-
-
News
News Highlights
- Books
Featured Books
- pcb007 Magazine
Latest Issues
Current IssueSales: From Pitch to PO
From the first cold call to finally receiving that first purchase order, the July PCB007 Magazine breaks down some critical parts of the sales stack. To up your sales game, read on!
The Hole Truth: Via Integrity in an HDI World
From the drilled hole to registration across multiple sequential lamination cycles, to the quality of your copper plating, via reliability in an HDI world is becoming an ever-greater challenge. This month we look at “The Hole Truth,” from creating the “perfect” via to how you can assure via quality and reliability, the first time, every time.
In Pursuit of Perfection: Defect Reduction
For bare PCB board fabrication, defect reduction is a critical aspect of a company's bottom line profitability. In this issue, we examine how imaging, etching, and plating processes can provide information and insight into reducing defects and increasing yields.
- Articles
- Columns
- Links
- Media kit
||| MENU - pcb007 Magazine
Estimated reading time: 3 minutes
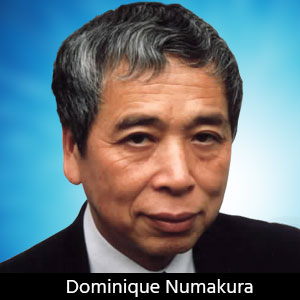
EPTE Newsletter: Thinner and Lighter Printed Circuits
Manufacturers from the electronics industry consistently compete to create higher density circuits. Cutting edge semiconductor manufacturers can generate less than 10 nanometer traces on silicon chips. Compared to integrated circuit (IC) chips, the fine pattern capabilities from printed circuit manufacturers are three orders lower while flex circuit manufacturers are generating patterns finer than 15 microns on polyimide films using a reel-to-reel process.
Flexible circuits have some advantages when considering the thickness and weight of circuit devices. Wafer manufacturers are ready to produce 20-micron silicon wafers, but chip manufacturers are not ready for thin wafers. The industry standard in the United States and Europe for polyimide film thickness used to be 50 microns because of the reliable handling. However, Asian manufacturers are using 25-micron polyimide films due to the lower cost. Over the last decade, the thickness of polyimide film has become thinner and thinner even though the cost has remained the same. End users are demanding thinner flex circuits that are earmarked for tight spaces in smartphones and smartwatches. Now, 12.5-micron polyimide film is the predominant size for the industry.
The thickness of copper foils has also started to become thinner. One-ounce copper foil (35-micron) is no longer the standard thickness for the flex circuit industry. The majority of the industry is consuming 18- and 12-micron copper foils for major laminates. Consumer electronics continue to evolve and circuit customers are requiring thinner circuits. Polyimide film manufacturers have commercialized 9-, 7.5-, and 5-micron films. Copper foil suppliers have been also developing thinner foils down to two microns with carrier sheets.
DKN Research conducted several trials with ultra-thin polyimide films and found no issues with microhole generation with a UV laser. Metallization by sputtering or elecro/electroless plating was successful in creating conductor layers thinner than 0.2 microns while maintaining bond strength. Standard laser scribing and photolithography are available to generate circuit patterns on thin polyimide film. Lastly, the total thickness of the flexible circuit was about 5.5 microns and the unit weight of the thin circuits was less than 10 milligrams per square centimeter.
We learned how difficult it is to handle thin flexible circuits during our trials. For example, 7.5-micron polyimide films are manageable but 5-micron films require special tools and equipment. You must also be aware of the static electricity from the plastic films during manufacturing and assembling. It is almost impossible to keep the thin film materials flat while processing with traditional equipment, so the manufacturing yield and assembling yield are quite low.
Headlines
1. Daio Paper (Major paper manufacturer in Japan) 8/1
Developed a new manufacturing process of cellulose nanofiber that makes the fibers transparent up to 92%.
2. Toshiba (Major electric and electronics company in Japan) 8/2
Developed a new recognition system for players in sporting events. It will reduce analyzing work for TV directors.
3. Fuji Electric (Major electric equipment manufacturer in Japan) 8/2
Rolled out a new power conditioner system for solar power generation plants that will reduce the total cost and combine energy storage devices.
4. Kyocera (Major electronics company in Japan) 8/6
Released a new connector “6892 Series” with a 0.5-mm pitch for high-density flex circuits and flat cables. It has safety connection mechanisms to avoid misconnections.
5. NEDO (Major R&D organization in Japan) 8/9
Started constructing the world’s largest hydrogen energy system with 10000-kW capacity in the Fukushima prefecture.
6. Fujitsu (Major electronics company in Japan) 8/10
Successfully strengthened the power of GaN transistors for radar equipment that will make the radar search distance 2.3 times longer.
7. Yokogawa (Major equipment manufacturer in Japan) 8/14
Developed a new IR base thickness measuring equipment—WG5152—with an accuracy of +/- 0.2 microns for the process control of plastic films.
8. Mitsubishi Material (Major material supplier in Japan) 8/20
Will co-develop recycling processes of cobalt, nickel, and other rare earth metals from used lithium-ion batteries.
9. Murata (Major device manufacturer in Japan) 8/20
Will build a new manufacturing plant of microelectromechanical (MEMS) sensors in Finland and hire 200 new employees. The devices will be used as safety systems for automobiles and medical pacemakers.
10. Hitachi (Major electric and electronics company in Japan) 8/21
Commercialized a new data management system for high-speed liquid chromatography. Operators can manage the data without long training.
More Columns from EPTE Newsletter
EPTE Newsletter: Travel to Japan During COVIDEPTE Newsletter: A New COVID Surge in Taiwan?
EPTE Newsletter: COVID-19 PCR Test in Japan
EPTE Newsletter: Japan Failing in Vaccine Distribution
EPTE Newsletter: A Long Trip to the U.S.
EPTE Newsletter: Ten Years After Fukushima
EPTE Newsletter: Taiwan Releases 2020 PCB Production Numbers
EPTE Newsletter: The Printed Circuit Industry in China