surface of the board, making contact at pre-designated locations to verify interconnect integrity.
Compared to fixed-probe testing, the flying probe test is not dedicated to a single board design and can test a variety of circuit board designs using the same testing system. By utilizing the CAD data, the probes can be preset to comply with an unlimited number of circuit patterns, enabling the uncompromised testing of individual or panel format circuit boards. Finally, the flying probe test is safe. To prevent the probe contactors from coming into contact with any other components or people, the probes are protected by a guard, minimizing the risk of damage or injury caused by faulty circuit boards.
Flying probe testing is one of the most efficient and cost-effective methods of testing PCBs. It is accurate, fast, flexible, and safe, making it the ideal solution for many types of testing requirements. A leading circuit board fabricator in the Silicon Valley recommends:
- Designated probe contact surfaces must be free of dielectric coatings, resist material, or solder mask
- The preferred surface area provided for probe contact is 0.50 mm (~0.020")
- Minimum probe contact area should not be less than 0.15 mm (~0.006")
- When probing via holes, the preferred land diameter is 0.25 mm (~0.010") but, depending on the test system employed, they may range between 0.20 mm and 0.50 mm (~0.008" and 0.020") diameter
The system shown in Figure 1 is equipped with eight probe heads (4X on the topside and 4X on the bottom) and can simultaneously probe both surfaces of the bare circuit board or panel, enabling micro-pad probe targets as small as 0.30 ?m.
The test system can provide probing speeds up to 180 touches per second and accuracy in the range of ±10 ?m, and repeatability of ±5 ?m.
Circuit board manufacturers note that the manufacturing process of printed circuit boards is complex, and the process is cumbersome. Any defects not detected during the post etching phase of the manufacturing process, if not corrected, will seriously affect the quality of the final product. In order to effectively control the progression of quality defects in the production process, and prevent the imperfections from occurring on future runs, prompt corrective action is warranted.
The following identifies defects that may occur during the circuit board fabrication process:
- Electroplating short circuit: When the copper conductors are closely spaced and equal in both height and width, copper bridging between circuit paths can occur. The cause of bridging is likely due to dry film resist breakdown during the plating process.
- Copper bridge short circuit: A very thin wire-like copper connection between two conductors forming a short circuit. The cause may be attributed to foreign particles that remain trapped between the resist film and copper surface.
- Insufficient etching: Where random copper blotches remain in the open, copper-free area, and where closely spaced conductors run in parallel for long distances. This may be due to etch chemical imbalance or when the duration for the etching process is too short.
- Scratch short circuit: When a short circuit remains after electroplating and etching. Typically attributed to scratches in the dry film resist by mechanical, human contact, or hair and other fine fibers falling on the board surface. These particles, if not removed before imaging and electroplating, will impede light access, resulting in copper bridging.
Overall, the flying probe test is an efficient and cost-effective method for testing circuit boards after fabrication is completed. It is accurate, fast, flexible, and safe, making it the ideal solution for many types of testing requirements. However, when the circuit board fails during electrical testing, there are other testing methods that can be implemented to identify defects.
The 3D X-ray inspection systems can provide 3D images of the circuit board by creating a series of 2D cross-sections to expose defects embedded in the board after lamination. While removing the defect on the inner layers of the board may not be practical, identifying and discarding a specific circuit board within a multiple unit panel format will ensure that it does not reach assembly. The images shown in Figure 2 represent the isolated X-ray view of defects within the inner-layer circuit conductor routing path.
In addition to visual and X-ray imaging, thermal imaging, EMI test, and solderability testing is often implemented to further certify that all boards are manufactured correctly and will be assembly process ready, and that any design flaws that would compromise product reliability are identified and corrected.
This column originally appeared in the March 2023 issue of Design007 Magazine.
More Columns from Designer's Notebook
Designers Notebook: Basic PCB Planning Criteria—Establishing Design ConstraintsDesigners Notebook: Layer Stackup Planning for RF Circuit Boards
Designers Notebook: Addressing Future Challenges for Designers
Designers Notebook: Impact of Advanced Semiconductor Packaging on PCB Stackup
Designers Notebook: Implementing HDI and UHDI Circuit Board Technology
Designer's Notebook: Heterogeneous Integration and High-density SiP Technologies
Designers Notebook: PCB Design and IPC-CFX for Assembly Automation
Designer’s Notebook: What Designers Need to Know About Manufacturing, Part 2