-
- News
- Books
Featured Books
- smt007 Magazine
Latest Issues
Current IssueSupply Chain Strategies
A successful brand is built on strong customer relationships—anchored by a well-orchestrated supply chain at its core. This month, we look at how managing your supply chain directly influences customer perception.
What's Your Sweet Spot?
Are you in a niche that’s growing or shrinking? Is it time to reassess and refocus? We spotlight companies thriving by redefining or reinforcing their niche. What are their insights?
Moving Forward With Confidence
In this issue, we focus on sales and quoting, workforce training, new IPC leadership in the U.S. and Canada, the effects of tariffs, CFX standards, and much more—all designed to provide perspective as you move through the cloud bank of today's shifting economic market.
- Articles
- Columns
- Links
- Media kit
||| MENU - smt007 Magazine
Estimated reading time: 4 minutes
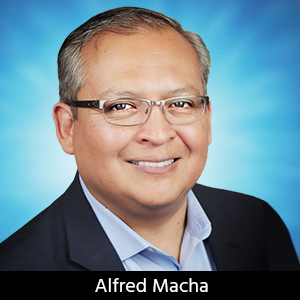
Operational Excellence: Becoming the Preferred Supplier, Phase 1—Transform Your Company's Culture With Lean Sigma
A strategic customer has just emailed you the quarterly supplier scorecard, and you gather your team to review it. Reviewing the performance scorecard results should not be a surprise to anyone in your team since you already know your on-time delivery; quality, technology, and cost-reduction initiatives; and customer-service responsiveness KPIs with that customer have not been stellar. The emotional roller coaster starts with the realization of the impact the scorecard has on your future growth with that customer account. The knee-jerk reaction of some executives is to demand immediate improvements at all costs, which will create a stressful environment. The ability of the team to perform is in question. Confidence in your team falters, but an opportunity to transform your company arises.
Every manufacturing organization understands that customers have options to select suppliers that provide consistent product quality and great service. Customers continuously evaluate their supply base; they have strategic initiatives to get the right suppliers in their AVL. As a supplier, you are confident that your technology and process capabilities will open doors for new programs. However, growing an account into a long-term engagement will require you to be a strategic and preferred supplier to your customer. Becoming a preferred supplier does not happen overnight; it requires a well-defined roadmap that will transform your organization over time.
In the next few monthly columns, I will provide the fundamental concepts to achieve the goal of becoming a preferred supplier to your customers. The first phase is to transform your company’s culture with Lean Sigma. The approach introduced in this column can be adopted by any manufacturing organization through the following steps.
Leadership Commitment to Core Values
The executive team defines the vision of the company and the respective core values to support the vision. Unfortunately, most companies often specify values to satisfy customer expectations instead of representing values that are aligned with behaviors that employees can identify with. To initiate a culture transformation, the executive team needs to clearly establish values that drive the expected behaviors for its employees. Once these are established, the key to success is the commitment of company leaders to demonstrate behaviors and actions that support these values; it’s a concerted effort that requires consistency. One initiative is to create a Lean Sigma mentality that supports your values.
Designate a Lean Sigma Champion
We must first understand the meaning of Lean Sigma. Lean Six Sigma is a series of methods that require team collaboration to improve performance by systematically removing waste and reducing variation. Many books provide guidance on how to implement these methods. One of my preferred books is Lean Six Sigma: A Beginner’s Guide to Understanding and Practicing Lean Six Sigma, authored by Jim Hall and Tina Scott. This book provides a practical approach to implementing the Lean Sigma journey.
Before starting this journey, the leadership team must designate a Lean Sigma champion that will be empowered to lead the transformation. From my experience, companies that have been successful with Lean Sigma designate an executive with decision-making authority to be the Lean Sigma champion. I advise not to assign this responsibility to the quality or engineering manager. Lean Sigma is a lot more involved that one departmental function, and it’s best not to create the perception that only quality personnel and engineers work on Lean Sigma projects. Lean Sigma involves the entire organization working together to succeed.
Figure 1: Lean Sigma toolkit.
The Lean Sigma champion does not have to be an expert in advanced quality tools, which are required in carrying out projects that support Lean Sigma. Instead, the Lean Sigma champion will create the roadmap, toolkit, and accountability system for engineers, managers, and individual contributors that will be trained as subject-matter experts in the methods to implement Lean Sigma. Various methods exist to support a Lean Sigma transformation. Figure 1 illustrates some of the most common methods.
Keep It Simple
This is the secret to Lean Sigma success. The complexity level of Lean Sigma implemented at Tier 1 companies will not work for Tier 3 or 4 manufacturing organizations. Your Lean Sigma champion needs to consider available resources to roll out a program that will be sustainable. A mistake often made is to make Lean Sigma a theoretical exercise instead of a practical business tool for the organization. The phrase “by the book” should not be applied to Lean Sigma. Use methods and approaches that fit your organization.
One example is the use of design of experiments (DOE) for your Lean Sigma projects. Implementing a DOE requires engineering effort, material cost, and equipment time to carry out a DOE correctly. It is an investment that an organization makes in carrying out this type of exercise. The Lean Sigma champion should provide proper guidance to determine when a DOE is applicable for a Lean Sigma project. Not all Lean Sigma projects should require DOE deliverables.
Keep It Agile
Your company must adopt the mentality of agile project management. This concept is a great tool not only for software development but also for manufacturing and will be explored in more detail in future columns. For the purposes of this column, the mentality of agile project management requires a tactical approach of monitoring progress frequently and defining a timeline to complete planned work activities in segments. The Lean Sigma champion must adopt that mentality to accelerate progress while monitoring performance closely.
Make Everyone Accountable
The old adage of holding everyone accountable needs to be reintroduced not as a punitive management method but as a method of self-accountability. The culture transformation using Lean Sigma will instill genuine pride in the team so that employees feel proud of what they do and of the company for which they work. This transformation allows for accountability to be seen as a personal accomplishment assessment.
Alfred Macha is the president of AMT Partners. He can be reached at Alfred@amt-partners.com.
This column was originally published in the June 2019 issue of SMT007 Magazine.
More Columns from Operational Excellence
Operational Excellence: Strengthen Your Design Transfer Process With Agile NPIOperational Excellence: Redefine Recruiting to Attract and Hire the Right Talent
Operational Excellence: Process Effectiveness Qualification
Operational Excellence: Working Remotely–Redesign Your Information Systems
Operational Excellence: Sharpening Your Organization’s Competencies
Operational Excellence: Hiring and Retaining Top Employees
Operational Excellence: Update Your Business Contingency Plan
Operational Excellence: The Gemba Transformation of Manufacturing With AI