-
-
News
News Highlights
- Books
Featured Books
- pcb007 Magazine
Latest Issues
Current IssueSales: From Pitch to PO
From the first cold call to finally receiving that first purchase order, the July PCB007 Magazine breaks down some critical parts of the sales stack. To up your sales game, read on!
The Hole Truth: Via Integrity in an HDI World
From the drilled hole to registration across multiple sequential lamination cycles, to the quality of your copper plating, via reliability in an HDI world is becoming an ever-greater challenge. This month we look at “The Hole Truth,” from creating the “perfect” via to how you can assure via quality and reliability, the first time, every time.
In Pursuit of Perfection: Defect Reduction
For bare PCB board fabrication, defect reduction is a critical aspect of a company's bottom line profitability. In this issue, we examine how imaging, etching, and plating processes can provide information and insight into reducing defects and increasing yields.
- Articles
- Columns
- Links
- Media kit
||| MENU - pcb007 Magazine
Estimated reading time: 5 minutes
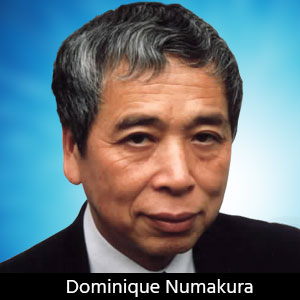
EPTE Newsletter: 47th INTERNEPCON JAPAN
The 47th INTERNEPCON Japan electronics trade show was held on January 18th at Tokyo Big Sight. I attended the three-day NEPCON show in hopes of discovering the next electronics breakthrough, and examine the business trends within a shrinking electronics industry. The show attracted a large number of visitors—150,000 people over the three days. It was tough navigating between the trade show booths because the aisles were full with people.
It is now common to have relating exhibitions held concurrently. For this reason, the exhibition gets bigger each year. Listed below are the events that were held simultaneously:
- 34th ELECTROTEST JAPAN
- 9th Light-Tech Expo
- 18th PWB EXPO (Printed Wiring Boards Expo)
- 18th IC PACKAGING TECHNOLOGY EXPO
- 18th ELECTRONIC COMPONENTS & MATERIAL EXPO
- 7th FINE PROCESS TECHNOLOGY EXPO
- 3rd WEARABLE EXPO (Wearable Device & Technology Expo)
- 1st RoboDex (Robot Development & Application EXPO)
- 9th CAR-ELE JAPAN (Int’l Automotive Electronics Technology Expo)
- 8th EV Japan (EV & HEV Drive System Technology Expo)
- 7th Automobile Lightweight Technology Expo
- 5th Connected Car Japan
- 3rd CAR-MECHA JAPAN (Automotive Components & Processing Technology Expo)
- 1st SMART FACTORY Expo
More than 2200 companies and organizations reserved booths. The East Hall expanded the floor space 30% this year to accommodate the new exhibitors. Due to the size of the exhibition, I was not able to review the entire show. In my opinion, the promoter should focus on visitor engagement, and not the head count at the gate.
A big change this year was the increased size reserved for the automobile vendors. More than half the floor space was dedicated to car electronics or related products. Consumer electronics companies will target the automobile industry during recessionary periods because the automobile industry is more stable than the consumer electronics industry. However, the automobile industry in Japan is more conservative than the consumer industry; therefore, it takes time and money before the sales pitches bear any fruit. Most of these companies will stop peddling to the auto industry once their traditional businesses begin to flow again. Unfortunately, the current recession for consumer electronics is very long, and the Japanese electronics companies have few customer choices other than automobile market. I focused my attention on traditional electronics packaging at the show.
The PWB section of the show was smaller this year. Many of the major circuit manufacturers did not reserve booths. Several mid-sized manufacturers introduced upgraded technologies such as 100+ layer counts and MIL certified rigid-flex. FiWLCSP and FoWLCSP are the common technology for IC substrate suppliers. The manufacturers developed finer than 10 micron traces. Specialty chemical suppliers featured competitive solutions for the semi-additive process capable of producing 2-micron traces. I came across several new circuit manufacturers from Taiwan, Mainland China and other Asian countries. Usually, their technology and quality levels were subpar compared with Japanese manufacturers; however, they are just as good today.
Wearable technology is popular and will continue to be popular in the electronics industry. Flex circuit manufacturers featured new technical concepts for stretchable circuits and transparent circuits using new substrate and conductor materials. Textile manufacturers introduced new functional fibers for use as the basic material for wearable electronics. Their demonstrations did garner a lot of attention, but the ideas for application abled products is still in its infancy, and make take a few more years to commercialize.
Companies affiliated with assembling sections were present at the show. Manufacturers for mounting machines and soldering occupied relatively large spaces, but there were fewer companies compared with last year’s show, and most of were headquartered in Japan. I was not very sure if these Japanese manufacturers are growing their market share, but I do know that foreign suppliers do not have strong representation in this market. EMS manufacturers had one company headquartered in Japan. They were happy to report their revenue topped over $1 billion due to expansions in China, Vietnam and Mexico.
Looking at the whole exhibition, I can see that business for the consumer electronics industry in Japan remains sluggish. Many electronics companies are still shaking the bushes looking for new business, especially from the automobile market. It may take some time to get this well primed, but once it does, they will benefit from increased business. I remain optimistic.
Headlines of the week
1. Murata (Major component supplier in Japan) 1/12
Has developed a new heat resistant ceramic capacitor series RHS for modules in engine rooms. It is available at 200°C.
2. Panasonic (Major electronics company in Japan) 1/17
Has commercialized a new low-loss thin flexible laminate for multi-layer flexible circuits. The bonding sheets can be kept under room temperature.
3. AGC Asahi Glass (Major glass supplier in Japan) 1/17
Has developed a new glass sheet with low CTE for the fan out wafer level package of the next-generation semiconductor devices.
4. Ube Eximo (Polyimide material supplier in Japan) 1/17
Has started volume production of the new polyimide laminate “Upicel H” with thick copper foil for flex circuits in automobile use.
5. Idemitsu (Major petro chemical company in Japan) 1/18
Has founded a new subsidiary in Switzerland for R&D work of organic EL materials cooperating with BASF.
6. Hitachi Solutions (Equipment supplier in Japan) 1/19
Has rolled out a new voice recognition and management system for the telephone monitoring in finance companies.
7. Omron (Major device manufacturer in Japan) 1/19
Has opened a new automation center in Seoul, Korea, for the customer service of the factory automation devices.
8. Sharp (Subsidiary of Hon Hai Precision in Taiwan) 1/20
Has opened a new R&D center in Shenzhen, China for white goods and home appliances. It will cover southeastern Asia.
9. Panasonic (Major electronics company in Japan) 1/23
Has commercialized a new lighting system LINK STYLE LED. It manages the lighting in the rooms by Bluetooth.
10. Air Water (Gas supplier in Japan) 1/24
Has started a field test of Shikaoi Hydrogen Firm. Hydrogen gas is generated from biomass materials and supplied to the area.
11. AIST (Major R&D organization in Japan) 1/26
Has developed a new simple process to generate pure nano-carbon thin layers on various substrates including glass and rubber using appropriate lighting.
12. Nippon Paper (Major paper supplier in Japan) 1/30
Has developed a new hybrid material of pulp cellulose and inorganic compounds named Mineral Hybrid Fiber.
13. Hitachi High Technologies (Equipment manufacturer in Japan) 1/30
Has co-developed a new equipment to generate thin layers with Plasma-Enhanced Atomic Layer Deposition with Kustaa Poutiainen in Finland.
14. Panasonic (Major electronics company in Japan) 1/31
Will found a new subsidiary, Panasonic Eco Solutions Solar New York America for manufacturing and marketing photovoltaic modules.
15. Konica-Minolta (Major camera manufacturer in Japan) 1/31
Has agreed to make a joint venture with Pioneer to create organic EL lighting business, especially in automobiles.
16. Toyota Motors (The largest automobile manufacturer in Japan) 1/31
Has started to operate new forklifts powered by fuel cells in Motomachi Plant in Aichi Prefecture.
To read back issues of the newsletter, click here.
To reach Dominique K. Numakura, click here.
Visit DKN Research at www.dknresearchllc.com.
More Columns from EPTE Newsletter
EPTE Newsletter: Travel to Japan During COVIDEPTE Newsletter: A New COVID Surge in Taiwan?
EPTE Newsletter: COVID-19 PCR Test in Japan
EPTE Newsletter: Japan Failing in Vaccine Distribution
EPTE Newsletter: A Long Trip to the U.S.
EPTE Newsletter: Ten Years After Fukushima
EPTE Newsletter: Taiwan Releases 2020 PCB Production Numbers
EPTE Newsletter: The Printed Circuit Industry in China