Estimated reading time: 5 minutes
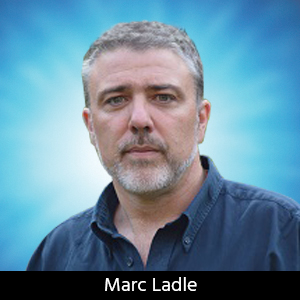
Ladle on Manufacturing: LED UV Cure—Does It Really Work?
Machines that have been made to UV cure inks used in printed circuits and other manufacturing processes have largely used vapour lamps as the UV light source since the earliest development of UV-cured materials. Typically, vapour bulbs contain a proportion of mercury, which is in the process of undergoing a worldwide ban. In turn, this means that alternative UV light sources with enough power to complete the UV curing process have a very clear commercial interest.
The development of the photoinitiators, which are the components in UV ink that enable cure when exposed to UV light, was based on the best UV source available at the time. If you want to guarantee that you will achieve exactly the same result when you switch light sources, you will need to accurately mimic the output of the vapour bulb in both spectrum and intensity.
In the search for good alternatives, LED technology has been hovering in the background, but for a number of reasons, it has struggled to position itself as a serious contender.
UV LEDs have worked well for the photoimage exposure of dry film and solder mask, and there are quite a number of established machines available for this purpose. I have set a few of these machines up at customer factories, and the empirical test methods—such as using step wedges to control the exposure power—work much better when assessing the output of the LEDs. The good results from the LED exposure machines suggest that the same LED method should be suitable for other UV light processes, such as bump of solder mask (additional exposure after developing the photoimageable mask) to make the ink more robust for the aggressive chemical and heat processes that some circuits are subjected to as part of their manufacturing process.
It is quite hard to make a direct comparison of vapour bulb and LED machines due to the difference in the spectrum available. A vapour bulb has a wide spectrum of output with strong spikes that can be controlled by different doping of the bulb. An LED has a single distinct output wavelength, so even the tools available to measure intensity and exposure power may not give a very true reading of the LED’s output, as these tools were designed for use with vapour bulbs.
A little reading about the subject of UV curing of solder mask reveals that different wavelengths can have a different effect on the ink. The exact wavelength can have quite an effect on the penetration through the depth of the mask material. Longer wavelengths penetrate deeper, and short wavelengths are good for surface cure. A vapour lamp covers this with a wide variety of available wavelengths, but there is no possible control of the proportions of long and short wavelengths once you have selected a bulb. All that is possible in terms of adjustment is to vary the power. Over time, each bulb degrades and also loses some intensity, which means that a pattern of constant adjustment has to be followed over the life cycle of the bulb to ensure the effect on the product is within the acceptable range.
With UV LED, we have to deal with the problem of distinct wavelengths, but thankfully, a variety of types are available—namely 365, 385, 395, 405, and 415 nanometres. If these are arranged and connected in the right way, it is possible to control the proportion of each wavelength, which allows you to tune the output to suit individual products and ink application methods—a level of control that has never been available with vapour bulbs.
After some amount of research and development, one of my colleagues in China produced what we believe will be an LED-powered machine suitable for bump processing of photoimageable solder mask, as well as cure of other UV curable inks. Finding a place to make empirical tests, however, proved to be very difficult.
Finding a potential end-user for a machine like this is reasonably easy, but for obvious reasons, they are always very keen to make sure their UV ink supplier is happy with the proposed change of equipment. When you do this for the first time, nobody is able to say with any level of certainty that it will work.
I did talk directly to the ink supplier, and they were extremely helpful but also quite skeptical that it would be possible to get a positive result. It seems that poor past experience of LED-based curing had galvanised opinions against this format of machine.
There is no substitute for testing on real products, and in this respect, Merlin Circuits in North Wales has been a huge help. They have run the machine alongside their old vapour lamp machine and made a true side by side comparison with testing and verification of the results being made by their UV ink supplier. The target for the company I work for is to sell these machines, but the results we have seen from the testing work at Merlin Circuits (Table 1) have raised some points which may have some wider technical interest.
The results for the LED machine were all good when running at 1 m per minute and 2 m per minute, but one of the adhesion test results was poor when running at 3 m per minute. This is not surprising, as the processing speed was quite extreme for a machine formatted with only two LED light bars (Figure 1). The modular design approach means that an appropriate number of bars could be fitted if higher speeds are important to the user.
One interesting result from the trial was the difference between vapour bulb and LED machine with regard to printing component ident onto the panels. The panels were UV bumped on both types of machines and then printed with component ident. There was a notable difference in ident adhesion between the two processes. The ident did not adhere well on the panels processed with the vapour lamp machine (Figure 2), but the adhesion was very good on panels processed with the LED machine (Figure 3).
The significance of this result is that the LED machine has the potential to be fitted directly to the end of the solder mask developer, greatly simplifying the process route. The component ident will still adhere well to the panels. When processed with the vapour bulb, the panels have to be notated after developing and then run through the UV bump as a separate stand-alone operation.
I spoke again to the ink supplier after the tests had been completed, and he told me they were very impressed with the results. In all tests, the LED machine performed well and achieved a good level of cure. For all parties involved, this was certainly a big step forward. Some of the potential advantages of LED-based machines are obvious—such as the low power usage and long service life of the light source—but without good process results, there is no way forward.
If you are concerned about the ongoing availability of vapour lamps, then perhaps the future is a little brighter when it is lit with UV LEDs.
This column originally appeared in the July 2020 issue of PCB007 Magazine.
More Columns from Ladle on Manufacturing
Ladle on Manufacturing: UV Cure LED Energy SaverLadle on Manufacturing: Sharing an Idea for Christmas
Ladle on Manufacturing: Behind the Scenes at productronica 2019
Ladle on Manufacturing: Sunday Afternoon in Dongguan
The Travelling Engineer, Installment 2
Ladle on Manufacturing: VCP—The Future of Plating
Developments in Wet Processing: Beyond Spraying and Dipping
Ladle on Manufacturing: What’s New?