-
- News
- Books
Featured Books
- pcb007 Magazine
Latest Issues
Current IssueInventing the Future with SEL
Two years after launching its state-of-the-art PCB facility, SEL shares lessons in vision, execution, and innovation, plus insights from industry icons and technology leaders shaping the future of PCB fabrication.
Sales: From Pitch to PO
From the first cold call to finally receiving that first purchase order, the July PCB007 Magazine breaks down some critical parts of the sales stack. To up your sales game, read on!
The Hole Truth: Via Integrity in an HDI World
From the drilled hole to registration across multiple sequential lamination cycles, to the quality of your copper plating, via reliability in an HDI world is becoming an ever-greater challenge. This month we look at “The Hole Truth,” from creating the “perfect” via to how you can assure via quality and reliability, the first time, every time.
- Articles
- Columns
- Links
- Media kit
||| MENU - pcb007 Magazine
Estimated reading time: 5 minutes
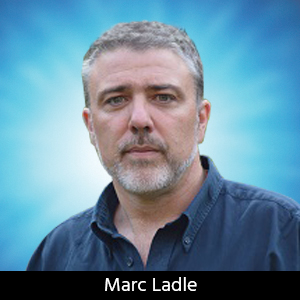
Ladle on Manufacturing: Why is the Developer Missing at BATM Systems’ Romania Facility?
I recently had the great pleasure to be working with BATM Systems at their new factory in Romania. The process concept is the brainchild of Steve Driver. For those who don’t know Steve, he is a gentleman of many years of experience in the UK printed circuit industry. Even after several decades of circuit production, he has an energy and enthusiasm for manufacturing which are most infectious!
As I walked into the BATM wet process area I had to question why the developer was missing from the set-up. The answer was straightforward enough: Because the etch resist is applied directly by “drop on demand” technology so there is no need for any dry film developer (or photoplotter, dry film laminator or UV exposure).
The clever printing technology has been supplied by a company called Mutracx, based in Holland. The machine they delivered to Romania is the Lunaris, and it can print a panel in not much more than 20 seconds, so it aligns very well to European etching and stripping speeds. It is a machine designed for fitment within the conveyorised image-etch-strip process and can be integrated into the middle of the manufacturing line very easily. The Lunaris is capable of being used for both innerlayer (print and etch) or for outer layer (pattern plate) using the same ink for both process routes. It strips in normal dry film stripping solution, although the temperature may need to be a little higher.
The high print speed, as compared to other drop on demand printers, is possible because of the multi-head print array spanning the complete width of the conveyor which allows each side of the panel to be imaged in a single movement through the print hardware. After printing the first side, the panel is automatically flipped over to print the second side. The flexibility of being able to print batches of 1 or 100 with virtually no changeover times and a very steady cost-per-print is very attractive.
Figure 1: An employee makes adjustments to the Mutracx Lunaris machine.
It also has AOI built in to check the image before it is delivered to the etch machine, so there is excellent security to make sure that there are no issues with any of the jets in the print heads for every panel that is printed.
The etch resist used on the Lunaris machine is supplied by Dow Chemical and this also has a lot of potential for wider use, as it can also be used as an electroplating resist. The nature of the resist once it has been applied to the panel is reasonably robust and it also strips easily and cleanly as long as you are able to achieve stripping temperatures of around 65°C.
The process is not currently a high-density solution. Drop-on-demand printing technology has a limitation on the resolution that can be achieved as each drop must have enough mass to travel across the air gap between the print head and the panel without drifting or distorting.
This means there is some limitation on the line and space that can be achieved; 0.150 microns (6 mil) or greater is quite comfortable on this machine. This technology aligns perfectly to the target products for the BATM factory so I must say this looks like it will be an excellent machine for them to use.
I had not previously visited Romania and was not really sure what to expect. I knew the factory was brand new and most of the staff had not previously been involved in making printed circuits. I should not have worried. The Romanian people are a credit to their country. They are hard-working and very conscientious, but also very friendly and helpful towards anyone who is visiting them. I have added Romania to the list of countries that I would visit for pleasure if the opportunity presents itself. There are areas of the country which have staggering natural beauty and, compared to the UK, the cost of accommodation and food is extremely reasonable.
I am sure other companies will follow where people like Driver are leading the way. It makes good commercial sense to manufacture in a country where the labour costs are relatively low—especially in printed circuit production, where the personnel costs are a substantial proportion of the overall cost of the product. I am also sure the future looks good for Romania and the Romanian people, with many companies wanting to invest in a low-cost manufacturing base within the European union. Romania is a perfect option. As I drove south from Hungary into Romania it became obvious that some substantial electronics companies have already established factories to benefit from the favourable economic conditions. I am sure this will be a growing market for years to come.
There are quite a few associated benefits to this new print technology. Factory real estate in Europe is expensive and an opportunity to cut out so many machines in one go makes the small footprint of the Lunaris very attractive. Add in the savings in power and water use and the case gets stronger and stronger. Then there is also the saving in process time, which is a big advantage in the fast turn-around European market. It is possible to be etching the circuit literally minutes after the manufacturing data has arrived in the factory.
I have a lot of respect for people who are prepared to take a step forward and try new technology. This is only the second Lunaris machine working in a production environment and I understand the other machine is mainly printing resist for electroplating. To move our industry on, it is critical that we continue to have people like Steve who are prepared to invest in new technology.
I work for an equipment supplier but I have no commercial interest or influence with either Mutracx or BATM Systems. The equipment I have installed there is much more conventional in its nature. I am genuinely interested in their new process and will be watching closely to see how they progress. I wish them every success.
Marc Ladle is director at Viking Test Ltd. To contact Ladle or to read past columns, click here.
This column originally appeared in the August 2017 issue of The PCB Magazine, click here.
More Columns from Ladle on Manufacturing
Ladle on Manufacturing: LED UV Cure—Does It Really Work?Ladle on Manufacturing: UV Cure LED Energy Saver
Ladle on Manufacturing: Sharing an Idea for Christmas
Ladle on Manufacturing: Behind the Scenes at productronica 2019
Ladle on Manufacturing: Sunday Afternoon in Dongguan
The Travelling Engineer, Installment 2
Ladle on Manufacturing: VCP—The Future of Plating
Developments in Wet Processing: Beyond Spraying and Dipping