-
-
News
News Highlights
- Books
Featured Books
- smt007 Magazine
Latest Issues
Current IssueWhat's Your Sweet Spot?
Are you in a niche that’s growing or shrinking? Is it time to reassess and refocus? We spotlight companies thriving by redefining or reinforcing their niche. What are their insights?
Moving Forward With Confidence
In this issue, we focus on sales and quoting, workforce training, new IPC leadership in the U.S. and Canada, the effects of tariffs, CFX standards, and much more—all designed to provide perspective as you move through the cloud bank of today's shifting economic market.
Intelligent Test and Inspection
Are you ready to explore the cutting-edge advancements shaping the electronics manufacturing industry? The May 2025 issue of SMT007 Magazine is packed with insights, innovations, and expert perspectives that you won’t want to miss.
- Articles
- Columns
- Links
- Media kit
||| MENU - smt007 Magazine
Estimated reading time: 4 minutes
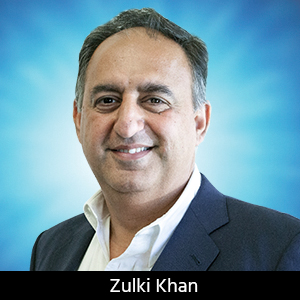
Zulki’s PCB Nuggets: Get a Handle on Glob Top Epoxies
In my last column, I talked about protecting both the bare die and associated wire bonding as a major part of today’s PCB microelectronics assembly. I also discussed two die protection methodologies—glob top and lid and cover—as well as a glob top sub-method known as dam and fill. This column will further describe how you can get a handle on glob top epoxies.
Most often, glob top is the prevalent method EMS providers use today. However, the most important point to be made about glob top is the fact that multiple manufacturers are producing different glob top epoxies. And within each manufacturer, there are numerous types of epoxies being produced. Another key point is that EMS providers and contract manufacturers generally are the ones deciding on the kind of epoxy to use.
However, one has to keep in mind that electronic components continue to be increasingly minuscule, and product reliability is at a premium. Therefore, it’s prudent on the OEM customer side to gain a basic understanding of the key differences among these epoxies because they play a vital role in the levels of die protection integrity and reliability that customers expect.
Some of the key aspects to be aware of include:
- Epoxy characteristics
- Curing conditions
- Viscosity
- Glass-transition temperature (Tg)
Epoxy is composed of different characteristics or elements. Some may have adhesive characteristics; others may have conductive thermal characteristics or non-conductive electrical characteristics, depending on the applications that are being used.
Moreover, a general-purpose epoxy should be able to adapt to a variety of different temperature ranges to work with different substrates and surface finishes. A good epoxy should display low thermal stress during temperature cycling. This means taking a board or substrate to very high and low levels of temperature to ensure they are reliable at a wide range of temperature cycles.
Curing depends on an epoxy's application. Curing means the epoxy goes through a cycle of a specific temperature range, which is of a certain time and at a certain interval. Some epoxies are cured at lower temperatures and others at higher temperatures. Some are cured in minutes, while others take 1.5–2 hours. For example, some epoxies take 20 minutes to cure at 120°C while others take five seconds at 150°C. Again, epoxy curing depends on the die-attach application as well as a particular epoxy’s characteristics.
Viscosity comes into play for multiple reasons regarding die attach or wire bonding (not so much for wire bonding, but definitely for die attach). Process engineering on a PCB microelectronics assembly line should closely inspect viscosity. It is one of the most important epoxy characteristics that will either make your project successful or a failure.
Different applications require various viscosities, so viscosity is very important. If the viscosity isn't right for the application, it could cause problems. For instance, if it's too thin, it could leach out to the outside periphery of the die, creating unstable die-attach joints before wire bonding can be performed. If it's too thick, it might create non-optimal flashpoint with the surface. This means it's overly lifted from the surface of the substrate on a PCB to the die itself, creating possibilities for voids within the epoxy.
Dispensing the epoxy is yet another factor to keep in mind. The accuracy of the epoxy lines a dispenser makes underneath or around the die that's to be attached plays an important role. Dispensing methods are equally as important. There are different dispensing pumps, needles, and syringes, and each methodology should be considered carefully to assure the die-attach application.
Also, consider tack time. Die-attach epoxy can get dried up unless properly applied. When epoxy is dispensed, there is a distinct amount of time allowed to attach a die or else it will dry too quickly, resulting in a non-optimal die attach for a given application, thereby creating field failures.
As for Tg, it is important to know that high glass transition epoxy compounds are critical to the adhesive selection for higher-temperature applications. These products have superior mechanical, thermal, and electrical properties than lower Tg materials at high temperatures. Thus, you also have to consider Tg as a major factor when choosing the right epoxy for your given application.
For example, an application may require a flexible epoxy; therefore, a low Tg or a level below 0°C is acceptable. Other applications may require the strongest possible epoxy physical properties. In cases like these, a high Tg is fine. In turn, the high Tg uses high strength, compression, and tension epoxy properties.
One key point to make when selecting epoxies for microelectronics is that Tg should be carefully considered for the substrate temperature operating levels versus the die in terms of the ranges at which these epoxies can be cured. OEM customers should get a handle on the various types of die-attach epoxies available so they can ensure it’s a highly reliable product as it goes through an effective PCB microelectronics assembly line.
Zulki Khan is the president and founder of NexLogic Technologies Inc.
More Columns from Zulki's PCB Nuggets
Zulki's PCB Nuggets: Cleanliness is Next to ReliabilityZulki’s PCB Nuggets: Thermal Compression Bonding for Extra Fine Pitch Flip Chips
Zulki’s PCB Nuggets: WBAN Steps Into PCB Microelectronics Assembly
Zulki’s PCB Nuggets: Photonics Comes to PCB Microelectronics Assembly
Zulki’s PCB Nuggets: Sub-Micron Die Bonding—Don’t Be Misled by Five Micron Placement Standard
Zulki’s PCB Nuggets: Meet the New Player in PCB Microelectronics Assembly—Interposers
Zulki’s PCB Nuggets: How Effective Is Your PCB Microelectronics Assembly?
Zulki’s PCB Nuggets: Five Key Benefits for Onshoring PCB Microelectronics Assembly