-
- News
- Books
Featured Books
- smt007 Magazine
Latest Issues
Current IssueSupply Chain Strategies
A successful brand is built on strong customer relationships—anchored by a well-orchestrated supply chain at its core. This month, we look at how managing your supply chain directly influences customer perception.
What's Your Sweet Spot?
Are you in a niche that’s growing or shrinking? Is it time to reassess and refocus? We spotlight companies thriving by redefining or reinforcing their niche. What are their insights?
Moving Forward With Confidence
In this issue, we focus on sales and quoting, workforce training, new IPC leadership in the U.S. and Canada, the effects of tariffs, CFX standards, and much more—all designed to provide perspective as you move through the cloud bank of today's shifting economic market.
- Articles
- Columns
- Links
- Media kit
||| MENU - smt007 Magazine
Estimated reading time: 12 minutes
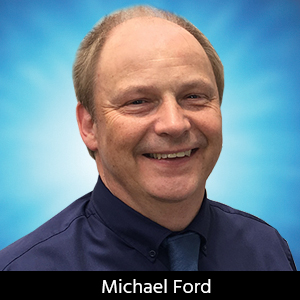
Contact Columnist Form
The 'New Face' of Automotive Traceability
Historically, the perception of traceability data collection from the shop-floor has been that it presents a significant burden to the operation, yet provides value only when the most unplanned, rare, and disastrous of events take place. Automotive has always been on the forefront of traceability because safety issues are paramount, and responsibilities for failures are quite severe.
A quiet revolution, however, is taking place within the automotive electronics industry, driven by a collection of technology advances, the need for further energy efficiency, and ever enhanced safety. A wide combination of different products that previously only existed in discrete sectors have come together in the car, combining critical control and management systems, including self-drive technologies such as radar, multi-media consumer devices, and built-in telecom capabilities including Internet access.
All of these technologies have to work together in one extended system, all operating in potentially hostile environments, and yet also be economically competitive because the car is, after all, a key consumer product. This is what makes automotive unique. A glitch in a single video camera does not simply result in a poor quality picture, it may now cause a car’s systems to react inappropriately in certain situations. Every electronics-based system can potentially affect every other.
A new approach to automotive traceability that brings the whole principle of traceability in electronics manufacturing up to date is now long overdue.This new “face” of traceability has a low cost of ownership because almost all data is captured electronically and automatically from every process and support operation within the factory. Assurance and compliance is enforced as operations are optimized and guided by the relevant elements of the highly automated manufacturing control software, with traceability built-in. Depending on the level of detail, accuracy, and timeliness of data capture from areas such as quality management, manufacturing, engineering, and supply chain, traceability can become the ultimate quality-management tool, as well as bring enhanced productivity and reduced operating costs.
The Cost of Compliance
Traceability data collection has been all about recordkeeping: the list of materials used, the processes executed, exceptions that have happened during, for example, test processes. In what we can call the traditional automotive factory, the majority of processes were separate entities each supported by other disconnected functions. For example, SMT machines pick from materials that have been loaded. The machines only need to know the size and shape of materials to operate.
The setup of the materials on the SMT machines, which has to align to the setup that is expected by the SMT machine program, is still in most cases done manually as a separate process. And even the introduction of “smart” feeders on SMT machines that can transfer knowledge of loaded material content from the feeders to the machine automatically serves only to push the point of materials setup and verification away from the machine to the material setup area, where mistakes can still happen.
Another mechanism, driven by supply chain, provides logistic support to bring the required materials to the kitting area, which usually is in bulk as a kit, and requires significant manual management. The selection of those materials from the warehouse is also likely to be done by a separate entity, which in many cases still relies on manual decision-making. The receipt and put-away of materials into the warehouse storage locations was also required, often again, by a separate operation.
No wonder then that the cost of traceability information recording at key production processes is just the tip of the iceberg when it comes to “needless” operational costs incurred by tasks associated with compliance to standards for automotive manufacturing assurance.
Improved use of Existing Data and Systems
The starting point for the “new face” of traceability follows the realization that pretty much all of the necessary traceability data already exists as part of the production operation, and so as such, the record-keeping activities were actually needless duplications of existing data. Most production processes today and the systems that support them are now automated to a greater or lesser extent.
The SMT machines are a great example. Surely every SMT machine must know exactly what material is being taken from which feeder and placed on the PCB for each reference designator because it is part of the SMT machine program. This is the origin of exact traceability. It is a critical part of the overall PCB traceability solution because it reflects the point-of-use accurately, for example, alternative or substitute materials, cases where there are multiple instances of the same material part number on set up on the machine that could be selected for use at any time, or perhaps a material is changed at a position part-way through a circuit board.
It is only right at the actual point of use and consumption that the exact traceability data can be derived; and for automotive, most materials are placed as SMT. Although the SMT machines have knowledge of this relationship of feeder and placement, it is the first critical piece of information, in addition to which other key information will need to be added.
Typical modern SMT machines will recognize materials by their part number and not recognize their unique characteristics such as manufacturer, batch number, age, MSD status, and history, etc. Therefore, the “point-of-use” traceability data coming from the machine has to be qualified against the information of the specific materials used. This material information can be acquired and associated to each material carrier using a unique ID as it is received in the SMT material warehouse. When these two pieces of information are known, there is then the need for the link to know which material IDs have been set up and used at each feeder position.
Rather than leaving this as a manual process, our “new face” of traceability can instead use further automation. Using the material consumption data coming from the machine, a “low level warning” can be created, which in combination with the work-order planning data can be made into a pull signal to trigger just-in-time (JIT) material replenishment to the warehouse. Knowing exactly what material is needed, where, and when, Lean supply-chain logistics software can select the best material available from the warehouse and send it directly to the required position on the SMT machine so that it arrives immediately before it’s needed. In so doing, the traceability data of the materials is linked with that of the machine, connected by the software-driven verification process of the material on to the feeder.
Three Benefits of Automated Traceability
The live data coming from the SMT machines, associating picked materials with placements, would now be used to generate three benefits for manufacturing. The first is the automated creation of exact traceability data without manual effort or mistake, as well as the elimination of kitting errors. The second benefit is the use of Lean materials logistics, which eliminates significant stocks of materials on the shop-floor, reducing needless investment cost as well as space and handling overheads. Thirdly, the assurance that the production is being executed exactly as specified. The automotive management conformance requirements have been satisfied through the material verification process, which does not allow any machine to work unless every material has been actively verified for use only in its set position.
Figure 1: Full automation carries through all the necessary manufacturing data to comply with automotive management reporting requirements.
Three separate benefits have been achieved simply and automatically through the capture and use of one key source of data, bringing lower cost and inter-process automation between the supply-chain to manufacturing flow. Similar mechanisms exist to support non-SMT machines for manual assembly and even for repair, as well as the bare PCB and consumable items such as solder paste, all with active verification, pull material signals, and the subsequent automated association of data to create material traceability.
These additional steps, although usually representing a small fraction of the total material content of a PCB, are essential to have a complete material traceability record and to eliminate operational mistakes, as well as reducing the operational costs. It all sounds too good to be true, but these are firm principles of advanced automation of interconnected processes as suggested by Industry 4.0—applied to traceability.
Benefits Extending Beyond Materials Traceability
Material traceability is just one part of the overall traceability requirement for automotive. The need for control and tracking of PCB assemblies through SMT and related operations, from a traceability perspective, is originally centered on the test and repair process. The basic requirement was the assurance that each product had passed every required test. This immediately introduced the requirement that each individual PCB within a work-order needs to be managed separately.
In the traditional manufacturing flow, a failed test would mean that a paper-based repair ticket was issued, which would be physically attached in some way to the failed PCB which was then taken to the repair station. The critical issue was simply that the repair tickets would fall off, leaving a failed PCB that could mistakenly go forward in production without being repaired. This can be solved by creating a unique identification of each PCB that is associated with a bare PCB as early as possible in the process.
The history of labeling PCB IDs has been fraught with issues with little available space for a barcode, especially considering the need for consistent positioning across products. Newer generation scanners, etching machines, and 2D barcode technologies have all combined to ease the cost and improve the reliability.
With the unique PCB ID in place, a whole range of potential values are created. At each testing process, the test result and associated test data can be captured electronically and automatically, then associated with the individual PCB. In the case of a test failure, the captured data acts as a paperless repair ticket. Reading the PCB ID at any point can display the history and status of each individual PCB.
At the repair station, reading the PCB ID provides not only the repair ticket information, but also the complete manufacturing and history, including any previous failures and repair attempts. Serious quality issues and trends in quality can be identified and highlighted in near real-time, providing the opportunity for active quality management. Should any PCB be routed incorrectly, then the next process with a reader for tracking will prevent processing of the faulty unit, thereby ensuring that no defective PCB assemblies can get through to the next stage.
This tracking facility can also be used to ensure that during manufacturing all process are completed in the correct sequence and that all processes are set up correctly before execution can begin. In cases where processes are capable of making different products with the same material setup, the unique PCB ID can also be used to trigger the SMT machine to select the correct machine program, thus allowing mixed production through SMT machine lines without risk of error.
Using the same tracking information, the time taken by each PCB assembly at each process and the time lost between processes can be recorded, which can then be used in productivity reports and bottleneck analysis. This provides a great deal more depth than only capturing data about the quantities of products produced and stored. All of this information, automatically captured by the tracking system, is then available to be a part of the traceability data.
The justification for unique PCB identification can be made based not only on routing at test and repair, but also for complete material and process traceability where exact trace of materials to individual PCBs as well as product manufacturing and test histories are required.
Adopting the three key principles of the “new face” of traceability creates a whole new paradigm of technology that is based on the creation of value and benefit to manufacturing. The ability to collect all of the required data for traceability through the use of automation means that there is little cost for the data acquisition. The data is also more accurate because there will not have been manual data entry or data manipulation, and it will also be more immediate because it is collected from the processes during the normal course of operation. The data collected can also potentially be far more detailed than when using manual methods because there is very little overhead on how much data can be collected.
This all leads to a rich traceability environment for little cost. The key for automated traceability value is focused on combining all of the different sources and formats of data, piecing together every fact and event that happens.
Care should be taken for accurate interpretation of the data so that traceability is built into a neutral format that is not dependent on any proprietary formats from machines or processes. Traceability retention for automotive electronics systems can stretch to many years, sometimes over a decade, which means the sheer volume of the data can require the adoption of the latest “big data” technologies.
Even this requirement for the retention of traceability data can provide more benefit than cost. Apart from the headline-grabbing, market-recall scenarios, bringing the need for immediate help to identify the exact scope of vehicles with a particular issue so as to reduce recall costs, traceability data can serve as a sophisticated internal and market-quality tool.
Figure 2: Total traceability pulls data from all three silos of materials, process, and quality.
Because of the nature of production with traceability, there will be very few issues in the market, but if any issue, even a minor one-off defect should be found, possible root causes can be found with the significant options for analysis of the complete build records for those products. For example, the defect could be found in a product that was one of a 1,000 unit work-order, which were all made at the same time and in the same way.
There has to be a reason, however, that one of those products out of the 1,000 had a variance—a slightly different circumstance or combination of circumstances that created this defect. Using the fully detailed traceability build record, covering all processes and materials including all sub-assemblies, it is far more likely that the specific exception that may have occurred, such as a specific combination in the use of alternative materials, deviation of the reflow process temperature, or a particular repair that was actioned, could have been the unique trigger to cause the defect.
Once known, the specific set of circumstances can be engineered out of the production operation so as to prevent the defect from recurring. Without traceability, finding the root cause would have been almost impossible.
The approach to the need for traceability in today’s automotive manufacturing environment should no longer be a simple reaction to what is required by a customer to meet some specified standard, especially where products with complex use categories are made together. The real traceability solution lies with the full consideration of the ability of key processes such as SMT and key supporting functions such as supply chain, engineering, production management, and quality to communicate in automated ways, sharing data that can be made visible and used to obtain multiple operational benefits, and as a result, a complete and detailed traceability record. Doing this should make adherence to any standard imposed from the customer something that becomes just a routine “tick in the box,” because everything is covered as a fundamental part of the production operation, in a way that is a benefit, rather than being a potentially costly add-on control and management function.
More Columns from The Essential Pioneer's Survival Guide
If It's My Data, I Can Do What I Want, Right?The Essential Pioneer's Survival Guide: One Size Fits All?
Smart for Smart’s Sake, Part 3: Unification & Traceability
Smart for Smart's Sake, Part 2: Material Management
Industry 4.0: Who Benefits?
To Be Lean is to Be Human
Stop the SMT Conspiracy, Part 2: Abduction
The Future of SMT: Welcome to the 4th Dimension