-
-
News
News Highlights
- Books
Featured Books
- pcb007 Magazine
Latest Issues
Current IssueSales: From Pitch to PO
From the first cold call to finally receiving that first purchase order, the July PCB007 Magazine breaks down some critical parts of the sales stack. To up your sales game, read on!
The Hole Truth: Via Integrity in an HDI World
From the drilled hole to registration across multiple sequential lamination cycles, to the quality of your copper plating, via reliability in an HDI world is becoming an ever-greater challenge. This month we look at “The Hole Truth,” from creating the “perfect” via to how you can assure via quality and reliability, the first time, every time.
In Pursuit of Perfection: Defect Reduction
For bare PCB board fabrication, defect reduction is a critical aspect of a company's bottom line profitability. In this issue, we examine how imaging, etching, and plating processes can provide information and insight into reducing defects and increasing yields.
- Articles
- Columns
- Links
- Media kit
||| MENU - pcb007 Magazine
Estimated reading time: 4 minutes
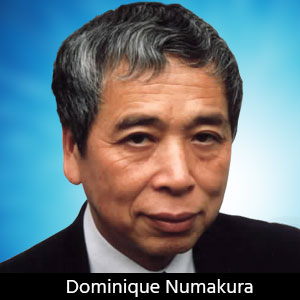
EPTE Newsletter: Can Toshiba Survive?
I am fortunate to have a business relationship with Toshiba that began in the early 1980s. I supplied flexible circuits, and my first interaction with Toshiba was designing a membrane switch for microwave ovens. Later, I was caught up in the consumer electronics boom in Japan. Many types of electronic devices were developed and commercialized, and Japanese companies were leading the global industry in technology and market share. About dozen large electronics companies in Japan were competitors in the global electronics market.
Toshiba was the leader in the electronics industry, and developed and marketed many types of electronic equipment and devices that included word processors, printers, VCR cameras, tape recorders, hard disc drives, transceivers, laptop computers, facsimiles, cellular phones, and more. Toshiba was also a leader in designing medical equipment. Toshiba was always one of the best electronics companies in the world.
Most of these electronic devices consumed high-end flexible circuits including high-density multilayer rigid-flex. I visited Toshiba’s plants two or three times a week to design flex circuit solutions. Toshiba’s engineers required cutting edge technologies for flex circuits that required me to develop new technologies continuously.
Toshiba challenged component suppliers to advance technologically, and rewarded us financially. We made a good living being part of the Toshiba family, and Toshiba posted record profits year over year during this time. Their engineers were capable and innovative in a very competitive consumer electronics industry. Component suppliers were very confident that Toshiba’s business strategy will allow them to have an income stream for a long time.
Well, nothing lasts forever and things changed with the turn of the century. Competitive pressures from Taiwan and Korea had an immediate impact on Japanese manufacturers. Market share and profits declined year over year, and companies were forced to shut their doors. Toshiba’s electronics division was strong enough to remain competitive during the recession, but their nuclear venture was weighing heavily on profits. In 2006, Toshiba acquired Westinghouse, the U.S. power plant arm of British Nuclear Fuels for $5.4 billion. Toshiba was hit with massive cost overruns and a delay linked to Westinghouse’s nuclear projects in the U.S.; Westinghouse was a failed bet. Toshiba sold their profitable medical business to compensate the losses, but still required another $20 billion cash to avoid bankruptcy, and a potential delisting from the Tokyo Stock Exchange. Currently, Toshiba is negotiating with three potential buyers to sell their semiconductor business, and prefer the buyer to be a Japanese fund group. However, Western Digital, the major memory device manufacturer is objecting to the deal because of the current contract with Toshiba. Business analysts cannot predict what will happen over the next few months.
Toshiba was once on top of the world; now they are selling off pieces of the company. Can they survive? They signed a deal on Thursday to sell their computer memory chip business, so money is coming in. I will be optimistic about their future, and use the poker phrase, “Chip and a chair,” meaning if they are still alive, if they have just one chip, they can still win.
Correction from previous edition
The revenue during the first half in Japan should read: 226.9 billion yens (2.08 billion U.S. dollars)
Headlines of the week
1. Canon (Major electronics company in Japan) 9/8
Will invest 23 billion yens to build a new plant in Miyazaki Prefecture for the production of digital cameras. The new plant will start the operation in August 2019.
2. Murata (Major component supplier in Japan) 9/11
Will commercialize a new RAIN RFID tag “LXFLANMXMG-003”. The new device is attachable on metallic surfaces.
3. Mitsui Chemical (Major chemical company in Japan) 9/14
Has agreed with Microwave Chemical to develop and commercialize the microwave process for various chemical reactions.
4. Taiyo Yuden (Major component supplier in Japan) 9/14
Has commercialized a new 0201 size (0.25 x 0.125 x 0.125 mm) ceramic chip capacitor with 100pF capacity for next-generation mobile devices.
5. Waseda University (Japan) 9/14
Has developed the world first high-speed P/E conversion chip that can manage multiple signals at the same time.
6. Hitachi (Major electric & electronics company in Japan) 9/14
Has developed a new SiC base CMOS chip technology. The semiconductor chips are reliable under high temperature and irradiation.
7. Shimadzu (Major scientific equipment supplier in Japan) 9/19
Will double the capacity of circuit board production in Philippines by 2019, adding more manufacturing lines.
8. Katolec (EMS Company in Japan) 9/20
Has received an order of reliable circuit board modules from Mitsubishi Heavy Industry for the H3 Rockets of JAXA.
9. Mitsubishi Electric (Major electric & electronics company in Japan) 9/22
Has developed a new SiC base power semiconductor chip with the smallest power loss.
10. Ushio Electric (Major electric device manufacturer in Japan) 9/25
Has rolled out a new UV-LED dryer “UniJet iIII” with the highest irradiation power density for the inkjet printing process.
11. Toshiba (Major electric & electronics company in Japan) 9/25
Has developed a new low-cost foldable solar cell module with a high conversion rate (10.5%) introducing perovskite compounds.
12. Idemitsu (Major petrochemical company in Japan) 9/26
Has agreed to develop organic EL materials for next generation display devices with Toray, a major organic material company in Japan.
13. Keio Gijuku University (Japan) 9/26
Has co-developed a new robot hand system with a unique vision device. The robot can handle ripe fruits without damage.
To reach Dominique K. Numakura, click here.
Visit DKN Research here.
Please contact haverhill@dknreseach.com for further information regarding the news items.
More Columns from EPTE Newsletter
EPTE Newsletter: Travel to Japan During COVIDEPTE Newsletter: A New COVID Surge in Taiwan?
EPTE Newsletter: COVID-19 PCR Test in Japan
EPTE Newsletter: Japan Failing in Vaccine Distribution
EPTE Newsletter: A Long Trip to the U.S.
EPTE Newsletter: Ten Years After Fukushima
EPTE Newsletter: Taiwan Releases 2020 PCB Production Numbers
EPTE Newsletter: The Printed Circuit Industry in China