-
- News
- Books
Featured Books
- design007 Magazine
Latest Issues
Current IssueProper Floor Planning
Floor planning decisions can make or break performance, manufacturability, and timelines. This month’s contributors weigh in with their best practices for proper floor planning and specific strategies to get it right.
Showing Some Constraint
A strong design constraint strategy carefully balances a wide range of electrical and manufacturing trade-offs. This month, we explore the key requirements, common challenges, and best practices behind building an effective constraint strategy.
All About That Route
Most designers favor manual routing, but today's interactive autorouters may be changing designers' minds by allowing users more direct control. In this issue, our expert contributors discuss a variety of manual and autorouting strategies.
- Articles
- Columns
- Links
- Media kit
||| MENU - design007 Magazine
Estimated reading time: 6 minutes
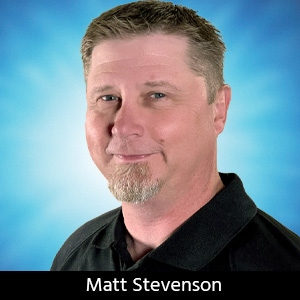
Connect the Dots: The Power of Forward Thinking
Innovation comes in many forms and from more places these days. Last year, the staff of Popular Science locked themselves in a room and came up with its annual list of 100 greatest innovations. These technological advances will shape how we live and work in the coming years. Included were products like Omrom’s HeartGuide, HTC’s VIVE Pro Eye, and Pro Display XDR by Apple, as well as the national rollout of 5G cellular from all four mobile carriers.
Breakthroughs result when visionary individuals and organizations identify needs that are not being served, platforms that can be improved, or entirely new products capable of transforming daily life. What do these electronic devices and an industry-wide technology shift have in common? They are all innovative, and they all contain PCBs.
Turning Visionary Ideas Into Innovative Products
Whether it’s a new electronic device or advancement of broader technology infrastructure, moving from idea to innovation requires processes—the journey from concept to design to prototype—and manufacturing. Bringing innovation to the market requires many skills across multiple disciplines, all working together.
From mechanical and electrical engineering to sales and marketing, a team needs to have all these resources available to them to be successful. PCBs are at the heart of these products and product innovation; designing, prototyping, and manufacturing them is vital to success.
To the uninitiated, PCB design may seem like a rigid, by-the-book process, but It’s not. Because it takes creativity to turn a concept into design, PCB design is very much an art form. Granted, boards aren’t quite the same as blank canvasses, and there’s nothing artsy-sounding about schematics or a bill of materials or documentation. PCB design is a world filled with limits, tolerances, and parameters—in other words, rules. But, like in “The Matrix,” some of those rules can be bent and others broken.
When you focus on design as an opportunity to be creative, rather than a task standing between you and production, you put yourself in a position to better fulfill the promise of innovation.
Let’s start with components. The placement and use of components aren’t just pragmatic; there is also an element of creativity in their use. There is no single right way to place them, but there is something unspoken about the elegance and aesthetic beauty of well-arranged components. It’s important to remember, and this is where “The Matrix’s” rules cannot be broken; how you orient and organize components will heavily influence the manufacturability of design and, ultimately, the functionality of your finished board (Figure 1).
Figure 1: Components.
Pro Design Tips:
- Orient similar components to facilitate efficient and error-free soldering
- Do not place components on the solder side of a board that would sit behind through-hole components; your assembly shop will tell you how much room they need
- Organize through-hole and surface-mount components to minimize assembly steps
- Avoid components that will give you heating issues when the board is in use or take steps to control or remove that heat
Next, consider routing. Almost every piece of PCB design software has an auto-router feature that can be useful in a lot of situations, but when you’re designing something brand new, you can benefit from taking over the controls yourself.
Leave the auto-router in charge, and the results can be asymmetrical, even look and feel messy. These configurations are not easily manufactured and can be lacking when it comes to performance. It’s like a pilot who doesn’t know the destination of the flight. Use this tool as a complement to your routing efforts—not a replacement for you.
If you have time, hand route the entire design; it will look more professional, work more efficiently, and be easier to update if you must rework a section of the board. If you cannot avoid having to auto-route some of the board, hand route the critical traces yourself, and then auto route the remaining ones. In this capacity, the auto-router can help with schedule compression while also making the bulk of your non-critical connections. There will be some messy routing and too many vias—plus editing will be harder down the road—but you’ll have something to work with much sooner.
Innovation increasingly goes hand in hand with PCBs getting smaller. A multilayered PCB can offer requisite functionality if it occupies a small space in your device. If you have limited or no experience with multilayer board design, the prospect of an attempt can be daunting. Multilayer boards don’t have to be a hassle. Think of them as multiple single-layer boards stacked together.
Pro Design Tips:
- Become familiar with multilayer design tips and guidelines provided with your CAD tool
- Familiarize yourself with components, tolerances, and requirements unique to multilayer PCBs
- Make sure your design tool library is set up for multilayer boards
- Know your manufacturer’s requirements for multilayer designs
- Stay away from blind and buried vias unless you really need them
- Don’t hesitate to ask for help
To be considered an innovator—a profitable one, at least—it’s important that you’re first to market with your product. This presents a seemingly compelling reason to head straight for full production, but designing your PCB is just step one for ensuring its manufacturability and eventual functionality. Prototyping is the critical next step in the process, one that can make you more confident about your production runs.
Some feel prototyping costs too much, takes too much time, or must be outsourced abroad. Even if you are in a hurry, prototyping makes sense. It also doesn’t have to cost a lot or happen 5,000 miles away. We believe prototyping is vital to a smooth, successful production run. It cost-effectively validates manufacturability of design, helps avoid incredibly expensive mistakes during full production, creates more opportunities to innovate, and tests your boards for quality and durability.
Prototype fabrication services can vary, and if you are working on something cutting-edge, there are several critical elements to keep in mind. Many manufacturers offer a feasibility assessment of your design to ensure PCB manufacturability and viability. This can help you avoid costly and unnecessary iteration during the prototyping phase. Layout review may uncover expanded manufacturing needs, so don’t be afraid to ask questions and make sure your prototyping partner uses processes and equipment that match your desired speed of production and quality of the product (Figure 2).
Figure 2: DFM.
Once an acceptable prototype has been manufactured, assembled, and proven, your board moves on to full production and then assembly. At assembly, functional components for power regulation, I/O interfaces, and processing are connected with the wiring of your PCB. The resulting printed circuit assembly (PCA) will be key to end-product functionality.
In terms of time, money, and reputation, the cost of a do-over after assembly is more than at the design or prototyping phases—especially at higher volumes. A PCA with performance problems at this point could result in delayed order fulfillment, project cost overruns, or a competitor beating your product to market—a missed opportunity for innovation. That is why choosing your assembler wisely is so important. A reliable assembly partner will help you avoid costly failures associated with slipshod production, as well as defective and improperly installed components.
Moving your PCB design through prototyping, manufacturing, and assembly is the journey within the journey for product innovation. Every part of it is a continuous learning process that offers an opportunity for improvement. That’s what makes innovation both challenging and exciting.
Bob Tise is an engineer at Sunstone Circuits, and Matt Stevenson is the VP of sales and marketing at Sunstone Circuits. To read past columns or contact Tise and Stevenson, click here.
This column originally appeared in the June 2020 issue of Design007 Magazine.
More Columns from Connect the Dots
Connect the Dots: Sequential Lamination in HDI PCB ManufacturingConnect the Dots: The Future of PCB Design and Manufacturing
Connect the Dots: Proactive Controlled Impedance
Connect the Dots: Involving Manufacturers Earlier Prevents Downstream Issues
Connect the Dots: Stop Killing Your Yield—The Hidden Cost of Design Oversights
Connect the Dots: Designing for Reality—Routing, Final Fab, and QC
Connect the Dots: Designing for Reality—Surface Finish
Connect the Dots: Designing for Reality—Solder Mask and Legend