-
- News
- Books
Featured Books
- pcb007 Magazine
Latest Issues
Current IssueInventing the Future with SEL
Two years after launching its state-of-the-art PCB facility, SEL shares lessons in vision, execution, and innovation, plus insights from industry icons and technology leaders shaping the future of PCB fabrication.
Sales: From Pitch to PO
From the first cold call to finally receiving that first purchase order, the July PCB007 Magazine breaks down some critical parts of the sales stack. To up your sales game, read on!
The Hole Truth: Via Integrity in an HDI World
From the drilled hole to registration across multiple sequential lamination cycles, to the quality of your copper plating, via reliability in an HDI world is becoming an ever-greater challenge. This month we look at “The Hole Truth,” from creating the “perfect” via to how you can assure via quality and reliability, the first time, every time.
- Articles
- Columns
- Links
- Media kit
||| MENU - pcb007 Magazine
Estimated reading time: 7 minutes
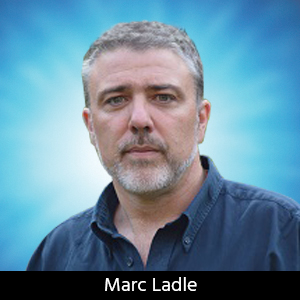
Testing Times Ahead
Bare board electrical test: For the most part, it does what it says on the tin. Current CAM software and test hardware means that in theory, it is a pretty simple exercise to make sure that a printed circuit matches the intended design. But are you getting the test you think you are?
Of the many different manufacturers of test machines, there are only two basic test methods: bed of nails or flying probe. Bed of nails test uses a fixture which is bespoke to the circuit design, so you must invest some effort into building the test jig and loading it with test pins. This can be quite a lot of work—especially for high-density circuit designs. I have built individual fixtures in the past with more than 5,000 test pins. For obvious reasons, this approach is better suited to larger batch sizes. Flying probe test needs no test fixture so it is no problem to test a single circuit. The test probes move from point to point on the circuit, testing each of the networks as they go.
The choice of which test method to use usually comes down to batch size and the likelihood of repeat batches. Many factories in Europe only use flying probe test. It certainly simplifies the choices that need to be made. There are no time-consuming fixtures to be assembled and flexibility in the test department is always good as change-over times are quick.
For a bed of nails test, investment is upfront most of the time; before you can start to test, the fixture must be designed and built, and even after you load it to the test machine there is often some debug to complete to make sure there are no missing, damaged or sticky test pins. Once you are running, the test is very quick—often just a few seconds for each circuit—which may take several minutes to test on a flying probe.
Modern test preparation software is very good at creating a secure netlist for test. This is the map that tells the tester which points should be connected and which points should not. You load the circuit design into the software and select the test method you want to use and the software will output the required files to enable you to make a test fixture or run a flying probe test.
The capability of each test method is not the same. This is the part that I thought may be of most interest to people who have not had experience using both types of tester. Current test requirements can be very demanding and quite difficult to comply with if you do not have the right hardware. A printed circuit design will often need to be manufactured to meet a formal standard, for instance IPC class 1, 2 or 3. The IPC documents give a good level of detail to tell you how you should set the tester. For the test department, it can be problematic that there is not a one-size-fits-all approach that you can use for all designs.
The following are some examples to give you some idea of possible issues.
Voltage
The available test voltage can be different from machine to machine. When testing for continuity, the voltage is usually just a few volts and a very small current. Very little power is applied during this part of the test. When testing isolation between networks, the voltage is often much higher. Some flying probes can be specified with 500V or 1000V isolation voltage capability. Bed of nails test may use much lower voltages for isolation testing.
Resistance
On all testers, an acceptable pass/fail value must be set for both continuity and isolation resistances. In fact, resistance could probably be the main control parameter for electrical test. Capability varies massively. For continuity test, most testers can be set with Ohm values in single figures. More capable testers make mOhm values possible by using a Kelvin (4-wire) test method. For isolation test, some testers are limited to values of a few KOhms; high-end flying probes may be capable of one GOhm or more.
Capacitance
Flying probes often speed up the test by using a capacitance-based measurement to detect open or short circuits. It is faster because there is no need to touch both ends of a network at the same moment. Thus, a much more efficient path can be selected for each of the probe heads. If a tester has four probe units, one can be used to touch the base network for capacitance measurement and the other three probes can check the test values of different networks at the same time. Capacitance-based test can be four or five times as fast as a resistance-based test. The capacitance measurement can be affected by blunt probe tips and poor conductive surfaces, so it is particularly dependent on good maintenance and servicing of the test machine.
If a test department has more than one type of tester, there is no guarantee that the same tester will always be used to test a particular circuit design. This could mean that one batch is tested on bed of nails and the next is tested by flying probe, so the test parameters can be very different from batch to batch.
Where a design does not call for a particular level of test default, test parameters will probably be used. These can vary quite a lot between different PCB manufacturers. Where a department has both bed of nails and probe testers, available parameters may be set which are achievable on both types of test. Often a continuity value of 50−80 Ohms is selected and an isolation value at the top end of the bed of nails capability. What you should catch for certain are true open and short circuits. There is really no excuse for any test method to miss this type of fault.
Where it gets more difficult is if the isolation fault has a high resistance or if there is a slight manufacturing flaw in the copper circuit. To accurately test for these types of faults, it is much more important to understand the limitations of the test method you are using. Older bed of nails testers may not be good for finding high resistances. Capacitance-based test should not be used to detect this type of fault so flying probes need to be set to a slower resistance-based test if you want to have the best chance of detecting this type of problem.
Testing of manufacturing flaws is harder still. Typical of this type of fault are defects in the metallisation of drilled holes which may only become apparent when the circuit has been put through several thermal cycles. To detect this type of flaw at the bare board test stage is very tough. A via hole may have a side to side resistance of just a few mOhms and a copper plating defect at this stage may only change the resistance by part of a mOhm. It is possible to measure this difference by making a very high accuracy test of the resistance of each hole from both sides and then looking for the ones that have the slightly higher values. You may be looking for one bad hole in a million. As far as I know, this can only be done with a high-end flying probe tester and it is a time-consuming test. It must be done in addition to the normal electrical test program which tests the rest of the circuit pattern.
If used correctly, modern testers are capable of many advanced functions. Both bed of nails and flying probes have developed a long way in the last few years. Voltage withstand test, buried resistance test and test of other embedded components, impedance test, even latent test has been tried to enhance the overall capability of equipment.
If you are concerned that you are missing faults or unable to achieve the test parameters you are being asked to meet, speak to your test machine supplier about an update of the machinery or trading in for a more capable machine.
The good news is that modern test equipment is hugely capable. There is most likely to be a machine out there which has the features and parameter range you are looking for. You may even find that the equipment you already own is up to the task if it is set correctly.
More Columns from Ladle on Manufacturing
Ladle on Manufacturing: LED UV Cure—Does It Really Work?Ladle on Manufacturing: UV Cure LED Energy Saver
Ladle on Manufacturing: Sharing an Idea for Christmas
Ladle on Manufacturing: Behind the Scenes at productronica 2019
Ladle on Manufacturing: Sunday Afternoon in Dongguan
The Travelling Engineer, Installment 2
Ladle on Manufacturing: VCP—The Future of Plating
Developments in Wet Processing: Beyond Spraying and Dipping