-
-
News
News Highlights
- Books
Featured Books
- pcb007 Magazine
Latest Issues
Current IssueSales: From Pitch to PO
From the first cold call to finally receiving that first purchase order, the July PCB007 Magazine breaks down some critical parts of the sales stack. To up your sales game, read on!
The Hole Truth: Via Integrity in an HDI World
From the drilled hole to registration across multiple sequential lamination cycles, to the quality of your copper plating, via reliability in an HDI world is becoming an ever-greater challenge. This month we look at “The Hole Truth,” from creating the “perfect” via to how you can assure via quality and reliability, the first time, every time.
In Pursuit of Perfection: Defect Reduction
For bare PCB board fabrication, defect reduction is a critical aspect of a company's bottom line profitability. In this issue, we examine how imaging, etching, and plating processes can provide information and insight into reducing defects and increasing yields.
- Articles
- Columns
- Links
- Media kit
||| MENU - pcb007 Magazine
Estimated reading time: 5 minutes
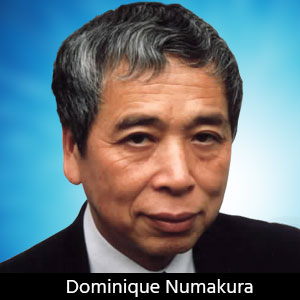
EPTE Newsletter: Transparent Flexible Circuits
When DuPont developed the heat-resistant polyimide film Kapton in the 1960s, there was no large-volume application. Now, DuPont has developed a new circuit concept for flexible circuits, but the company did not have a business plan for the products. The company developed and commercialized the copper laminate Pyralux as the raw material of reliable flexible circuits and rigid-flex for aerospace applications. DuPont also developed basic constructions of the circuit with process conditions. When DuPont promoted Pyralux, the company provided the technical information as the design guide and processing manual. The business strategy was successful, and DuPont enjoyed good profits. The basic construction of the flexible circuits was almost fixed.
The industry has grown significantly in the 1980s and 1990s, especially in consumer electronics, such as personal computers and cameras. The flexible circuit segment made another expansion in the 21st century with the growth of cellphones/smartphones. The industry expanded and became larger during the last four decades. However, the basic construction of the circuits has not changed. Kapton® is still a major material as the base film of flexible circuits. The circuit density rose, and via hole size shrank. Most of the flexible circuits retain the Kapton color. Few mobile device manufacturers seem to dislike the Kapton color, and they asked flexible circuit manufacturers to paint the circuits black, but customers don’t request changes to the base polyimide films.
On the other hand, new demands for the flexible circuits have appeared in wearable devices and medical electronics, which require abnormal properties that cannot be satisfied by traditional polyimide base flexible circuits; one of these requirements is transparency. Previously, it was not very critical for the applications; both customers and manufacturers of the flexible circuits did not pay attention to performance. However, the transparency of the circuits is critical for optical sensors and lighting devices. Therefore, the requirement about transparent circuit has become very keen (Figure 1).
Almost five years ago, a material supplier in Japan commercialized a clear polyimide film as the base material of heat-resistant flexible circuits. However, the etching companies did not consume the new polyimide films directly because they could not make the circuits without copper foils. Therefore, laminate manufacturers developed copper laminates using the transparent polyimide film. Unfortunately, the customers were not very happy about the properties of the copper laminates because the glue layer reduced the transparency remarkably, and the glue materials were not very transparent.
Next, it was our turn. We developed a series of flexible copper laminates without a glue layer using plating processes. Several flexible circuit manufacturers could make the circuits with the new laminate with their existing etching process, but they were not very positive about expanding that business. They needed coverlay material to finish the flexible circuits. I asked material manufacturers to develop film base coverlay or screen-printable coverlay ink, and they did.
On the other hand, device manufacturers have been demanding transparent conductors for optical applications. It was a hard requirement for traditional flex circuit manufacturers, so we had to change their minds. We had several choices to reach the goal. The first candidate was an indium tin oxide (ITO) film, but it did not have good flexibility. The second candidate was transparent conductive ink made of an organic molecule, but it was not stable at high-temperature processes, such as soldering. The third candidate was a silver nanowire ink, which was difficult to find appropriate process conditions, and its high cost was another headache. These candidates have larger conductor resistance than 100 ohm-cm. This conductivity restricts applicable areas.
The fourth candidate was a finely etched mesh pattern made of thin copper layer. In this case, the conductivities have a trade-off relationship against transparency. And the transparency depends on the fine pattern etching capabilities of the circuit manufacturers. Currently, we do not have a perfect solution for transparent conductors. We have to make appropriate balances between the materials and performances.
Our new customers sometimes request crazy properties because they do not know standard design rules. Recently, some wearable device manufacturers have asked for elastic, transparent, and heat-resistant flexible circuits, and it’s almost impossible to satisfy all of the requirements. However, one of our colleague companies developed silicone rubber base flexible circuits with screen-printable silver inks. The base materials are elastic, transparent, and heat-resistant, and the customer’s requirements were 80% satisfied.
There is no limit to customers’ requirements, especially the medical device manufacturers, who have been generating ultimate properties for the flexible circuits. Circuit manufacturers have been developing a broad range of materials with various manufacturing processes, and they do not satisfy merely 10% of the requirements, but 80–90%. Additional design ideas will help the requirement satisfaction reach 100%. We will be very happy to share our experiences regarding these new demands.
Headlines
1. Sharp (electronics company in Japan)
Demonstrated the secondary battery system “JH-WBPB150” for home use (capacity: 6.5 kWh; price: 2.6 million yen).
2. JPEA (organization of solar generators in Japan)
Reported that 80% of home solar generator holders utilized self-operation systems during the power outage caused by Typhoon #1915 in September.
3. Toyota (automobile manufacturer in Japan)
Will introduce a flexible organic EL display for the next-generation concept car “LQ.”
4. Panasonic (electronics company in Japan)
Co-developed a volume production process to produce chemical chips on a glass substrate with the Institute of Microchemical Technology.
5. Tokyo University (Japan)
Produced wafers of organic semiconductors by using a simple printing process, which could be a valuable step-up to make organic transistors.
6. Sharp (electronics company in Japan)
Co-developed a 30” foldable, flexible OLED display with NHK, which can be put in a 4-cm diameter pipe (weight: 100 grams).
7. SK Hynix (semiconductor manufacturer in Korea)
Opened an R&D center of C-MOS Sensor devices in Hamamatsucho, Tokyo, to catch up with the growing market.
8. AIST (R&D organization in Japan)
Improved the resolution of EDS element analysis in SEM system more than two orders to determine the 3D structure of carbon nanotube molecules.
9. Hokkaido University and Bsan University (Japan and Korea)
Made the chemical reaction process of SrCoOx, the basic material of next-generation memory devices.
10. Touchence (device manufacturer in Japan)
Agreed to co-develop finger type touch sensors using MEMS manufacturing processes with Kagawa University.
This article originally appeared in the December issue of Design007 Magazine in the FLEX007 section.
More Columns from EPTE Newsletter
EPTE Newsletter: Travel to Japan During COVIDEPTE Newsletter: A New COVID Surge in Taiwan?
EPTE Newsletter: COVID-19 PCR Test in Japan
EPTE Newsletter: Japan Failing in Vaccine Distribution
EPTE Newsletter: A Long Trip to the U.S.
EPTE Newsletter: Ten Years After Fukushima
EPTE Newsletter: Taiwan Releases 2020 PCB Production Numbers
EPTE Newsletter: The Printed Circuit Industry in China