-
-
News
News Highlights
- Books
Featured Books
- pcb007 Magazine
Latest Issues
Current IssueSales: From Pitch to PO
From the first cold call to finally receiving that first purchase order, the July PCB007 Magazine breaks down some critical parts of the sales stack. To up your sales game, read on!
The Hole Truth: Via Integrity in an HDI World
From the drilled hole to registration across multiple sequential lamination cycles, to the quality of your copper plating, via reliability in an HDI world is becoming an ever-greater challenge. This month we look at “The Hole Truth,” from creating the “perfect” via to how you can assure via quality and reliability, the first time, every time.
In Pursuit of Perfection: Defect Reduction
For bare PCB board fabrication, defect reduction is a critical aspect of a company's bottom line profitability. In this issue, we examine how imaging, etching, and plating processes can provide information and insight into reducing defects and increasing yields.
- Articles
- Columns
- Links
- Media kit
||| MENU - pcb007 Magazine
Estimated reading time: 3 minutes
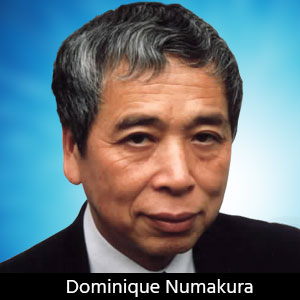
EPTE Newsletter: JPCA Show 2019, Part 4
Editor’s Note: This is Part 4 of Dominique Numakura’s coverage of the JPCA Show. Read Part 1, Part 2, and Part 3 here.
Many vendors and manufacturers featured test equipment for flexible circuits. It was worthwhile for me to take a long look at this equipment that evaluates new functional, flexible circuits. The first piece of equipment I examined was a flexing endurance tester presented by YUASA SYSTEM Co. Ltd. (the company has no relation with the major battery manufacturer).
Previously, circuit manufacture engineers developed specific test equipment for flexing tests because there was no system available for testing. Machine manufacturers viewed this segment as a niche and decided that a limited market was not profitable. This could change. New demands in wearable electronics now include flexing modes, such as twisting and stretching. The new test machines are capable of conducting 10 kinds of flexing changes.
The second machine I examined was a migration tester. In a previous column, I wrote about silver migration from thick-film circuits and the headache this causes for the industry. Unfortunately, most circuit manufacturers don’t have suitable test equipment, and thick-film circuit manufacturers do not provide reliable numerical test data for their customers. The migration tester provides an insulation tester with moisture chamber, and circuit manufacturers can now provide reliability data to their customers.
The most radical piece of test equipment I viewed at the show was geared toward the furniture industry. This equipment is a large-sized pressure sensor array produced for bed and sofa furniture designers. The two kinds of pressure sensors include a piezo-type and a static-capacitance-type. The sensor module consistently measures pressure distribution. The circuits are built on a fabric material, placed between a sheet and mattress, and are required to have moisture permeability and elasticity. The manufacturer of the device is a flex circuit manufacturer. One of their engineers explained that they did not need to invest in any extra processes and completed the manufacturing utilizing the current facilities.
Headlines
1. Murata (device supplier in Japan) 7/16
Started producing the world smallest SAW component series for multi-band mobile equipment in volume (chip size: 0.9 x 0.7 mm).
2. Sony (electronics company in Japan) 7/30
Released Q1 performance. Revenue dropped 1.4% by y/y to 1926 billion yen. Net income has dropped 33% to 152 billion yen. CMOS sensor business was quite busy.
3. Kyushu University (Japan) 8/2
Developed a new type of organic EL with high quantum yield up to 40%. It will reduce the cost because it does not need to keep the organic layer very thin.
4. TSMC (semiconductor manufacturer in Taiwan) 8/2
Will hire another 3,000 employees in Taiwan, in spite of a slow market, and invest over 11 billion U.S. dollars in 2019.
5. Showa Denko (chemical company in Japan) 8/5
Developed a high-quality 6” SiC wafer for power semiconductor devices. The defect density became half.
6. Renesas (semiconductor manufacturer in Japan) 8/6
Released Q2 performance. Revenue dropped 5.3% by y/y to 192.6 billion yen. The production in August will be reduced for the balance of inventories.
7. Murata (device supplier in Japan) 8/5
Invested an additional 4.71 billion yen to expand the manufacturing capacity of multilayer ceramic capacitor (MLCC). The plant will be built in Iwami.
8. Tokyo Institute of Technology (Japan) 8/6
Developed a perovskite-type LED with a halogen molecule. It has a higher brightness at a low-voltage drive.
9. Tohoku University (Japan) 8/6
Succeeded in measuring the IQE of a perovskite-type, organic/inorganic hybrid semiconductor (CH3NH3PbBr3). It depends on the amount of CH3NH3.
10. Mitsubishi Electric (electric and electronics company in Japan) 8/7
Developed a new thermal diode IR image sensor “MelDIR” with a small package (19.5 x 13.5 x 9.5 mm) for security cameras. It detects 0.1°C changes.
11. Toshiba Memory (semiconductor manufacturer in Japan) 8/8
Developed a compact-size (14 x 18 x 1.4 mm), removable PCle/NVMe memory “XFMEXPRESSS” for ultramobiles.
Dominique K. Numakura is the managing director of DKN Research LLC. Contact haverhill@dknreseach.com for further information and news.
More Columns from EPTE Newsletter
EPTE Newsletter: Travel to Japan During COVIDEPTE Newsletter: A New COVID Surge in Taiwan?
EPTE Newsletter: COVID-19 PCR Test in Japan
EPTE Newsletter: Japan Failing in Vaccine Distribution
EPTE Newsletter: A Long Trip to the U.S.
EPTE Newsletter: Ten Years After Fukushima
EPTE Newsletter: Taiwan Releases 2020 PCB Production Numbers
EPTE Newsletter: The Printed Circuit Industry in China