-
- News
- Books
Featured Books
- design007 Magazine
Latest Issues
Current IssueProper Floor Planning
Floor planning decisions can make or break performance, manufacturability, and timelines. This month’s contributors weigh in with their best practices for proper floor planning and specific strategies to get it right.
Showing Some Constraint
A strong design constraint strategy carefully balances a wide range of electrical and manufacturing trade-offs. This month, we explore the key requirements, common challenges, and best practices behind building an effective constraint strategy.
All About That Route
Most designers favor manual routing, but today's interactive autorouters may be changing designers' minds by allowing users more direct control. In this issue, our expert contributors discuss a variety of manual and autorouting strategies.
- Articles
- Columns
- Links
- Media kit
||| MENU - design007 Magazine
Estimated reading time: 8 minutes
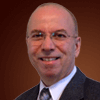
Bert's Practical Design Notes: Cross-Sectional Geometries
Whether you are new to signal integrity for PCB design or you are a veteran in the field, you undoubtedly will have to deal with various PCB cross-sectional geometries as part of your day job. This month’s column explores some of the more common geometries, and presents practical equations you can use to quickly determine the following:
- Odd-mode and even-mode impedance;
- Average/differential impedance; and
- Backward crosstalk/coupling coefficients from RLGC matrices extracted from 2D field solvers.
So, why do we need to understand the various PCB cross-sectional geometries anyway? Because they describe the details of the dielectric substrates, traces and reference planes within a PCB stackup. Their physical relationship to each other is used to predict the characteristic impedance and interaction of the respective traces. For all geometries, it is best to use a 2D field solver to help determine the correct impedance. Many EDA design tools have field solvers built into the layout tool to make your job easier.
There are really only three generic cross-sectional geometry paradigms with variations within each. They are:
- Coplanar
- Microstripline
- Stripline
CoplanarCoplanar geometry, sometimes called coplanar waveguide (CPW), is a signal conductor sandwiched between two coplanar reference conductors or planes as shown in Figure 1. This is a common transmission line structure for RF and microwave designs using single-sided printed circuit board technology. They also may be found in some mixed-mode RF/digital multi-layer designs.
Figure 1. Coplanar geometry. The reference planes are usually ground. The characteristic impedance is controlled by the signal trace width and the gap between it and reference planes. The closer the reference planes are to the trace, the lower the characteristic impedance. As a rule of thumb, the width of the reference plane on each side of the signal trace should be at least five times the distance between the left and right plane.
Microstripline
Microstripline, more commonly called microstrip, is the most popular transmission line geometry used in two- or four-layer printed circuit boards. An example is shown in Figure 2 (left). The characteristic impedance is controlled by the signal trace width, on one side of the substrate, and the thickness of the substrate attached to the reference plane below it. The thinner the dielectric is, the lower the characteristic impedance.
The embedded microstrip has the signal trace covered with prepreg or other dielectric material as illustrated in Figure 2 (right). Generally speaking, the thicker the dielectric material covering the trace is, the slower the speed of propagation of the signal.
Figure 2. Cross-sectional views showing microstrip (left) and embedded microstripline (right).
Stripline
Figure 3 shows an example of single stripline and dual stripline geometries. These geometries are typically found in multilayer PCBs of 6 layers or more. The characteristic impedance is controlled by the trace width, thickness and its proximity to the reference planes above and below. The closer one or both reference planes are to the trace, the lower the characteristic impedance. Compared to microstrip, the speed of propagation of the signal is slower for stripline geometries.
Single stripline has one signal layer sandwiched between two reference planes. If the signal layer is exactly spaced between the two reference planes, the geometry is called a symmetrical stripline. An asymmetrical stripline occurs when the signal trace is offset from the center of the cross-section.
Dual stripline geometries have two signal layers sandwiched between reference planes, and are mainly used to save layers; caveat is a trace on one layer is routed orthogonal to the trace on the other to mitigate crosstalk.
Figure 3. Cross section views showing stripline (left) and dual stripline (right).
Differential Pair Geometry
With differential signaling, a signal and its complement are transmitted on two separate conductors. These conductors are called a differential pair. In a PCB, both traces are routed together with a constant space between them as edge-coupled or broadside-coupled as illustrated in Figure 4.
Figure 4. Various differential pair geometries. Edge-coupled microstrip (top left), edge-coupled stripline (bottom left) and broadside-coupled dual stripline (right).
Edge-coupled routes the traces side-by-side on the same layer as microstrip or stripline. The advantage is that any noise on the reference plane(s) is common to both traces and thus cancelled at the receiver. Most differential pairs are routed this way.
Broadside-coupled routes one trace exactly over the other on two separate layers as dual stripline. Since each trace is more tightly coupled to its adjacent reference plane than the opposite reference plane, any noise on the planes will not be common to both traces, and thus it will not be cancelled at the receiver. Because of this, and the fact that it usually results in a thicker PCB, this geometry is rarely used for highspeed design any more.
Odd-Mode Impedance
When a pair of traces is driven differentially, the mode of propagation is odd. If the spacing between the transmission lines is close, there will be electromagnetic coupling between the two traces. This coupling is defined by the mutual inductance and capacitance. Referring to Figure 5, consider a pair of equal width microstrip traces labeled 1 and 2, with a constant spacing between them. Each individual trace, when driven in isolation, will have a characteristic impedance Zo, defined by the self-loop inductance and self-capacitance of the trace with respect to the reference plane.
Figure 5. Differential microstrip showing the self and mutual inductance and capacitance.
The proximity of the traces to a reference plane influences the amount of electromagnetic coupling between traces. The closer the traces are to the reference plane, the lower the self-loop inductance and the stronger the self-capacitance. This results in a lower mutual inductance, and weaker mutual capacitance between traces. The end result is a lower differential impedance.
A 2D field solver is usually used to extract the parameters for a given geometry. Once the RLGC parameters are extracted, an L C matrix can be set up as follows:
For lossless transmission lines, the copper and dielectric losses represented by the R and G parameters are ignored.
The self-loop inductance and self-capacitance for traces 1 and 2 are L11, C11, L22, C22 respectively. The off diagonal terms in each matrix, L12, L21, C12, C21, are the mutual inductance and mutual capacitance. We can use the LC matrix to determine the odd-mode impedance, Zodd.
Zodd is the impedance of one trace of a differential pair when driven differentially. It can be calculated by the following equation:
Where:
Zodd = odd mode impedance
Lo = self-loop inductance = L11 = L22
Co = self-capacitance = C11= C22
Lm = mutual inductance = L12 = L21
Cm = mutual capacitance = |C12|=|C21|
Even-Mode Impedance
When current flows down both traces of the same polarity, the mode of propagation is even and the coupling is positive. The even-mode impedance, Zeven, can be calculated using the following equation:
Differential Impedance
The differential impedance, Zdiff, is simply twice the odd-mode impedance:
Zdiff = 2 x Zodd
Average Impedance
When current flows down two traces randomly, as if they were single-ended, the mode of propagation is a combination of odd and even. The average impedance of each trace is affected by its proximity to the adjacent trace(s). Zav is calculated by the following equation:
Coupling Coefficient
The coupling coefficient, Kcc, is a number that conveys the amount of electromagnetic coupling between two traces. Knowing the odd- and even-mode impedances, Kcc can be calculated by the following equation:
Backward Crosstalk Coefficient
If two traces are near one another, one will couple a portion of its own signal to the other. If we consider one trace as the aggressor, and the other as the victim, the amount of coupled noise travelling backwards on the victim’s trace, opposite to the aggressor’s direction, is called near-end crosstalk (NEXT) or backwards crosstalk. The amount of coupled noise, travelling in the same direction as the aggressor’s direction, is called far-end crosstalk (FEXT).
In stripline, there is little to no FEXT, but backwards crosstalk will saturate to a fraction of the amplitude of the aggressor’s voltage for the length of time the traces are coupled. This fraction of the aggressor’s voltage is called the backward crosstalk coupling coefficient Kb. It is equal to one half of the coupling coefficient Kcc :
Example:
An 8-9-8 mil differential pair; with 12 mil core; 12 mil prepreg; Dk=4; stripline geometry; 1/2 oz copper; has the following R L G C matrix extracted from a 2D field solver:
If the two traces are driven differentially, then the differential impedance is 100 ohms and there is 14% coupling of the two traces. On the other hand, if the traces are driven single-ended then the characteristic impedance of each trace is 57 ohms. With 9 mils of space between them, the backward crosstalk is 7%.
If you increase the spacing between traces until Zodd equals approximately Zeven, the coupling will reduce to near zero, and there will be little backward crosstalk. For this particular geometry, increasing the space to 50 mils gives Zodd = 61.5 ohms and Zeven = 61.7 ohms for Kb = 0.07 %.
Depending on your design and your noise budget, you may be able to live with a certain amount of backwards crosstalk. The only way to know the spacing between traces to achieve the budget is to plug in the numbers.
Acknowledgment
I would like to thank my old Nortel colleague Dick Goulette for sharing these equations many years ago. They have served me well over the years, and I hope you will find them just as useful the next time you define your PCB stackup.
Bert Simonovich was born in Hamilton, ON, Canada. He received his Electronic Engineering Technology diploma from Mohawk College of Applied Arts and Technology, Hamilton, ON, Canada in 1976. Over a 32-year career, working as an Electronic Engineering Technologist at Bell Northern Research and later Nortel, in Ottawa, Canada, he helped pioneer several advanced technology solutions into products. He has held a variety of engineering, research and development positions, eventually specializing in signal integrity and backplane architecture for the last 10 years. He is the founder of Lamsim Enterprises Inc., where he continues to provide innovative signal integrity and backplane solutions to clients as a consultant. With three patent applications and two patent grants to his name, he has also (co)authored several publications, including an award winning DesignCon2009 paper related to PCB via modeling. His current research interests include signal integrity, high-speed characterization, and modeling of high-speed serial links associated with backplane interconnects. To contact Bert, click here.
More Columns from Bert's Practical Design Notes
Practical Modeling of High-Speed Backplane ChannelsObsessing over Conductor Surface Roughness: What’s the Effect on Dk?
The PDN Bandini Mountain and Other Things I Didn’t Know I Didn’t Know
Bert's Practical Design Notes: Accelerating the SI Learning Curve - Bogatin's SI Academy
Bert's Practical Design Notes: Are Guard Traces Worth It?
Bert's Practical Design Notes: Perils of Lumped Via Modeling
Bert's Practical Design Notes: The "Stubinator" vs. Back-Drilling
Backplane High-Level Design: The Secret to Success