-
- News
- Books
Featured Books
- design007 Magazine
Latest Issues
Current IssueProper Floor Planning
Floor planning decisions can make or break performance, manufacturability, and timelines. This month’s contributors weigh in with their best practices for proper floor planning and specific strategies to get it right.
Showing Some Constraint
A strong design constraint strategy carefully balances a wide range of electrical and manufacturing trade-offs. This month, we explore the key requirements, common challenges, and best practices behind building an effective constraint strategy.
All About That Route
Most designers favor manual routing, but today's interactive autorouters may be changing designers' minds by allowing users more direct control. In this issue, our expert contributors discuss a variety of manual and autorouting strategies.
- Articles
- Columns
- Links
- Media kit
||| MENU - design007 Magazine
Estimated reading time: 7 minutes
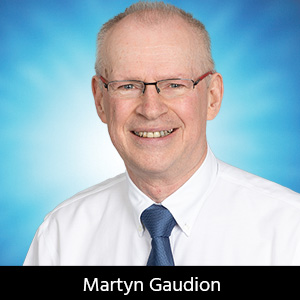
The Pulse: Communicating Materials From Design to PCB Fabrication
Designer and fabricator communication—especially for high-speed PCBs—should be a bidirectional “thing.” It is so easy for a designer to say, “Just build this,” and hand over a challenging design to a fabricator who could have performed better with some preliminary conversation or dialog before placing the order.
Materials always matter when it comes to PCB fabrication; however, as designs progress and industry changes and morphs, the PCB materials or specific material characteristics that impact the day-to-day lives of designers, fabricators, procurement specialists, and PCB technologists change. Characteristics that could safely be ignored in the past may now creep up and trip you over—catching you unaware—and yet other characteristics that may have been critical on legacy products may only have a second order influence on your PCB specification and the chances of it performing as expected.
Depending on design requirements, a designer has a choice to entrust material specification to their fabricator or to lock down the materials far more rigidly before ordering or perhaps somewhere in between where only critical layers are deployed with mandated materials (Figures 1 and 2).
Important in guiding you through this are the specialists in the PCB base material supply industry, which has transformed from an industry with only a selected handful of material choices to a whole range of suppliers providing a complete gamut of materials with a range of purpose. This adds complexity and perhaps confusion as designers, fabricators, procurement specialists, and technologists work together to select appropriate base materials. Most material suppliers will have OEM teams whose aim is to guide you towards the correct base material or family of materials.
Choosing Materials
Knowing what you need is always a good place to start. The choices seem endless. ?High Tg or low Tg? Halogen-free? High speed? Controlled impedance? Is insertion loss critical? Rough or smooth copper? Reliability and susceptibility to thermal cycling and thermal stress? Expected lifetime of the product? Will the PCB go in a short-lived consumer product, a satellite or undersea cable, or automotive with harsh environments and be highly-price sensitive but with a lifespan midway between mobile phone and aerospace applications? Will the PCB be laser drilled? Sequential laminated or HDI and subject to repeated press cycles? Once designed, will the board be produced in low quantities by one fabricator, or will it ramp up and be sourced from a volume fabricator in another country? Maybe the OEM will handle procurement directly or—as often happens—the procurement will be outsourced to a specialist broker. What happens to the carefully crafted materials specification as the specification wings its way across the supply chain?
Cost is almost always there to intervene, and getting the PCB specification correct for the specific application—neither over- or under-specified—is important if you wish to minimise the cost for a specific application.
Conversations with technical buyers often raise the following question: “When I send out a PCB specification for quotation or purchase PCBs from multiple suppliers, why is the construction of the stackup different from the same stack specification?” In more than one case, a technical buyer expressed frustration that the same PCB repeatedly purchased from the same supplier was realised with different material stackups. The question is, “Does this matter?” And the answer is sometimes yes, sometimes no, and sometimes maybe; however, the more the procurement team knows of the ultimate application, the better they are able to specify the PCB to an appropriate level.
Looking at two extremes of PCB specification, here are some examples of the requirements, from simple to very demanding, that can be asked of a design. At the lowest end, the PCB could simply be a carrier for low-power LEDs for an indicator in machine status lights; the PCB may be wired into the machine, and the PCB fitted with screws to a backplate. Thickness isn’t critical—neither is power handling—and the environmental stress on the board could be pretty benign, too. Likewise, the volume produced may be low, so, really, all that matters is that the board be the correct X and Y dimensions, have holes in the correct place, and the correct data imaged on the appropriate layer. It might need to be lead-free and halogen-free to comply with environmental regulations and minimal specifications required.
At the highest end, a large aerospace PCB will need to be built by a fabricator with all the correct approvals and likely from material which is certified for the job, too. The layer stackup will be tightly controlled, and any changes will have to be thoroughly investigated and signed off by the appropriate parties.
In between these two extremes, there is far more space for PCB technologists and procurement teams to make intelligent decisions to gain the best commercial advantage, and this does not necessarily mean just a price negotiation. A well-specified PCB will help a fabricator get a better yield with appropriately priced materials, there will be less waste in the process, and everyone wins. Good communication can allow businesses to work together to maximise profits and to minimise scrap and waste. Here’s a sample checklist:
- Speed: Low, medium, high, or ultra-high
- Volume: Low, medium, or high
- PCB size: Small or large
- Traces: Short, long, or high-speed (Shorter traces make life easier for high-speed signals for a given material type.)
- Layer count
- Sequential lamination
- HDI
- Back-drilled
- End-use: Consumer, industrial, automotive, or aerospace
- Single supplier or multiple sourced
- Laser or conventional drilled
- Environmental/regulatory requirements
Taking all of the above into account, you may choose to band the type of specification you provide from a low-end “layer count/thickness” to a medium “layer count/thickness/IPC slash sheet material description” to a high medium “layer count/thickness/generic material family/impedance requirements” to a high “layer count, specific build, material vendor, glass style, specific base material, foil type—treatment type” depending on how “nailed down” you need the specification to be for the specific application.
Understanding Materials
Material is fascinating, and the more you understand, the more you can work with the characteristics rather than fighting with them. In previous decades, rarely did designers have to concern themselves with such matters as glass style and resin content, but here is an example of just how this has changed.
Let’s take the case of spread glass cloth. You may be aware of a property called fibre weave effect, which frustrates high-speed designers. This stems from the fact that glass cloth and epoxy resin have widely different electrical properties.
Park that in your mind and consider something unrelated and from a completely different arena: laser drilling. When drill companies developed laser drilling for PCBs the composite nature of base materials limited the precision of laser drilling techniques. You can imagine why. You are trying to accurately ablate holes in a material, which is a composite of relatively easy to remove polymer and woven e-glass cloth (Figure 3)—not the easiest of materials to ablate. It must be like mechanically drilling into a block wall with steel rebar inserts. The lack of consistency would give even the best mechanical drill a tough time.
On the PCB front, the material suppliers innovated by developing flat or spread glass cloth; this modified the traditional warp and woof (weft in the U.K.) of the fibre and mostly eliminated the gaps in the cloth where the threads cross over (Figure 4).
This is achieved by mechanical or water jet blasting sometimes combined with threads that are “low twist” (i.e., the glass yarn has fewer twists per metre, making it easier to flatten out). This step-function improvement in materials for laser drilling has a hidden side effect. The more even lay of the glass also helps to eliminate the variations of dielectric constant that used to be experienced by signals transiting along traces, which ran predominantly over fibre or predominantly over resin. The win for drilling presented SI engineers with a win for signal integrity too. (There is a “but” coming, which isn’t a problem, but is something you should be aware of.)
A third benefit of flat glass is that the cloth lies flatter and gives overall more control over finished thickness and thickness variation (here comes the “but”), but a benefit of the “old school” glass styles with the apertures between the crossover of the warp and woof of the cloth is that the apertures allow the easy passage of resin from one side of the cloth to the other—so more of the total resin content on top and below the cloth could flow from one side or the other into the gaps between the traces to ensure a reliable lamination process and minimal risk of resin starvation.
For the same resin content, flat glass may prevent the resin flowing across the glass boundary, so before you change glass styles, you should consult with your material supplier and take advice on the resin content requirements for successful lamination with flat glass. This is not a problem with the material; it simply means that when using the newer material styles, you need to ensure you understand what questions you need to ask to make sure your material supplier can help you specify the optimum build materials.
Having a material and stackup discussion before submitting the design or—even better—before starting to lay out the board is critical for complex designs. Moving stackup design as early in the process as possible gives both designers and fabricators time to discuss the trade-offs and benefits of different material choices.
This column originally appeared in the May issue of Design007 Magazine.
More Columns from The Pulse
The Pulse: Design Constraints for the Next GenerationThe Pulse: Ultra Upgrade Unknowns—What’s Coming for UHDI?
The Pulse: Commonsense Cost Cutting
The Pulse: Overconstraining: Short, Slim, and Smooth
The Pulse: Drilling Down on Documentation
The Pulse: New Designer’s (Partial) Guide to Fabrication
The Pulse: Simplest Stackups Specified
The Pulse: Rough Roughness Reasoning