-
-
News
News Highlights
- Books
Featured Books
- pcb007 Magazine
Latest Issues
Current IssueSales: From Pitch to PO
From the first cold call to finally receiving that first purchase order, the July PCB007 Magazine breaks down some critical parts of the sales stack. To up your sales game, read on!
The Hole Truth: Via Integrity in an HDI World
From the drilled hole to registration across multiple sequential lamination cycles, to the quality of your copper plating, via reliability in an HDI world is becoming an ever-greater challenge. This month we look at “The Hole Truth,” from creating the “perfect” via to how you can assure via quality and reliability, the first time, every time.
In Pursuit of Perfection: Defect Reduction
For bare PCB board fabrication, defect reduction is a critical aspect of a company's bottom line profitability. In this issue, we examine how imaging, etching, and plating processes can provide information and insight into reducing defects and increasing yields.
- Articles
- Columns
- Links
- Media kit
||| MENU - pcb007 Magazine
Estimated reading time: 3 minutes
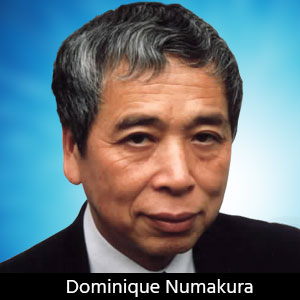
EPTE Newsletter: Sputtering or Chemical Plating?
More than 20 years ago, material manufacturers competed with each other to develop adhesiveless copper-clad laminates for the next generation of flexible circuits. A dozen or so companies were leaders in the pack with their new technologies. These technologies were categorized into two types: a casting and laminating process, and the metallization of polyimide films.
The casting and lamination process used a couple of polyimide resins coated on copper foils and baked to form a reliable base layer. Next, a second copper foil was laminated on the other side of the polyimide layers. The process provided a reliable bond strength between the base film and copper, but the manufacturing process was complicated, and the cost was relatively high.
Metallization of the polyimide film required the production of a seed layer before electrical plating. The two choices to produce the thin seed layer were a sputtering in a vacuumed chamber or electroless plating in a wet bath. The sputtering created reliable bond strength, but the process is slow and expensive. Electroless plating is a simple process that provided a low-cost solution, but unstable bond strength was an issue.
There was no perfect manufacturing process; each had advantages and disadvantages. At the time, I was a project leader for a manufacturer of casting-type adhesiveless laminates. The manufacturing facility was subpar and did not have enough capabilities to satisfy customers’ requirements. I needed to change our business strategy. First, I reorganized the R&D engineering staff to focus on engineering services for small volume customers who required high-end applications. Simultaneously, I required our process engineers to improve quality and yields. The strategy was successful. We acquired strategic customers with high-volume applications and increased our margins. Our products became the industry standard.
The metallized laminates with sputtering did not garner much support in the flex circuit industry. It is still popular as a special application for driver IC modules in flat panel displays. The modules require very fine traces; accordingly, they demanded very thin copper foils. The devices were inexpensive, and the market grew rapidly. The sputtered laminate became the industry standard.
Unfortunately, metallized laminate with electroless plating was not successful even though the process was inexpensive. Manufacturers could not improve the bond strength significantly enough, and the process is no longer used in the industry.
I developed a new metallization process comparing sputtering and electroless plating for medical devices. Both technologies improved significantly over the last 10 years. They have different advantages, and I use them depending on the application. They are capable of metallizing on polyimide films as well as new exotic materials such as rubber sheets, paper, cloths, and more, and are a comfortable dielectric material for wearable electronic devices.
Can the metallization process generate a new flexible laminate business for wearable devices? Absolutely! Feel free to reach out to DKN Research for a collaborative project centered on wearable electronics
Headlines
1. ELIIY Power (Battery manufacturer in Japan) 11/26
Developed a new lithium-ion battery with non-flammable ion liquid.
2. AIST (R&D organization in Japan) 11/28
Developed a new anode material of SiO deposited by vacuumed evaporation for lithium-ion batteries that makes battery capacity five times larger compared to the traditional graphite anode.
3. NTT (Telephone company in Japan) 11/29
Demonstrated a prototype model of a flexible and transparent secondary battery for IoT applications.
4. AGC (Glass product supplier in Japan) 11/30
Developed a glass base transparent antenna for 28-GHz band 5G telecommunications targeting the windows of automobiles and buildings.
5. JAE (Connector manufacturer in Japan) 12/5
Released a new waterproof connector series “MX60A” for engine room use of automobiles; the pin counts can be up to 177.
6. DaiShinku (Vacuumed equipment manufacturer in Japan) 12/5
Developed the industry’s smallest quartz device with an embedded temperature sensor in the package (package size: 1210 (1.2 x 1.0 x 0.5 mm)).
7. Toshiba (Electric and electronics company in Japan) 12/6
Will release a new compact 3.5” HDD with 14-TB capacity for consumer applications next February.
8. Yasukawa (Robot manufacturer in Japan) 12/7
Unveiled its new manufacturing plant “Yaskawa Solution Factory” with various IoT technologies. The productivity will be three times higher, and the lead time will be one-sixth.
9. Ricoh (Electronics company in Japan) 12/10
Has been introducing a “new deep-learning process” for robotics using the generative adversarial network (GAN), which imitates the actions of human beings.
10. Takenaka (Construction company in Japan) 12/10
Has been introducing drones to check the progress of constructions in limited spaces in high-density building areas.
Dominique K. Numakura is the managing director of DKN Research LLC.
More Columns from EPTE Newsletter
EPTE Newsletter: Travel to Japan During COVIDEPTE Newsletter: A New COVID Surge in Taiwan?
EPTE Newsletter: COVID-19 PCR Test in Japan
EPTE Newsletter: Japan Failing in Vaccine Distribution
EPTE Newsletter: A Long Trip to the U.S.
EPTE Newsletter: Ten Years After Fukushima
EPTE Newsletter: Taiwan Releases 2020 PCB Production Numbers
EPTE Newsletter: The Printed Circuit Industry in China