-
- News
- Books
Featured Books
- smt007 Magazine
Latest Issues
Current IssueSupply Chain Strategies
A successful brand is built on strong customer relationships—anchored by a well-orchestrated supply chain at its core. This month, we look at how managing your supply chain directly influences customer perception.
What's Your Sweet Spot?
Are you in a niche that’s growing or shrinking? Is it time to reassess and refocus? We spotlight companies thriving by redefining or reinforcing their niche. What are their insights?
Moving Forward With Confidence
In this issue, we focus on sales and quoting, workforce training, new IPC leadership in the U.S. and Canada, the effects of tariffs, CFX standards, and much more—all designed to provide perspective as you move through the cloud bank of today's shifting economic market.
- Articles
- Columns
- Links
- Media kit
||| MENU - smt007 Magazine
Estimated reading time: 7 minutes
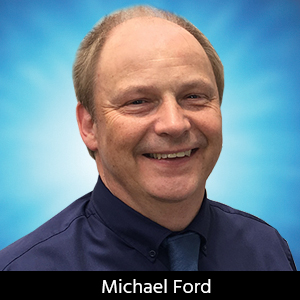
Contact Columnist Form
Stop the SMT Conspiracy, Part 2: Abduction
As I mentioned in Part 1 of this series (October 2014), tours of SMT factories sometimes make me feel like I am in an episode of The XFiles. In Part 1, we focused on information about processes that were often out of this world, so to speak. This time, we focus on a case of abduction.
Abduction
The story starts with the reported disappearance of some key materials from the shop floor. One minute they were there, and the next, they could not be found. Rumors were started and fingers were pointed. The evidence triggered stories of strange events that sometimes took place during the night, when no one was around. CCTV was setup; footage was analyzed and cages were built to protect higher-value materials, but still, the strange disappearance of materials continued.
Time once again for Mulder and Scully to investigate. Was the disappearance caused by some alien visitation, or had an enterprising engineer simply built a teleportation device out of spare parts? The truth had to be uncovered—a task that was to become something much more complex than anyone was expecting.
The victim in this instance was quickly identified as we entered the senior manager’s meeting room. Charts were displayed; groups of managers sat huddled over tablets. As we sat down, the CEO called the meeting to order. We were taken through a sequence of reports that showed that materials had been ordered by MRP, arrived, booked in, but had then never left the factory—at least not officially.
All available staff had been called on to work through the previous weekend, performing a site-wide stock check, counting all of the raw materials in the factory. The expected result had been a subtle material discrepancy between the ERP stock records and the physical inventory that could be explained by the nature of the production operation. The shocking reality, however, was an inventory inaccuracy level approaching 30%, or 10x what had been expected.
The financial team figured that the loss represented more than $3 million worth of materials at cost pricing. That’s a lot of chips.
The Scale of the Problem
OEM manufacturing operations are budgeted to break even against an agreed budget, using fabricated “transfer pricing” as a tool to calculate operational performance. On the other hand, EMS companies need to make real profits, often from very small margins. A sudden impact on the business in either case can be devastating.
Shutdown of the factory over a long weekend had already meant the loss of 1% of annual productivity. For a factory making products with a total value of $150 million per year, the stock check cost $1.5 million of lost opportunity, even before considering the labor and other costs. The end-result value of the write-off of “lost” materials was estimated at more than $3 million on top. This would represent a major embarrassment for any OEM CEO and a financial disaster for an EMS, whose margin just evaporated. It was time to get out of the meeting and into action, to uncover the facts about the conspiracy behind these SMT materials shortages.
The Scene of the Crime—the Warehouse
An anxious warehouse and logistics manager approached us. He was quick to explain that, although the materials shortages had reported been directly related to his team, all of the losses actually could not have taken place in the warehouse. He was confident in his materials operators. He thought that the materials had gone missing because of the inherent nature of SMT materials, which, while mostly based on reels, have a minimum delivery quantity. He explained that for work orders that require 1,500 pieces of a certain material, the minimum he can send to production is a single reel of 5,000. Even if he had a reel with 1,500 pieces of materials, a little extra would have been needed to compensate for the SMT machine and related spoilage, so more materials would have had to be included. This issue applied to each of the hundreds of materials on every work order, multiplied then by the number of production lines. Not only that, but because of the history of not being able to find materials for work orders when needed, each line can have several such “kits” of materials prepared in advance, meaning that if there was a material shortage at the warehouse, there should be time to do something about it before it affected production. This was the agreement that production made with the warehouse.
I thought that we had just found a clue to our conspiracy. The warehouse was huge and well-stocked with materials. It must have taken ages to count. The bloated inventory was simply due to the requirement to oversupply the lines and the historical issues of unexpected material shortages. The increase in the frequency of these shortages was what led to the need for the stock check.
The warehouse manager shrugged his shoulders and said he knows what happens during the day; it is what happens at night that he is afraid of. I asked whether the excess materials sent out to production are ever seen back in the warehouse again. The reply was that they were not—at least not all. The ERP system had difficulty tracking part-used materials, so manual management was necessary within production.
We looked across the shop floor at the banks of feeder trolleys and racks of feeders, all setup with part-used materials. With each feeder costing up to $1,000, that was a serious investment in itself. What was causing the disappearance of those materials? It was time to move on and talk with the production manager.
What Happens in Production, Stays in Production
The production manager openly admitted that his priority is to keep the production lines working at all times because that was the core of the value generation of the business. He and the warehouse manager agreed that oversupply is essentially insurance against material supply issues causing production downtime. It was thought of as a trade-off; after all, neither the warehouse manager nor any of his guys wanted to work the night shifts. Chuckling, the production manager left us momentarily to order us some coffee.
While the manager is momentarily absent, a young production engineer turned informant. He said that often the materials prepared in the warehouse kits are not enough. At night, with the machines on stop, machine operators have to go looking for materials and will take whatever they can find, which includes taking materials from the warehouse.
The production manager returned. I asked what happens to the oversupplied materials. The production manager and the engineer exchanged glances. We are told that the partly used materials should be returned to the warehouse, but with the time and effort needed for counting, this only happens for expensive key materials, and only then if there is a significant quantity. Production generally keeps materials on the shop floor to cope with cases where the warehouse undersupplies or there is a sudden spoilage issue. The undersupply happens if the warehouse manager thinks that there should be enough excess materials already issued in earlier kits that should be reused. He often gets it wrong, or at least he often cannot find it.
The spoilage issue, while averaging out as a fraction of a percentage of materials overall, can suddenly peak if reels are loaded and unloaded onto feeders several times, if the feeders have been set up incorrectly, or the material itself becomes damaged. In those cases, with the warehouse working so far in advance of production, it is up to production to manage replacements. The ERP system cannot account for materials on the shop floor, so, as the production manager explained, they take control. I suspect, however, that this is not always their highest priority. There are thousands of reels and trays of materials, stacked up on unlabelled shelves, all mixed, some on feeders, and some not. I am not surprised that materials would be difficult to find, such that in a line-down situation, it may be far easier to look in the warehouse.
The volatile nature of material spoilage around the SMT machines seems to account for some of the material losses, but surely not all. Having such bloated inventory in the warehouse and a huge quantity of unmanaged materials on the shop floor would indeed make it very difficult to identify when or where problems began and things went out of control. It was time to talk with the engineering manager, who, for some reason, was not surprised to see us.
Editor's Note: This article originally appeared in the February issue of SMT Magazine.
More Columns from The Essential Pioneer's Survival Guide
If It's My Data, I Can Do What I Want, Right?The Essential Pioneer's Survival Guide: One Size Fits All?
Smart for Smart’s Sake, Part 3: Unification & Traceability
Smart for Smart's Sake, Part 2: Material Management
The 'New Face' of Automotive Traceability
Industry 4.0: Who Benefits?
To Be Lean is to Be Human
The Future of SMT: Welcome to the 4th Dimension