-
- News
- Books
Featured Books
- smt007 Magazine
Latest Issues
Current IssueSupply Chain Strategies
A successful brand is built on strong customer relationships—anchored by a well-orchestrated supply chain at its core. This month, we look at how managing your supply chain directly influences customer perception.
What's Your Sweet Spot?
Are you in a niche that’s growing or shrinking? Is it time to reassess and refocus? We spotlight companies thriving by redefining or reinforcing their niche. What are their insights?
Moving Forward With Confidence
In this issue, we focus on sales and quoting, workforce training, new IPC leadership in the U.S. and Canada, the effects of tariffs, CFX standards, and much more—all designed to provide perspective as you move through the cloud bank of today's shifting economic market.
- Articles
- Columns
- Links
- Media kit
||| MENU - smt007 Magazine
Estimated reading time: 1 minute
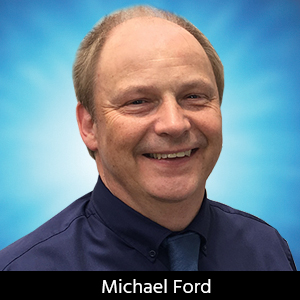
Contact Columnist Form
The Essential Pioneer's Survival Guide: Dropping the BOM
The bill of materials (BOM) is the most critical element in the definition of what production should do to manufacture a product. What ends up executing as a BOM on the shop floor, however, is the result of several complex and often manual processes, some of which will corrupt the BOM’s data integrity. Who takes responsibility for what is actually produced as compared to what the design intended? Getting a real handle on the management of the BOM must be high on the agenda for any company as product mix and variation grows, lead times to market decrease, and the need for accountability increases.
The BOM starts life at the design stage. As products are conceived, often formed around combinations of key technologies and chipsets, the key materials are identified. These key materials are at the core of the design. For the electrical designer, the specifications are known in terms of functionality, and for the layout designer, in terms of physical attributes. These materials are usually sourced from only one or two suppliers, and are not interchangeable with other devices. The majority of the remaining materials that will make up the product are so-called “common” materials: things like resistors, capacitors, diodes, etc., which have standardized specifications, are available from several different suppliers and in several different specifications of size and rating. Generally, the electrical designer decides the values and ratings of all materials, the design capturing these as well as the descriptions of the key materials. The layout engineer takes this information and has to make decisions about which actual materials to use, at least in terms of size and shape. Each individual component is uniquely named with a reference designator, a shape, a specified value and rating, and often, an assigned nominal part number.Read the full column here.Editor's Note: This column originally appeared in the August 2013 issue of SMT Magazine.
More Columns from The Essential Pioneer's Survival Guide
If It's My Data, I Can Do What I Want, Right?The Essential Pioneer's Survival Guide: One Size Fits All?
Smart for Smart’s Sake, Part 3: Unification & Traceability
Smart for Smart's Sake, Part 2: Material Management
The 'New Face' of Automotive Traceability
Industry 4.0: Who Benefits?
To Be Lean is to Be Human
Stop the SMT Conspiracy, Part 2: Abduction