-
- News
- Books
Featured Books
- smt007 Magazine
Latest Issues
Current IssueSupply Chain Strategies
A successful brand is built on strong customer relationships—anchored by a well-orchestrated supply chain at its core. This month, we look at how managing your supply chain directly influences customer perception.
What's Your Sweet Spot?
Are you in a niche that’s growing or shrinking? Is it time to reassess and refocus? We spotlight companies thriving by redefining or reinforcing their niche. What are their insights?
Moving Forward With Confidence
In this issue, we focus on sales and quoting, workforce training, new IPC leadership in the U.S. and Canada, the effects of tariffs, CFX standards, and much more—all designed to provide perspective as you move through the cloud bank of today's shifting economic market.
- Articles
- Columns
- Links
- Media kit
||| MENU - smt007 Magazine
Estimated reading time: 3 minutes
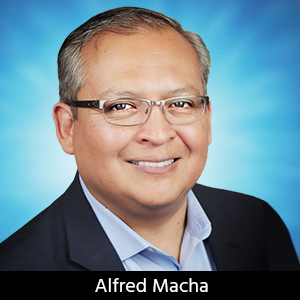
Operational Excellence: Becoming the Preferred Supplier, Phase 3—Re-engineer Your Quality System
The final phase of becoming a preferred supplier is to apply a business process re-engineer approach to your quality system. Before you start with this phase, the company should have implemented Phase 1 and Phase 2, which are focused on changing its leadership mentality to embrace LEAN Six Sigma and the pillars of operational excellence. It's paramount to have the right mindset before you re-engineer your quality system.
Most organizations build their quality systems for compliance to ISO 9001 or industry-specific standards, such as AS9100, ISO 13485, TL 9000, or TS 16949. It’s important to maintain these certifications to reassure existing and new customers that the manufacturing facility has implemented quality systems compliant to a recognized quality management standard. However, a mistake that is often made is to develop procedures and a structure solely focused on passing registration and surveillance audits to maintain these certifications.
The business objective when implementing a quality management system is to develop closed-loop systems and practical procedures that enable employees to manufacture and consistently deliver quality products on time to customers. The quality management system certifications should not be your end goal; customer excellence should be the goal of an effective quality system.
ISO provides valuable guidelines on implementing quality management systems to the various standards. One document that every manufacturing leadership team should read is "Quality Management Principles" from the International Organization for Standardization (ISO) [1]. This document delivers practical information in establishing the fundamentals of a quality management system, including:
- Customer focus
- Leadership
- Engagement of people
- Process approach
- Improvement
- Evidence-based decision making
- Relationship management
These principles provide the basis of how an effective quality management system should be developed. The guidelines in the next paragraphs provide supplementary guidelines to these quality management principles. These are five practical and proven approaches that can help you re-engineer your quality management system for customer excellence.
1. Lowest Common Denominator: Less Is More
I once audited a printed circuit board assembly factory and asked for their document listing. The listing was impressive and had over 500 procedures that had been created over 15 years. These procedures had comprehensive instructions and technical information that gave the impression of assurance. However, as I asked operators and technicians in the production line to explain their process steps and point out the steps of the procedure, it was quickly apparent that they knew their processes well but were not familiar with the respective procedures. The process engineer knew where to find the information in the procedure, but the end user—the operator—was not so sure. To address this common issue, some companies have created work instructions as the least common denominator of information that every production line personnel should master. These companies have also created technical documents that support these work instructions for trouble-shooting and problem-solving purposes where engineering is involved.
As you evaluate your current quality systems, put yourself in the shoes of the end user, and create simple-to-read, value-added instructions. Also, your supporting technical documents should not be lengthy. Keep the most essential and useful information available to support your operations.
2. Redefine Your Training Philosophy
Is your training program built to satisfy the ISO auditor? Or is it built to elevate your company’s performance into a world-class organization? Training can be a controversial topic in organizations. Defining the return on investment on hours trained cannot always be quantified in accounting. How many hours can you let employees off the production line to invest in training? Is your training program ISO-compliant? Does the current training material provide value to your operations? Those are questions that are discussed in every organization.
Here is an approach that companies should consider taking. Don’t make training a burden to operations; instead, make it part of the operations process. Training can be incorporated as part of your day-to-day operations and a deliverable for every employee during the day. Design a training system where your production supervisors, process engineers, or area trainers can allocate a small percentage of the time each day to carry out on-the-job training. The key component here is to make it simple so that you cover a small element of knowledge each day—possibly 5 to 10 minutes with each operator. During the year, you will have covered at least 1,200 minutes of one-on-one training per operator, which equates to 20 hours of essential, practical on-the-job training. The goal should be to bring the competence and knowledge level of each employee to a higher level on a daily basis.
This is an excerpt of Alfred's column that appears in the August 2019 issue of SMT007 Magazine. To read the entire column, click here.
More Columns from Operational Excellence
Operational Excellence: Strengthen Your Design Transfer Process With Agile NPIOperational Excellence: Redefine Recruiting to Attract and Hire the Right Talent
Operational Excellence: Process Effectiveness Qualification
Operational Excellence: Working Remotely–Redesign Your Information Systems
Operational Excellence: Sharpening Your Organization’s Competencies
Operational Excellence: Hiring and Retaining Top Employees
Operational Excellence: Update Your Business Contingency Plan
Operational Excellence: The Gemba Transformation of Manufacturing With AI