-
-
News
News Highlights
- Books
Featured Books
- pcb007 Magazine
Latest Issues
Current IssueSales: From Pitch to PO
From the first cold call to finally receiving that first purchase order, the July PCB007 Magazine breaks down some critical parts of the sales stack. To up your sales game, read on!
The Hole Truth: Via Integrity in an HDI World
From the drilled hole to registration across multiple sequential lamination cycles, to the quality of your copper plating, via reliability in an HDI world is becoming an ever-greater challenge. This month we look at “The Hole Truth,” from creating the “perfect” via to how you can assure via quality and reliability, the first time, every time.
In Pursuit of Perfection: Defect Reduction
For bare PCB board fabrication, defect reduction is a critical aspect of a company's bottom line profitability. In this issue, we examine how imaging, etching, and plating processes can provide information and insight into reducing defects and increasing yields.
- Articles
- Columns
- Links
- Media kit
||| MENU - pcb007 Magazine
Estimated reading time: 3 minutes
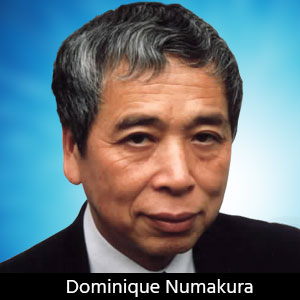
EPTE Newsletter: Metallization for Plastic Surfaces
During the 1980s, manufacturers ran around the barn a few times trying to decide the best way to produce reliable bond strength between polyimide sheets and copper foils when producing thin copper laminates for high-density flexible circuits. The two processes used to metallize the surface of polyimide films include a sputtering process and electroless plating. Sputtering generated a reliable adhesion for thin metallic layers on the inert plastic films, but the process was not productive because manufacturing had to be conducted in vacuumed chambers. This significantly increased the price for metallized films. A chemical plating process was simple and productive and had a lower manufacturing cost. Manufacturers preferred the lower priced chemical process. Unfortunately, the chemical process was not stable and did not produce reliable bond strength for thin copper laminates. Most manufacturers chose the sputtering process in spite of its high cost for the fine-line circuits of the chip-on-film (COF) substrates. Eventually, it became the industry standard.
Business opportunities using the electroless process dwindled during the 1990s and 2000s; however, chemical companies did not completely give up. They improved the process remarkably by introducing a new surface treatment process over the last few years, and more chemical suppliers threw their hat in the ring. Suppliers do not disclose detailed information about these chemicals, but there are sets in the chemical processes. DKN Research conducted a series of evaluations for these chemicals, and these new chemicals provide a more reliable bond strength for metallized layers on polyimide films compared to chemicals used 25 years ago. The cost increases for the new processes, but they have elevated performances due to their higher productivities. Additionally, the new chemical process provides additional advantages compared to other physical metallization processes including sputtering.
The first advantage is the processes can do double-sided metallization using the same process as for single-sided laminates. This is a huge advantage for new chip-on-flex (COF) substrates due to market trends. The next generation driver modules for flat panel displays will require finer traces down to 20-micron lines and spaces with smaller microvia holes less than 20 microns in diameter. The plating process using the new chemicals can produce a wide range of double-sided copper laminates down to 0.2-micron metallization.
The second advantage of using this process is the wide variety of substrates available. Traditional polyimide films are available using this process, as well as new polyimide films, including transparent versions. Trials using other plastic films (e.g., PET, PEN, LCP, PEEK) and several types of fluoride polymers were successful in producing unique copper laminates. There are a few of them that can effectively make larger sized piezoelectric devices, such as mechanical sensors and actuators.
Several flexible circuit manufacturers developed a new semi-additive process using new chemicals to generate ultrafine traces down to one-micron line and space for single-sided, double-sided, and multilayer circuits. The new plating process will create more functions for printed circuit manufacturers.
Headlines
1. NEDO (Major R&D organization in Japan) 6/18
Co-developed the world’s largest perovskite-type photovoltaic cell module (703 cm2) with an 11.7% conversion rate.
2. Toshiba Infrastructure Systems and Solutions (Subsidiary of Toshiba) 6/19
Agreed with Sojitsu and Companhia Brasileira de Metalugia e Mineração for the R&D projects of NbTi oxide as the new electrode of the next generation of lithium-ion batteries.
3. No new folk studio (Venture company in Japan) 6/19
Found success with the field test of Internet of Things (IoT) module developed for shoes, based on the standard of ORPHE CORE using the LoRaWAN Network.
4. Air Water (Gaseous product supplier in Japan) 6/21
Developed a new small size nitrogen gas generator “BPN3.” The equipment produces nitrogen gas with approximately 97–99.99% purity for soldering.
5. SUS (Metallic device manufacturer in Japan) 6/26
Completed the construction of a new plant in Kumamoto, Kyushu. The plant will produce aluminum frames of semiconductor equipment.
6. Hamamatsu Photonics (Major optical device manufacturer in Japan) 6/25
Will invest 2.8 billion yen to build new manufacturing plants for multi-pixel photon counter (MPPC) modules.
7. Tosoh (Major specialty chemical supplier in Japan) 6/26
Released a new flexible substrate material for organic thin-film transistor (TFT) arrays suitable for low-cost printing processes.
8. KANEKA (Major organic material supplier in Japan) 6/26
Will invest 11 billion yen to expand the manufacturing capabilities of polyimide films and graphite sheets three times larger.
9. Fujitsu Semiconductor (Japan) 6/29
Agreed with UMC, a major semiconductor contract manufacturer in Taiwan, to sell its manufacturing subsidiary in Mie Plant for 57.6 billion yen.
10. TIT (Technical college in Tokyo) 7/2
Developed a new flexible tera-Hz sensor device built on a carbon nanotube membrane for wearable usages.
Please contact haverhill@dknreseach.com for further information and news.
More Columns from EPTE Newsletter
EPTE Newsletter: Travel to Japan During COVIDEPTE Newsletter: A New COVID Surge in Taiwan?
EPTE Newsletter: COVID-19 PCR Test in Japan
EPTE Newsletter: Japan Failing in Vaccine Distribution
EPTE Newsletter: A Long Trip to the U.S.
EPTE Newsletter: Ten Years After Fukushima
EPTE Newsletter: Taiwan Releases 2020 PCB Production Numbers
EPTE Newsletter: The Printed Circuit Industry in China