-
- News
- Books
Featured Books
- smt007 Magazine
Latest Issues
Current IssueSupply Chain Strategies
A successful brand is built on strong customer relationships—anchored by a well-orchestrated supply chain at its core. This month, we look at how managing your supply chain directly influences customer perception.
What's Your Sweet Spot?
Are you in a niche that’s growing or shrinking? Is it time to reassess and refocus? We spotlight companies thriving by redefining or reinforcing their niche. What are their insights?
Moving Forward With Confidence
In this issue, we focus on sales and quoting, workforce training, new IPC leadership in the U.S. and Canada, the effects of tariffs, CFX standards, and much more—all designed to provide perspective as you move through the cloud bank of today's shifting economic market.
- Articles
- Columns
- Links
- Media kit
||| MENU - smt007 Magazine
Estimated reading time: 6 minutes
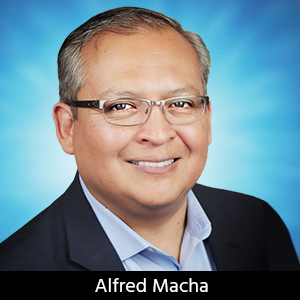
Operational Excellence: Becoming the Preferred Supplier, Phase 2—The Six Pillars
Last month’s column introduced the first phase of the roadmap in becoming a preferred supplier, which initial phase consisted of transforming your company’s culture with a Lean Six Sigma approach. Takeaways included creating a culture that embraces continuous improvement by creating the right mindset of ownership, empowerment, agility, and accountability. Your Lean Six Sigma program needs to be rightly sized to your organization’s structure for it to be sustainable. The second phase involves establishing the six pillars of operational effectiveness.
Attaining quality systems certification to a base standard of ISO 9001 or industry specific QMS standard for medical devices (ISO 13485), automotive (TS 16949), telecommunications (TL 9000), or aerospace (AS9100D) will provide you a solid foundation to your operations. The next step is to build on that quality systems foundation and take your factory to a higher level of performance by establishing six pillars to achieve operational effectiveness (Figure 1):
- Data integrity
- Visual factory
- Right metrics
- Change control
- Process monitoring
- Learning culture
Figure 1: Operational excellence.
1. Data Integrity
Remember that decisions are made from data captured from your process. Get the data right! This sounds basic, but many organizations fail to consistently retrieve accurate data from their manufacturing floor. Technological advancements in scanning, automated measurements, and inspection allow for accurate data collection. However, many manufacturing processes still require manual data entry data inputs into their ERP, MES, or paper logs in the production floor to capture process or product data.
Make sure that you have configured your data collection system with the right instructions and verification steps to ensure data is collected accurately. A best practice in a manufacturing environment is to have visual guides or pictures that clearly describe a process condition or product defect with a reference code that can be used in your ERP or data collection system. Train your workforce to these visual references and establish a simple audit plan to verify data accuracy on a regular basis. At the end of the day, the credibility of your operations starts with the confidence your team has in making decisions based on the right data.
2. Visual Factory
The year was 2001, and I was a quality manager for a large PCB company in Arizona that had a 24/7 operation. The factory had a footprint of 250,000 square feet and a workforce of 1,500 employees. The executive team was determined to transform the factory into a top performer in the industry, and one initiative was to reduce process variation by having visual work instructions. We had to convert over 300 technical procedures across the factory into practical visual work instructions. The effort required the involvement of over 50 employees from across the factory.
The project resulted in higher product yields, fewer customer complaints, and high employee engagement and customers took notice. We became a preferred PCB supplier in the industry. Now, manufacturing companies have cost-effective options to create not only visual work instructions but also a complete visual factory with the use of electronic visual displays, tablets, smartphones, and customized software to support this initiative.
The benefits of implementing an effective visual factory can be quantified. A software development organization, VKS, that specializes in visual factory solutions has research data collected via CMP AMS Ltd. and reports a quality improvement of 93% reduction of internal defects from the implementation of smart work instructions (Figure 2).
Figure 2: Defect reduction with smart work instructions.
3. Right Metrics
Measurements drive behaviors. There is so much truth in that statement, and having the right metrics in your operations can make the difference in how the workforce performs in the factory. Top companies create metrics or key performance indicators (KPIs) with the focus to bring value to their employees. Philosophically, remind your team that it’s not the quantity of metrics but the quality of metrics that matter. Fewer is better.
Here are five questions you can ask as you define the right metrics:
• What is your organization’s value proposition?
• What behaviors do you want to instill in the workforce that supports your value proposition?
• Are you collecting the right data to measure outputs that drives those behaviors?
• How frequently will you be communicating the metrics to your employees?
• What action plans will you take to address trends or outliers shown in your metrics?
Once you have documented a procedure that answers these questions, then select a handful of metrics and make them part of your culture’s DNA.
Figure 3: Example of change control that affects products.
4. Change Control
Change is inevitable, and how we control change is challenging. Hundreds of books and methods on change management exist with valuable theoretical guidance. However, the secret recipe of change control is not creating the perfect procedure based on theory; instead, it’s about creating a practical procedure based on risk levels when a change occurs.
I highly recommend funneling all changes that affect manufacturing into one common change control system. One system allows for standardization, consistency, and traceability of records. Figure 3 provides a simple flowchart of how this system can be set up based on risk levels.
5. Process Monitoring
The challenge that every manufacturing company faces is uncontrolled variation. While it’s inevitable that the parameters of your operation are going to change in some ways from time to time, it’s important to ensure that those variations are controlled and predictable. Ensure that you’re always one step ahead of the game.
Evaluating your process(es) to determine what factors have a higher impact on variation is a must. Once you identify those factors that can induce higher levels of process variation, then you need to closely monitor the outputs of those factors. This is where process monitoring becomes a vital component of your operations. Process monitoring can be carried out in many forms. Here are common methods for process monitoring that have proven to be effective in many organizations:
• Identify critical parameters for your operation and monitor these parameters via statistical process control. Not every parameter is critical so you will need to keep the list of critical parameters to a manageable number
• Allocate adequate funding to invest in proper automated process monitoring systems when possible
• Implement a process audit/monitoring program where qualified personnel can spot check critical operations constantly
• Change the mindset on the production floor. Process monitoring should never be viewed as a method to blame the operator for errors; rather, it should be viewed as a tool to help operations personnel achieve success
6. Learning Culture
Traditional training programs require periodic refresher training of procedures or work instructions with a certification exam at the end to demonstrate competency in the subject content presented. This approach brings value to organizations in reaching adequate levels of operator knowledge and compliance but does not create the level of learning that great organizations foster.
Achieving operational effectiveness requires a new level of engagement with employees by creating a learning culture. The first step in creating a culture of learning in your workplace begins with your leaders. Since they are reinforcing training initiatives, they should be supportive of a learning environment. All employees need to be empowered to reach their potential by continuously gaining new skills and knowledge via in-house mentoring or coaching or external professional development courses.
Here are a set of practical guidelines that you can start implementing in your organizations to create a learning culture.
- Offer leadership sessions to all employees. Everyone in the organization should be prepared to lead a team, project, or activity as opportunities present themselves.
- Encourage employees to make decisions based on the knowledge they have gained. Challenge employees to apply newly learned knowledge in their current positions.
- Give feedback on employees’ performance after they have learned new skills. New knowledge won’t be retained unless it’s applied in an employee’s work function.
- Recognize learning. Employees who have successfully learned new skills and abilities should be recognized, and encourage others to follow suit.
Alfred Macha is the president of AMT Partners.
This article was originally published in the July 2019 issue of SMT007 Magazine.
More Columns from Operational Excellence
Operational Excellence: Strengthen Your Design Transfer Process With Agile NPIOperational Excellence: Redefine Recruiting to Attract and Hire the Right Talent
Operational Excellence: Process Effectiveness Qualification
Operational Excellence: Working Remotely–Redesign Your Information Systems
Operational Excellence: Sharpening Your Organization’s Competencies
Operational Excellence: Hiring and Retaining Top Employees
Operational Excellence: Update Your Business Contingency Plan
Operational Excellence: The Gemba Transformation of Manufacturing With AI