-
-
News
News Highlights
- Books
Featured Books
- pcb007 Magazine
Latest Issues
Current IssueSales: From Pitch to PO
From the first cold call to finally receiving that first purchase order, the July PCB007 Magazine breaks down some critical parts of the sales stack. To up your sales game, read on!
The Hole Truth: Via Integrity in an HDI World
From the drilled hole to registration across multiple sequential lamination cycles, to the quality of your copper plating, via reliability in an HDI world is becoming an ever-greater challenge. This month we look at “The Hole Truth,” from creating the “perfect” via to how you can assure via quality and reliability, the first time, every time.
In Pursuit of Perfection: Defect Reduction
For bare PCB board fabrication, defect reduction is a critical aspect of a company's bottom line profitability. In this issue, we examine how imaging, etching, and plating processes can provide information and insight into reducing defects and increasing yields.
- Articles
- Columns
- Links
- Media kit
||| MENU - pcb007 Magazine
Estimated reading time: 3 minutes
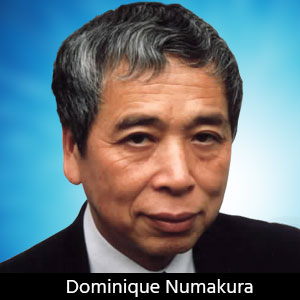
EPTE Newsletter: New Materials for Wearable Electronics
Technology continues to evolve, and wearable electronics are the focal point for many new concepts. The next generation of wearable products for the consumer electronics industry will create a new market with nothing but upside for manufacturers and suppliers. One feature of wearable devices is the ability to attach electronic devices on the skin for long-term health monitoring. Flexible circuits are the primary wiring ingredient for these wearable devices; however, the base materials will dramatically change and pose challenges for materials and manufacturing.
Polyimide films, such as DuPont’s Kapton and polyethylene terephthalate (PET) films, are the predominant material for traditional flexible circuits. To create a more reliable circuit for these new products, manufacturers increased insulation resistance, heat resistance, dimensional stabilities, and flexing endurance. They also raised chemical resistance against acid, alkaline, and organic solvents, and lowered moisture absorption. Film manufacturers continue to elevate their product performances to satisfy customer’s requirements, and flexible and stretchable wearable devices require many changes.
Circuit elasticity is another hurdle for film manufacturers. Medical devices attached to the skin require elasticity. Unfortunately, current polyimide films used for flexible circuits have almost no elasticity and are not suitable to use as the base material in medical devices. Thin sheets of urethane and silicone rubber could be alternatives; however, the traditional conductive material and circuit generation process—such as copper foil and etching—cannot be applied to the rubber sheets due to low flexibility and shearing strength. Thick-film conductors that generate screen-printing processes could be another solution, but several updates to the print processes and modifications to the ink materials would be necessary.
Two more challenges with wearable devices include hygroscopy and gas permeability of the circuits. Traditional flexible circuits would not allow sweat to dissipate when using a wearable electronic product attached to the skin. Several ideas involved using high-quality, lightweight cotton, polyester, or Lycra blends to draw moisture away from the body. Unfortunately, these materials are not suitable for building electronic circuits. Combinations of screen printing and cushion materials could help electronic circuits on the unstable and non-uniform substrates.
Several medical applications also require heat-resistant circuit transparency and reliable connections. Traditional polyimide films are dark brown or orange and cannot be used in transparent circuits. Several material manufacturers are developing transparent and heat-resistant plastic films to use as the base material in flexible circuits. Further, device manufacturers are considering the use of transparent conductive materials, such as indium tin oxide (ITO) and silver nanowire ink. Since the heat resistance is lacking, a technology that will guarantee a reliable connection is not available at this time.
Wearable devices are here to stay, and the next generation of devices will be even more advanced than current products. This evolution brings a whole new demand for material properties. Wearable tech is a $6 billion global market, and some analysts claim it grow to $34 billion by 2020.
Headlines
1. Tokyo University (Japan) 8/29
Developed a new continuous process to generate hydrogen with new catalysis.
2. Hitachi (Electronics company in Japan) 9/3
Developed a new recovery process of zirconium from high-level radioactive waste.
3. Murata (Device manufacturer in Japan) 9/4
Commercialized a new ultra-high frequency (UHF) band, radio frequency identification device (RFID) tag—LXMSANMXMG-202—attachable on metallic surfaces.
4. Panasonic (Electronics company in Japan) 9/6
Commercialized a new underfill compound for the secondary packaging of the automobile components with high heat resistance.
5. Fujitsu (Electronics company in Japan) 9/6
Commercialized a new liquid server cooling system—Fujitsu Server PRIMERGY—that makes integration density double.
6. Kyoto University (Japan) 9/6
Established the manufacturing process of the perovskite base photovoltaic cell with a high price-to-earnings (P/E) conversion rate.
7. Toshiba (Electronics company in Japan) 9/7
Developed a new Bluetooth low energy system on chip (SoC) that has executed long-distance telecommunication up to 600 meters.
8. DNP (Printing company in Japan) 9/10
Developed a new head-mounted display—DNP Virtual Gallery—where the user can see 360-degree moving pictures and make 3D copies.
9. NEDO (R&D organization in Japan) 9/10
Started a new project for a wind power generation system on the ocean with targets of 20% cost reduction.
10. Toppan Printing (Printing company in Japan) 9/10
Co-developing a fully automatic inventory managing system using a robot and radio frequency (RF) integrated circuit (IC) tag with ZMP Inc.
11. Ricoh (Electronics company in Japan) 9/11
Launched a new voltage regulator—R1525 Series—with extremely low power consumption for automobile use.
Dominique K. Numakura is the managing director of DKN Research LLC. Contact haverhill@dknreseach.com for further information and news.
More Columns from EPTE Newsletter
EPTE Newsletter: Travel to Japan During COVIDEPTE Newsletter: A New COVID Surge in Taiwan?
EPTE Newsletter: COVID-19 PCR Test in Japan
EPTE Newsletter: Japan Failing in Vaccine Distribution
EPTE Newsletter: A Long Trip to the U.S.
EPTE Newsletter: Ten Years After Fukushima
EPTE Newsletter: Taiwan Releases 2020 PCB Production Numbers
EPTE Newsletter: The Printed Circuit Industry in China