-
- News
- Books
Featured Books
- smt007 Magazine
Latest Issues
Current IssueSupply Chain Strategies
A successful brand is built on strong customer relationships—anchored by a well-orchestrated supply chain at its core. This month, we look at how managing your supply chain directly influences customer perception.
What's Your Sweet Spot?
Are you in a niche that’s growing or shrinking? Is it time to reassess and refocus? We spotlight companies thriving by redefining or reinforcing their niche. What are their insights?
Moving Forward With Confidence
In this issue, we focus on sales and quoting, workforce training, new IPC leadership in the U.S. and Canada, the effects of tariffs, CFX standards, and much more—all designed to provide perspective as you move through the cloud bank of today's shifting economic market.
- Articles
- Columns
- Links
- Media kit
||| MENU - smt007 Magazine
Estimated reading time: 5 minutes
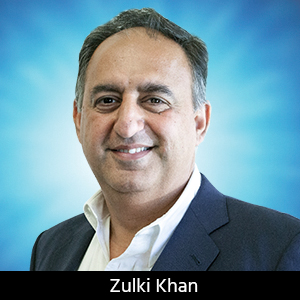
Zulki's PCB Nuggets: Multi-tier Wire Bonding—Diving Into PCB Microelectronics
Ideally, OEMs should crave as much functionality as possible out of a chip or die. The chipmaker has done its job to produce ultra-functionality for a given chip generation via its design and manufacturing. But would you believe that there’s still more functionality to glean out of that chip? That’s where multi-tier wire-bonding steps into PCB microelectronics assembly to do exactly that—extract more functionality out of that already powerful chip.
But there’s more. Multi-tier wire bonding also gives OEMs the opportunity to reduce the PCB’s size, meaning less cost, yet more value. Instead of using multiple dies and single wire bonding, a single die can be combined with multi-tier bonding to capture that extra functionality; at the same time, this can reduce the number of dies required for a given application, thus decreasing the PCB’s size.
As the name implies, multi-tier wire bonding involves several levels of wire bonding beyond the single level of wire bonding, which is traditionally used in semiconductor and/or PCB microelectronics assembly. Here, you have two, three, and four levels of wire bonding, in some cases, called stacked wire bonding (Figures 1 and 2). Also, multi-tier wire bonding offers OEMs a solution when the number of inputs/outputs (I/Os) are far beyond the traditional ones that are used in the single wire-bonding application.
Background
Flip-chip technology has historically had an advantage over single wire bonding in terms of the number of I/Os, which represent the communication system for transmitting and receiving signals to and from devices. For a given IC chip size, the possible number of I/Os depends on pad size, pad pitch, and pad arrangement.
A flip-chip process usually has an array of prepared channels containing a number of I/Os, which are conventionally more than a peripheral arrangement of pads in wire bonding for a specific chip size. But this process of I/O is limited in wire bonding due to pad size, pad pitch, bonding tool size, and thickness of the wire to be used for wire bonding. Considering that silicon cost is relatively high, OEMs obviously favor the idea of getting more I/O from a chip.
Tier wire bonding comes in at this point. The advantages are not having to compromise pad size or pitch. Multi-tier bonding was developed to handle high lead count packages, thereby extracting a lot more functionality from the same die.
Getting More Detailed
Capillary design in a wire-bonding machine is among several important considerations for effective, tiered wire bonding. The capillary is a tiny nozzle that feeds the wire to make connections with the bare die. The design of the capillary incorporates the hole size, tip shape, and tip length to be considered proper; otherwise, accurate wire bonding would be difficult. In effect, the wire uses a capillary to connect the thin wire to the bonding pads per the design process engineering finalizes. Figure 3 shows different capillary sizes and shapes for different applications.
In multi-tier wire bonding, the different rows of wires are isolated by maintaining a different loop height for each row. This creates a vertical gap between the rows of wire from the first row to the second, third, and fourth. Multi-tier wire bonding increases the capacity and the capability of a bare die. If wire bonding is double-stacked, the I/O capacity is doubled by adding the second set of wire-bond pads. If you go on to third-tier wire bonding, you increase the capacity of the I/Os by three times. The die is the same, so you can extract more functionality out of the same die.
Pitfalls and Challenges
So far, so good as far as the benefits of multi-tier wire bonding. Now, we have to face some realities. First, wire-bonder precision is especially important. You have to ensure that the first row of wire bonding is the lowest in height, the second a little bit higher, the third a tad higher, and the fourth has to be the highest.
A third- and quad-tier wire-bonding machine demands a well-trained operator, top-notch precision and process control, and exact calculations of and computational knowledge of wire size and bonder restrictions, among other key requirements. Also, wire looping has to be correctly calculated. If it’s not, wiring is prone to sag, and the result is the creation of shorts with other rows of wires.
For example, if the third tier of wire bonding is incorrectly performed, it will sag, thus creating the possibility of a short with the second tier of wire bonding. Reworking this problem is difficult; wire bonding can only be re-done two or maybe three times because the pad is worn down after those two or three rework attempts.
Wire pull testing (WPT) for wire-bond strength and quality also presents a challenge; it involves applying upward force under the wire to be tested. WPT is applied on every tier. If two to three tiers are tested properly, then it becomes a challenge to test without damaging certain wire tiers. Therefore, savvy, expert technicians are top requirements to ensure effective WPT. Each tier of wires is to be pull tested before the next tier is bonded.
Summary
Multi-tier wire bonding is one PCB microelectronics technology that will gain greater interest for newer, smaller OEM products across multiple industries. For example, greater functionality at a lower cost is much sought after in medical electronics, IoT devices, wearables, and other portable gear.
Knowledgeable OEMs and product designers will account for several considerations when seeking guidance for multi-tier wire bonding, including optimal design and the size of the pad. Further, pad pitch becomes important, as does the loop height and length of the wires. The staggering pitch is also important, which is basically the pitch from one row to the second to the third, and so on.
In addition, experienced EMS provider process engineers have to calculate how far to design a second set of wire rows to be wire bonded from the first row, etc. Also, the landing pad of the second bond has to be done very critically. Therefore, multi-tier wire bonding offers considerable advantages, but a proper plan and its correct execution are critical factors, as well.
Zulki Khan is the president and founder of NexLogic Technologies Inc.
More Columns from Zulki's PCB Nuggets
Zulki's PCB Nuggets: Cleanliness is Next to ReliabilityZulki’s PCB Nuggets: Thermal Compression Bonding for Extra Fine Pitch Flip Chips
Zulki’s PCB Nuggets: WBAN Steps Into PCB Microelectronics Assembly
Zulki’s PCB Nuggets: Photonics Comes to PCB Microelectronics Assembly
Zulki’s PCB Nuggets: Sub-Micron Die Bonding—Don’t Be Misled by Five Micron Placement Standard
Zulki’s PCB Nuggets: Meet the New Player in PCB Microelectronics Assembly—Interposers
Zulki’s PCB Nuggets: How Effective Is Your PCB Microelectronics Assembly?
Zulki’s PCB Nuggets: Five Key Benefits for Onshoring PCB Microelectronics Assembly